Abstract
Ce manuscrit décrit la fabrication de micro-aiguilles polymère (MN) tableaux par photolithographie. Elle implique un processus libre de moule simple en utilisant un photomasque constitué de micro-lentilles embarqués. Micro-lentilles embarqués ont influencé la géométrie MN (netteté). Tableaux MN robustes avec des diamètres de pointe allant de 41,5 ± 8,4 um um et 71,6 um ± 13,7 pm, avec deux longueurs différentes (1 336 um ± 193 um et 957 um ± 171 um) ont été fabriqués. Ces tableaux de MN peuvent fournir des applications potentielles dans la livraison d'agents thérapeutiques moléculaire et macromoléculaire bas à travers la peau.
Introduction
Administration transdermique de médicament offre une approche alternative intéressante pour l'administration de médicaments, en particulier pour les biomolécules, qui sont presque exclusivement administrés par injections hypodermiques. Cependant, la peau, en particulier la couche supérieure (la couche cornée), est une formidable barrière empêchant molécules exogènes de pénétrer dans le corps humain. Récemment, des dispositifs MN ont émergé comme des outils permettant de livrer des médicaments à travers la peau. Les dispositifs de MN créer des pores temporaires à l'intérieur de la couche cornée pour permettre le passage de molécules de médicament d'atteindre l'activité physiologique désirée avec une meilleure observance des patients et la commodité 1-3.
Diverses méthodes de fabrication ont été adoptées pour fabriquer des polymères MNs 4. Cependant, ils impliquent généralement des processus étape complexes et multiples nécessitant des temps longs et / ou des températures élevées pour fabriquer des réseaux MNS. 4 Pour simplifier le processus de fabrication, un processus libre de moule en une seule étape à l'aideun photomasque a été développé récemment 5,6. Cependant, avec cette méthode, fabriqué MNs avaient pointes d'aiguilles émoussées, comme aucun mécanisme n'a été mis en place pour modifier le chemin ultraviolet (UV) impliqués dans la photolithographie.
Dans cette étude, des microlentilles intégrées dans le photomasque ont été proposées pour définir la géométrie des MNs. Le protocole de fabriquer des masques constitués de microlentilles embarqués et ensuite mn fabrication avec des conseils pointus en utilisant le photomasque sont signalés.
Subscription Required. Please recommend JoVE to your librarian.
Protocol
1. Fabrication du masque
- Nettoyer une tranche 4 "de verre avec une solution piranha (H 2 SO 4 / H 2 O 2 à 2: 1) pendant 20 min à 120 ° C par immersion dans une cuve en quartz.
- Déposer une couche de chrome / or (30 nm de Cr / Au de 1 um) sur la couche de la plaquette de verre en utilisant un faisceau d'électrons évaporateur 7 (figure 1A).
- Placez les tranches dans un évaporateur à faisceau électronique. Une fois que le vide atteint 5 x 10 -6 Torr, allumer la source de haute tension (10 kV). Contrôler l'épaisseur par le panneau de contrôle du moniteur.
- Pré-propre chaque matériau pendant 30 secondes à l'aide du canon à faisceau d'électrons, en maintenant l'obturateur "OFF" (afin d'éviter le dépôt sur les plaquettes).
- Générer une couche Cr / Au résine photosensible de masquage pour gravure humide profonde du verre.
- Appliquer une résine photosensible épaisse 2 pm par filage 5 ml de la solution pendant 30 secondes à 3000 tours par minute en utilisant un système de couchage spin-pulvérisation.Précuisson de la résine photosensible sur une plaque chauffante à 100 ° C pendant 1,5 min.
- Exposer et faire cuire dur la résine photosensible à 120 ° C pendant 30 min sur une plaque chauffante. Il est essentiel de produire une surface hydrophobe et une forte adhérence de la résine photosensible sur la couche de métal. Motif de la couche de Cr / Au utilisant Cr et Au décapants à travers la résine photosensible masque 8,9.
- Pour la protection de la surface de verre non à motifs, lier temporairement la plaquette de verre à une plaquette de silicium factice. 9
- Placer la plaque de verre sur une plaque chaude à 110 ° C et faire fondre la cire sur le côté opposé de la plaque de verre (d'une manière telle que toute la surface de la plaquette est recouverte avec de la cire).
- Placez une tranche de silicium mannequin en contact avec la plaquette de verre et appuyez sur pour enlever la cire excès. Afin d'éviter de renverser de la cire, placez un papier tissu de salle blanche sur la plaque chauffante.
- Effectuer une gravure isotrope de la lentille au moyen d'acide fluorhydrique optimisé (49% v / v)et de l'acide chlorhydrique (37% v / v) de solution (dans un rapport volumétrique de 10: 1). avec un agitateur magnétique pendant 10 min 8,5 Présence du HCl est essentiel pour parvenir à une bonne qualité de surface des lentilles produites de.
- Assurez-vous que la vitesse de gravure est de 7 pm / min; en utilisant un volume total de 200 ml de solution de gravure. Effectuer gravure dans un récipient en plastique et de prendre les précautions de sécurité pour cette étape de traitement.
- Nettoyez la galette dans la (DI) de l'eau déminéralisée d'un rinçage et un séchage supplémentaire à la température ambiante.
- Après l'achèvement du procédé, de séparer la tranche de verre à partir de la tranche de silicium factice et réchauffer la cire en utilisant une plaque chaude à 100 ° C pendant 15 s. Comme la cire fond à cette température, détacher la tranche de verre à partir de la tranche de silicium factice.
- Retirer le reste de la cire, la résine photosensible et le surplomb Cr / Au couches sur les bords de la lentille en utilisant ultrasonication pendant 1 heure en utilisant du N-méthyl-2-pyrrolidone comme solvant à 80 ° C dans une cuve à ultrasons.
- Créer un moule PDMS réplique des microlentilles fabriquées sur les photomasques 11.
- Caractériser les dimensions de photomasques (longueur et largeur) et le moule microlentilles PDMS (profondeur et le diamètre) des répliques en utilisant un microscope électronique à balayage et stéréomicroscope respectivement. 12-14
2. Arbres MN Fabrication
- Créer une cavité de 2,5 cm x 0,9 cm à l'aide des lames de verre montées de part et d'autre d'un verre. Le nombre des lames de verre empilées part et d'autre détermine la hauteur de la cavité dite épaisseur d'espacement (figure 1B).
- Fixer chaque couche de la lame de verre par application d'une mince couche de la solution de prépolymère contenant du poly (éthylène glycol) diacrylate (PEGDA, MW = 258 Da) avec 0,5% en poids / poids de 2-hydroxy-2-méthyl-propiophénone (HMP) sur la lame de verre suivie d'une irradiation de la lumière mis en place avec l'ultraviolet de haute intensité (UV) pendant 2 secondes.
- Placez le Photomask (fabriqué précédemment) avec les surfaces de Cr / Au revêtus face à l'intérieur de la cavité. Faire en sorte que les côtés des parois de la cavité ne sont pas obscurcir la lentilles noyées dans le photomasque.
- Remplir la cavité avec la solution de prépolymère jusqu'à ce que la surface revêtue Cr / Au est en contact avec la solution sans bulles visibles.
- Irradier la configuration à haute intensité de la lumière UV d'une intensité souhaitée pendant 1 s à une distance de 3,5 cm de la source UV en utilisant la station de séchage UV avec une gamme de filtre UV de 320-500 nm. Utilisez un adaptateur collimateur avec la sonde de la lumière UV.
- Mesurer l'intensité de la lumière UV utilisée en utilisant un radiomètre.
- Suite à l'exposition aux UV, retirer le photomasque avec le tableau de MNs. Verser la solution de prépolymère en excès qui est polymérisé pas dans le processus de retour dans son emballage d'origine pour une réutilisation.
- Quantifier le diamètre des MNs l'aide d'un microscope stéréoscopique selon les instructions du fabricant longueur ni les pourboires.
- Avec une pince, placer les MNs (fabriqué précédemment) fixé sur le photomasque dans un puits d'une plaque à 24 puits comme indiqué dans la Figure 1C.
- Ajouter un volume donné (300 - 400 pi) de la solution de prépolymère dans le puits jusqu'à ce que les aiguilles sont immergées à une hauteur désirée. Ce volume détermine l'épaisseur de la couche de support qui en résulte.
- Irradier la configuration de lumière de haute intensité UV (15,1 W / cm 2), à une distance de 10,5 cm de la source d'UV pour une durée de 1 sec.
- Séparer la couche de support sur le tableau MN du photomasque utilisant une lame tranchante.
- Quantifier le diamètre longueur, le diamètre et la base pointe des MNs avec la couche de support en utilisant un stéréomicroscope selon les instructions du fabricant.
Subscription Required. Please recommend JoVE to your librarian.
Representative Results
La géométrie des MNs peut être significativement affectée par les caractéristiques de photomasques et microlentille embarqués. Le degré de réfraction affecte le trajet de transmission des rayons UV, qui ont influencé la géométrie de MN (figure 2A). Chaque microlentille a été trouvé pour avoir un diamètre de 350 um, 130 um aplatis une surface convexe, et une profondeur de 62,3 um (figure 2B-D). En utilisant le théorème de Pythagore, le rayon de courbure de la première surface a été jugée 272,89 pm. La longueur focale a été calculée à 509,28 um (considérant n = 1,53627 verre; n air = 1.000; λ = 365 nm) par l'intermédiaire de l'équation lentille maker 12 comme indiqué ci-dessous:
1 / f = (n 1 / n m -1) * (1 / r 1 -1 / r 2)
Où n 1 est l'indice de réfraction du matériau de la lentille, n m est l'indice de réfraction du milieu ambiant, r 1 est le radius de courbure de la première surface, et r 2 est le rayon de courbure de la seconde surface.
L'effet de l'intensité du rayonnement UV sur la longueur du MN, la netteté et la déformation structurale a été étudiée par intensité de la lumière UV à partir de 3,14 ou moins à 15,1 W / cm 2 à une distance focale constante et la distance de la source lumineuse. Il a été constaté que la longueur de MN moyen a augmenté de façon significative (p <0,05) avec une intensité croissante de 3,14 à 9,58 W / cm 2 (figure 3A). D'autres augmentations de l'intensité jusqu'à 15,1 W / cm 2 ne produisent pas de changements significatifs dans la longueur. La pointe de diamètre (mesure de netteté) et la structure de pointe de MN ont été trouvés à varier avec augmentation de l'intensité (figure 3B). MNS avec une forme régulière et sans aucune déformation de la structure ont été observés à 6,4 W / cm 2.
La couche de support a été fabriqué pour permettre le retrait de MN en forme d'un patchet de rendre la réutilisable de photomasques. Il fournit également la résistance aux arbres de MN. Par conséquent, l'effet du volume de la couche de support (le volume de la solution de prépolymère pour former la couche arrière) a également été étudiée. Avec des diamètres de pointe ne sont pas touchés, les MN avec une gamme de la longueur (1336 ± 193 um pour 300 pi et 957 ± 171 um pour 400 pi) ont été observés après l'exposition aux UV (figure 4).
Figure 1. (A) Représentation schématique du procédé de fabrication de lentilles noyées photomasque. (1) 4 "plaquette de verre. (2) Cr / Au couche déposée à l'aide d'un évaporateur à faisceau électronique. (3) L'exposition de Cr / Au / couche de résine photosensible de masquage à la lumière UV avec photomasque. (4) La formation de motif sur la couche en utilisant du Cr / Au décapant. (5) la liaison temporaire de verre sur une tranche de silicium factice. (6) - (7) La gravure humide (isotrope) processus en utilisant des agents de gravure HF / HCl suivi par ultrasons. (8) Le décollement de la plaquette de silicium mannequin et l'enlèvement de la couche de résine photosensible. (B) Représentation schématique du procédé de fabrication d'aiguilles. Le chrome revêtu photomasque (9 x 9 de réseaux), est placé sur une cavité contenant une solution de pré-polymère et exposé aux UV. (C) Représentation schématique du procédé de fabrication de la couche de support. Photomask, avec micro-aiguilles attachées, est placé dans un puits rempli de pré-polymère et exposée aux UV. S'il vous plaît cliquer ici pour voir une version plus grande de cette figure.
Figure 2. Caractérisation des photomasques. (A) l'exposition aux UV concentre la lumière dans un conica l chemin, en produisant MNs coniques. (B) et (C) Une image MEB d'une microlentille. (D) Une partie d'un ensemble de répliques de moule PDMS copiées à partir de micro-lentilles, qui montre la surface convexe aplati sous un stéréomicroscope. (E) Un photomasque montrant le schéma. S'il vous plaît cliquer ici pour voir une version plus grande de cette figure.
Figure 3. Effet des paramètres UV sur la géométrie de micro-aiguille. Effet de (A) et l'intensité (B) d'épaisseur d'écartement de la longueur du micro-aiguille. S'il vous plaît cliquer ici pour voir une version plus grande de cette figure.
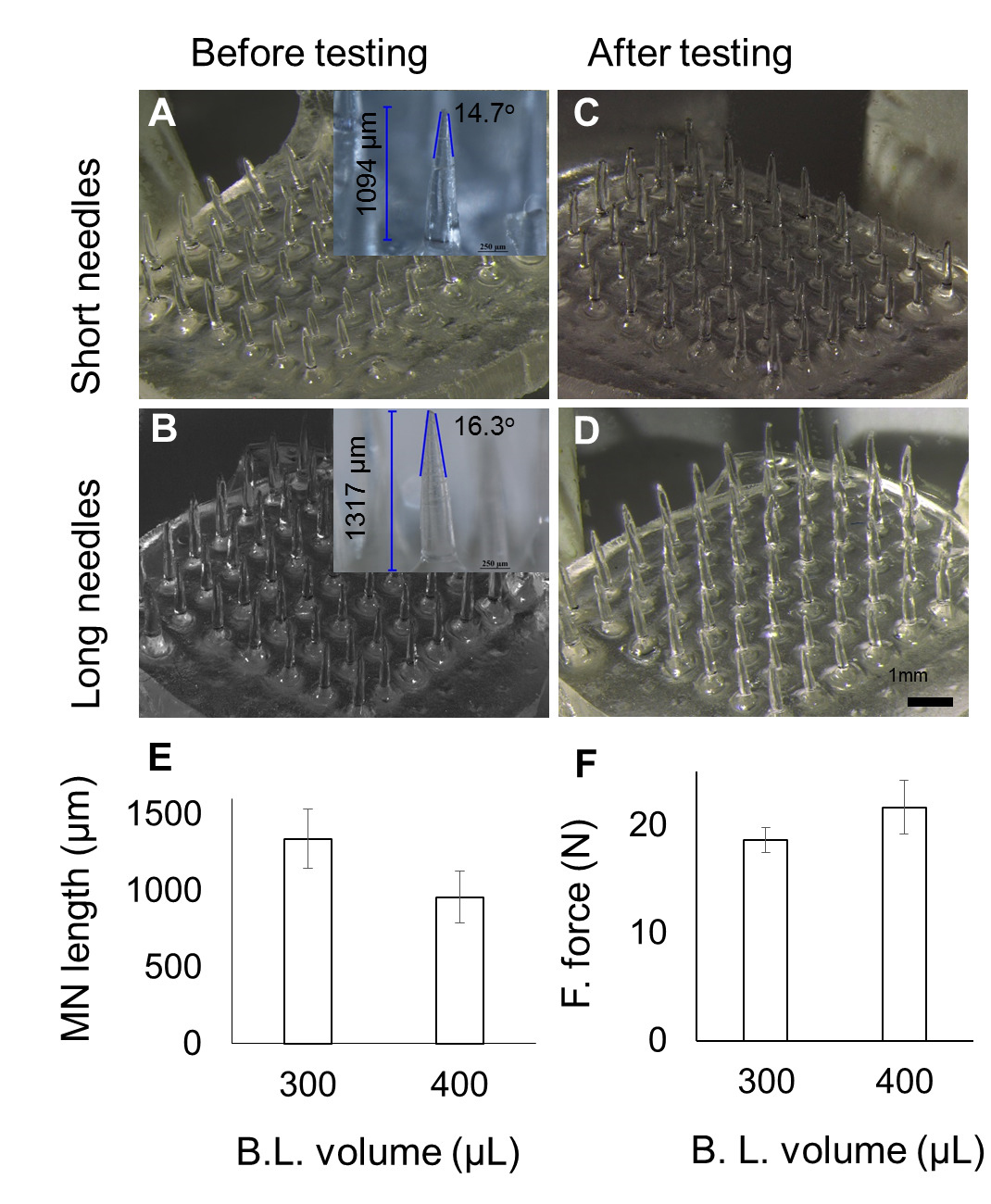
Figure 4. Effet de la variation de volume de pré-polymère utilisé pour la couche de support fabrication. (A - B) des images à divers capacités, avec une longueur moyenne de courts MN (957 pm) et longs (1 336 pm) MNs. (C - D) Images correspondant à (AB) après le test de force de fracture. (E) diminution de la longueur MN avec augmentation du volume utilisé pour la couche de support de fabrication. Force de fracture (F) MN à travers les deux volumes pré-polymères utilisés pour fabriquer couche de support (BL). S'il vous plaît cliquer ici pour voir une version plus grande de cette figure.
Subscription Required. Please recommend JoVE to your librarian.
Discussion
Le protocole décrit ci-dessus pour la fabrication de la matrice MNs a été présenté pour la fabrication de la matrice de MNs ~ 1 cm 2. Les réseaux peuvent être mis à l'échelle par la création d'une cavité de grande taille et en utilisant un photomasque plus grande. L'augmentation de la taille de la cavité peut être créée par l'augmentation de la largeur entre les entretoises de chaque côté. Bien que chaque étape pour fabriquer les tableaux de Mn dans le protocole était important, les étapes les plus cruciales étaient: le positionnement de photomasques, le remplissage de la solution de prépolymère, et l'irradiation de l'installation. Positionnement du photomasque doit être de telle sorte que les surfaces de Cr / Au revêtues font face à l'intérieur de la cavité et les côtés des parois de la cavité occulter les lentilles noyées dans le photomasque. Lors du remplissage du moule avec la solution de prépolymère, veiller à ce que des bulles d'air ne sont pas piégés qui peut sinon conduire à un tableau force MN déformé et faible. Les bulles d'air peuvent être évitées grâce à une action de pénétration capillaire contrôlé en ajoutant lentement la prepolymesolution de r et assurer qu'il n'y a pas de bulles d'air présentes dans la solution de prépolymère. Positionnement de la configuration pour l'irradiation devrait être fait d'une manière guidée pour assurer l'exposition aux UV uniforme. Avant l'exposition à la lumière UV, l'installation a été aligné et placé dans la démarcation sur le stand de base.
Les MNs ont été formés en utilisant la photolithographie fortement influencée par la présence de micro-lentilles que l'objectif a donné lieu à une polymérisation dans un trajet convergent, ce qui conduit à la formation des MNs nettes par rapport aux MNs cylindriques formés en utilisant le photomasque plane. Dans le photomasque plane, la lumière UV traverse avec peu de déviation (presque droite) entraînant la formation des MNs cylindriques avec des conseils moins pointus. Alors que dans le photomasque de microlentilles-embarqués, la lumière UV passant à travers les lentilles subi réfraction et en convergence, conduisant à la formation de tranchants MNs à embout. L'équation de la machine à lentille qui a été utilisé en tant que predictive modèle pour approcher la longueur du MN en mettant en corrélation avec la longueur focale de la microlentille a une prédiction de la longueur de trois fois inférieure à la réalité. L'écart peut être dû à la surface convexe aplatie de la microlentille, qui ne permettent pas réfraction de la lumière, comme la lentille convexe classique. 13
Un autre facteur pour la géométrie de MN était l'intensité de la lumière UV. L'intensité de 6,44 W / cm 2 a été choisi parce que les aiguilles produites à cette intensité possédaient une résistance mécanique suffisante pour les applications de la peau. Une autre constatation est liée à l'intensité que chaque incrément de l'intensité UV, la longueur de MN augmente. Ceci pourrait être attribué au sommet plat de la microlentille, qui a permis à certains des rayons lumineux de voyager au-delà du point focal. 14,15 De plus, la mesure de la polymérisation a sa limite, selon la loi de l'inverse du carré de la lumière, dire, la lumière perd de l'énergie que la distanceà partir de la source augmente. 16
Les protocoles décrits ici ont l'avantage de fabrication exempt de moisissures dans un court laps de temps. Mais nous ne pouvons pas prédire dans quelle mesure il peut être pris en outre pour la fabrication en vrac. Les MNS tableaux ont été faites à partir d'un polymère biocompatible à faible coût. Il peut potentiellement être utilisé comme dispositif d'administration transdermique de médicament pour des applications pharmaceutiques et cosmétiques. Plus intéressant encore, il peut être utilisé comme une combinaison du système de délivrance et le dispositif, comme les composés thérapeutiques peuvent être encapsulées (par mélange ou solubilisation dans une solution de prépolymère) lors de la fabrication de MNs. 5,6,17 La solubilité du composé ajouté l'intérieur de la solution de prépolymère doit être pris en considération que les caractéristiques de MN, par exemple, la force MN, peut. modifier 17
Subscription Required. Please recommend JoVE to your librarian.
Materials
Name | Company | Catalog Number | Comments |
Poly(ethylene glycol) diacrylate (PEGDA Mn=258) | SIGMA | 475629-500ML | |
2-hydroxy-2-methyl-propiophenone (HMP) | SIGMA | 405655-50ML | |
Bovine collagen type 1, FITC conjugate | SIGMA | C4361 | |
UV curing station | EXFO Photonic Solutions Inc., Canada | OmniCure S2000-XL | |
Collimating Adaptor | EXFO Photonic Solutions Inc., Canada | EXFO 810-00042 | |
24-well plate | Thermo Fisher Scientific, USA | ||
Nikon SMZ 1500 stereomicroscope | Nikon, Japan | ||
Dillon GL-500 digital force gauge | Dillon, USA | ||
A-1R confocal microscope | Nikon, Japan |
References
- Zhou, C. P., Liu, Y. L., Wang, H. L., Zhang, P. X., Zhang, J. L. Transdermal delivery of insulin using microneedle rollers in vivo. International journal of pharmaceutics. 392, 127-133 (2010).
- Lee, J. W., Choi, S. O., Felner, E. I., Prausnitz, M. R. Dissolving microneedle patch for transdermal delivery of human growth hormone. Small. 7, 531-539 (2011).
- Raphael, A. P., et al. needle-free vaccinations in skin using multi layered, densely-packed dissolving microprojection arrays. Small. 6, 1785-1793 (2010).
- Lee, J. W., Han, M. R., Park, J. H. Polymer microneedles for transdermal drug delivery. Journal of drug targeting. 21, 211-223 (2012).
- Kochhar, J. S., Goh, W. J., Chan, S. Y., Kang, L. A simple method of microneedle array fabrication for transdermal drug delivery. Drug development and industrial pharmacy. 39, 299-309 (2013).
- Kochhar, J. S., Zou, S., Chan, S. Y., Kang, L. Protein encapsulation in polymeric microneedles by photolithography. International journal of nanomedicine. 7, 3143-3154 (2012).
- Tay, F. E. H., Iliescu, C., Jing, J., Miao, J. Defect-free wet etching through pyrex glass using Cr/Au mask. Microsystem Technologies. 12, 935-939 (2006).
- Iliescu, C., Chen, B., Miao, J. On the wet etching of Pyrex glass. Sensors and Actuators, A: Physical. 143, 154-161 (2008).
- Iliescu, C., Taylor, H., Avram, M., Miao, J., Franssila, S. A practical guide for the fabrication of microfluidic devices using glass and silicon. Biomicrofluidics. 6, 16505-16516 (2012).
- Iliescu, C., Jing, J., Tay, F. E. H., Miao, J., Sun, T. Characterization of masking layers for deep wet etching of glass in an improved HF/HCl solution. Surface and Coatings Technology. 198, 314-318 (2005).
- Pan, J., et al. Fabrication of a 3D hair follicle-like hydrogel by soft lithography. Journal of biomedical materials research. Part A. 101, 3159-3169 (2013).
- Jay, T. R., Stern, M. B. Preshaping photoresist for refractive microlens fabrication. P Soc Photo-Opt Ins. 1992, 275-282 (1993).
- Friedman, G. B., Sandhu, H. S. Longitudinal Spherical Aberration of a Thin Lens. Am J Phys. 35, 628 (1967).
- Xu, Q. A., Li, J., Zhang, W. Collimated the laser diode beam by the focus lens. Semiconductor Lasers and Applications IV. 7844, (2010).
- Lin, T. W., Chen, C. F., Yang, J. J., Liao, Y. S. A dual-directional light-control film with a high-sag and high-asymmetrical-shape microlens array fabricated by a UV imprinting process. J Micromech Microeng. 18, (2008).
- Dunne, S. M., Millar, B. J. Effect of distance from curing light tip to restoration surface on depth of cure of composite resin. Prim Dent Care. 15, 147-152 (2008).
- Kochhar, J. S., et al. Microneedle integrated transdermal patch for fast onset and sustained delivery of lidocaine. Molecular pharmaceutics. 10, 4272-4280 (2013).
- Kochhar, J. S., et al. Direct microneedle array fabrication off a photomask to deliver collagen through skin. Pharmaceutical research. 31, 1724-1734 (2014).