Abstract
Diese Handschrift beschreibt die Herstellung von polymeren Mikronadel (MN) Arrays durch Photolithographie. Es geht um eine einfache schimmelfrei Prozesses durch Verwendung einer Photomaske, bestehend aus eingebetteten Mikrolinsen. Eingebettete Mikrolinsen wurden gefunden, um MN-Geometrie (Schärfe) zu beeinflussen. Robusten MN Arrays mit Spitzendurchmessern im Bereich zwischen 41,5 & mgr; m ± 8,4 & mgr; m und 71,6 ± 13,7 & mgr; m & mgr; m, mit zwei verschiedenen Längen (1,336 & mgr; m ± 193 & mgr; m und 957 & mgr; m ± 171 & mgr; m) wurden hergestellt. Diese MN Arrays können potenzielle Anwendungen in der Lieferung von niedermolekularen und makromolekularen therapeutischen Wirkstoffen durch die Haut zu schaffen.
Introduction
Transdermalen Verabreichung von Arzneimitteln bietet eine attraktive Alternative Ansatz für die Arzneimittelverabreichung, insbesondere für Biomoleküle, die fast ausschließlich von subkutanen Injektionen verabreicht werden. Jedoch Haut, insbesondere die Deckschicht (das Stratum corneum) ist eine hervorragende Barriere verhindert exogenen Molekülen von in den menschlichen Körper. Vor kurzem haben MN Geräte ermöglichen Tools, um Arzneimittel durch die Haut zu liefern entstanden. Die MN-Geräte zu erstellen temporäre Poren im Inneren der Hornschicht, damit der Durchgang von Wirkstoffmolekülen, um die gewünschte physiologische Aktivität mit verbesserte Patienten-Compliance und Convenience 1-3 zu erreichen.
Es wurden verschiedene Herstellungsverfahren erlassen, um polymere MNs 4 herzustellen. Aber sie beinhalten in der Regel kompliziert und Mehrschrittverfahren für die langZeiten und / oder hohe Temperaturen, um MNs Arrays herzustellen. 4 Zur Vereinfachung des Herstellungsprozesses, einen einzigen Schritt schimmelfrei Prozess miteine Fotomaske wurde kürzlich 5,6 entwickelt. Doch mit diesem Verfahren hergestellt MNs hatten stumpfe Nadelspitzen, da kein Mechanismus vorhanden, um die ultravioletten (UV) Lichtpfad in der Photolithographie beteiligt zu ändern.
In dieser Studie eingebetteten Mikrolinsen in der Fotomaske vorgeschlagen worden, um die Geometrie der MNs definieren. Das Protokoll zum Photomasken, bestehend aus eingebetteten Mikrolinsen und anschließend MN Fertigung mit scharfen Spitzen Verwendung der Fotomaske wird berichtet, zu fertigen.
Subscription Required. Please recommend JoVE to your librarian.
Protocol
1. Fotomasken Fabrication
- Reinigen einer 4 "Glaswafer mit Piranha-Lösung (H 2 SO 4 / H 2 O 2 in Verhältnis 2: 1) für 20 min bei 120 ° C durch Eintauchen in einen Quarzbehälter.
- Hinterlegung einer Schicht aus Chrom / Gold (30 nm Cr / 1 & mgr; m Au) -Schicht auf der Glasscheibe unter Verwendung eines E-Strahl-Verdampfer 7 (1A).
- Platzieren der Scheiben in einer e-Strahl-Verdampfer. Sobald das Vakuum erreicht 5 x 10 -6 Torr, schalten Sie die Hochspannungsquelle (10 kV). Steuern Sie die Dicke von dem Monitor Bedienfeld.
- Vorreinigen jedes Material für 30 Sekunden mit der E-Strahlkanone, wobei die Verschluss "OFF" (in der Reihenfolge, um die Ablagerung auf den Wafern zu vermeiden).
- Generieren Sie eine Cr / Au Photoresist Maskierungsschicht für tiefen Nassätzen des Glases.
- Anwenden einer 2 um dicken Photoresist durch Schleudern 5 ml der Lösung für 30 sec bei 3.000 UpM unter Verwendung eines Spin-Sprühbeschichtungsvorrichtung Systems.Vorbacken des Photoresists auf einer Heizplatte bei 100 ° C für 1,5 min.
- Expose und harte Backen des Photoresist bei 120 ° C für 30 min auf einer Heizplatte. Es ist kritisch, um eine hydrophobe Oberfläche und eine starke Haftung des Photoresists auf die Metallschicht zu erzeugen. Muster der Cr / Au-Schicht unter Verwendung von Cr und Au Ätzmittel durch die Fotolackmaske 8,9.
- Zum Schutz der un-gemusterten Glasoberfläche vorübergehend verbinden die Glasscheibe auf eine Dummy-Silizium-Wafer. 9
- Platzieren der Glaswafer auf einer heißen Platte bei 110 ° C schmilzt das Wachs auf der gegenüberliegenden Seite der Glasscheibe (in der Weise, dass die gesamte Oberfläche des Wafers mit Wachs).
- Legen Sie eine Dummy-Silizium-Wafer in Kontakt mit der Glasscheibe und drücken Sie, um das überschüssige Wachs zu entfernen. Um Auslaufen des Wachses zu vermeiden, legen Sie ein sauberes Zimmer Tissue-Papier auf der Heizplatte.
- Zuführen isotropes Ätzen der Linse mit optimierten Flusssäure (49% v / v)und Salzsäure (37% v / v) Lösung (in einem Volumenverhältnis von 10: 1). mit einem magnetischen Rührer für 8,5 min 10 Anwesenheit des HCl ist kritisch bei der Erzielung einer guten Oberflächenqualität der erzeugten Linsen.
- Stellen Sie sicher, dass die Ätzrate 7 & mgr; m / min; mit einem Gesamtvolumen von 200 ml Ätzlösung. Führen Ätzen in einem Kunststoffbehälter und nehmen Sie Sicherheitsmaßnahme für diesen Verarbeitungsschritt.
- Reinigen des Wafers in dem deionisiertem Wasser (DI) gespült und eine weitere Trocknung bei RT.
- Nachdem der Prozess abgeschlossen, trennen Sie die Glasscheibe von der Dummy-Silizium-Wafer und erwärmen Sie das Wachs unter Verwendung einer Heizplatte bei 100 ° C für 15 Sekunden. Wie das Wachs bei dieser Temperatur schmilzt, nehmen Sie den Glaswafer von dem Dummy-Silizium-Wafer.
- Entfernen restlichen Wachs, das Photoresist und die überhängenden Cr / Au-Schichten an den Rändern der Linsen mit Ultraschall für 1 Stunde unter Verwendung von N-Methyl-2-pyrrolidon als Lösungsmittel bei 80 ° C in einem Ultraschalltank.
- Erstellen Sie eine PDMS-Form Replik der Mikrolinsen auf den Photomasken 11 hergestellt.
- Charakterisierung der Photomaske Abmessungen (Länge und Breite) und der Mikrolinsen PDMS-Form (Tiefe und Durchmesser) Nachbildungen mit einem Rasterelektronenmikroskop und Stereo jeweils 12-14.
2. MN Wellen Fabrication
- Erzeugen einen Hohlraum von 2,5 cm × 0,9 cm mit den Glasobjektträger auf beiden Seiten eines Glas montiert. Die Anzahl von Objektträgern auf jeder Seite gestapelt wird die Höhe des Hohlraums, wie Abstandshalterdicke (1B) bekannt bestimmen.
- Sicherung jede Schicht des Glasobjektträgers durch Aufbringen einer dünnen Schicht der Präpolymerlösung, die Poly (ethylenglycol) diacrylat (PEGDA, Mw = 258 Da) mit 0,5% w / w 2-Hydroxy-2-methyl-propiophenon (HMP) auf die Glasobjektträger, gefolgt von Bestrahlung des mit dem hochintensiven UV-Set (UV) Licht für 2 sec.
- Positionieren Sie den Photomask (zuvor hergestellt) mit dem Cr / Au beschichteten Oberflächen des Inneren des Hohlraums gegenüber. Sicherzustellen, dass die Seiten der Hohlwände sind nicht verdecken die Linsen in der Fotomaske eingebettet.
- Füllen des Hohlraums mit der Präpolymerlösung bis die Cr / Au-beschichtete Oberfläche in Kontakt mit der Lösung ohne sichtbare Blasen.
- Bestrahlen die Einrichtung mit hoher Intensität, UV-Licht einer gewünschten Intensität für 1 sec in einem Abstand von 3,5 cm von der UV-Quelle mit der Vernetzungsstation mit einem UV-Filter-Bereich von 320-500 nm. Verwenden Sie einen Kollimator-Adapter mit dem UV-Licht-Sonde.
- Messen Sie die Intensität der UV-Licht unter Verwendung eines Radiometer verwendet.
- Nach der UV-Bestrahlung, entfernen Sie die Fotomaske mit dem Array von MNs. Gießen Sie das überschüssige Präpolymerlösung, die nicht in den Prozess wieder in der Originalverpackung zur Wiederverwendung polymerisiert wird.
- Quantifizierung der Länge und Durchmesser der Spitze von MnS mit einem Stereomikroskop nach den Anweisungen des Herstellers.
- Mit einer Pinzette, legen die MNs (vorher hergestellt) auf die Photomaske in eine Vertiefung einer Platte mit 24 Vertiefungen angebracht, wie in der 1C gezeigt.
- Hinzufügen eines festgelegten Volumens (300 bis 400 & mgr; l) der Prepolymer-Lösung in das Bohrloch, bis die Nadeln bis zu einer gewünschten Höhe eingetaucht ist. Dieses Volumen bestimmt die Dicke der resultierenden Trägerschicht.
- Bestrahlen die Einrichtung mit hoher Intensität, UV-Licht (15,1 W / cm 2), 10,5 cm von der UV-Quelle für eine Zeitdauer von 1 sec.
- Trennen Sie die Rückschicht auf der MN-Array von der Photomaske mit einer scharfen Klinge.
- Quantifizierung der Durchmesser der MNs Länge, Durchmesser und die Basis mit der Rückschicht mit einem Stereomikroskop nach den Anweisungen des Herstellers.
Subscription Required. Please recommend JoVE to your librarian.
Representative Results
Die Geometrie der MNs können durch die Photomaske Eigenschaften und eingebettete Mikrolinsen erheblich beeinflusst werden. Der Brechungsgrad beeinflusst den Übertragungsweg der UV-Strahlen, die den MN-Geometrie (2A) beeinflusst. Jede Mikrolinse hatte einen Durchmesser von 350 um, 130 um eine abgeflachte konvexe Oberfläche und eine 62,3 & mgr; m Tiefe (2B-D). Verwendung des Satz des Pythagoras, wurde der Krümmungsradius der ersten Fläche festgestellt, 272.89 um sein. Die Brennweite wurde berechnet, 509,28 & mgr; m (gemessen an n Glas = 1,53627; n Luft = 1.000; λ = 365 nm) über die Linse maker Gleichung 12, wie unten angegeben:
1 / f = (n 1 / n m -1) * (1 / r 1 -1 / R 2)
Wobei n 1 der Brechungsindex des Linsenmaterials n m der Brechungsindex des umgebenden Mediums ist, r 1 der RADIUs Krümmung der ersten Oberfläche ist und r 2 der Radius der Krümmung der zweiten Oberfläche.
Die Wirkung der UV-Intensität auf der MN Länge, Schärfe und strukturelle Deformation wurde durch Variieren Intensität des UV-Lichtes von 3,14 bis 15,1 W / cm 2 bei einer konstanten Brennweite und Abstand Lichtquelle untersucht. Es wurde festgestellt, dass die durchschnittliche Länge MN signifikant erhöht (p <0,05) mit zunehmender Intensität 3,14-9,58 W / cm 2 (3A). Weitere Erhöhung der Intensität von bis zu 15,1 W / cm 2 nicht zu signifikanten Änderungen in der Länge. Der Spitzendurchmesser (Maß für die Bildschärfe) und der MN Spitzenstruktur wurde gefunden, dass mit einer Erhöhung der Intensität (3B) variieren. Die MNs mit einer regelmäßigen Form und ohne jede strukturelle Deformation wurden bei 6,4 W / cm 2 beobachtet.
Die Rückschicht wurde hergestellt, um die Entfernung von Mangan in Form eines Pflasters Freigabeund die Photomaske wiederverwendbar zu machen. Auch vorgesehen Stärke zu den MN Wellen. Daher wurde die Wirkung der Unterschicht (das Volumen des Prepolymeren Lösungen, um die Rückenschicht zu bilden) ebenfalls untersucht. Mit nicht-betroffenen Spitzendurchmesser wurden die MNs mit einem Bereich der Länge (1.336 ± 193 & mgr; m 300 & mgr; l und 957 ± 171 & mgr; m 400 & mgr; l) nach der UV-Bestrahlung (4) beobachtet.
Abbildung 1. (A) Schematische Darstellung des Herstellungsprozesses von Linsen eingebetteten Photomaske. (1) 4 "Glaswafer. (2) Cr / Au-Schicht abgeschieden unter Verwendung eines Elektronenstrahlverdampfer. (3) Die Exposition von Cr / Au / Photoresist-Maskierungsschicht mit UV-Licht mit Photomaske. (4) Bildung des Musters auf der Schicht mit Cr / Au-Ätzmittel. (5) temporäre Bindung von Glas an einem Dummy Siliziumwafer. (6) - (7) Nassätzen (isotrop) Verfahren unter Verwendung von HF / HCl Ätzmittel, gefolgt von Ultraschallbehandlung. (8) Debonding von Dummy-Siliciumscheibe und Entfernung der Photolackschicht. (B) Schematische Darstellung des Herstellungsprozesses der Nadeln. Chrom beschichteten Fotomaske (9 x 9-Arrays), wird über einen Hohlraum enthält Präpolymerlösung gegeben und UV ausgesetzt. (C) Schematische Darstellung des Herstellungsverfahrens der Trägerschicht. Photomaske, mit Mikronadeln befestigt ist, wird in ein gut platziert mit Pre-Polymer gefüllt und UV ausgesetzt sind. Bitte klicken Sie hier, um eine größere Version dieser Figur zu sehen.
Abbildung 2. Charakterisierung der Photomaske. (A) UV-Belichtung fokussiert Licht in eine conica l Pfad, wodurch sich verjüngenden MNs. (B) und (C) Ein SEM-Bild einer Mikrolinse. (D) Ein Teil eines Arrays von PDMS-Replikas von den Mikrolinsen kopiert, welche den abgeflachten konvexen Oberfläche, unter einem Stereomikroskop. (E) Eine Photomaske, die das Muster. Bitte klicken Sie hier, um eine größere Version dieser Figur zu sehen.
Abbildung 3. Einfluss von UV-Parametern auf Mikronadelgeometrie. Wirkung von (A) Intensität und (B) Abstandshalterdicke auf Mikronadellänge. Bitte klicken Sie hier, um eine größere Version dieser Figur zu sehen.
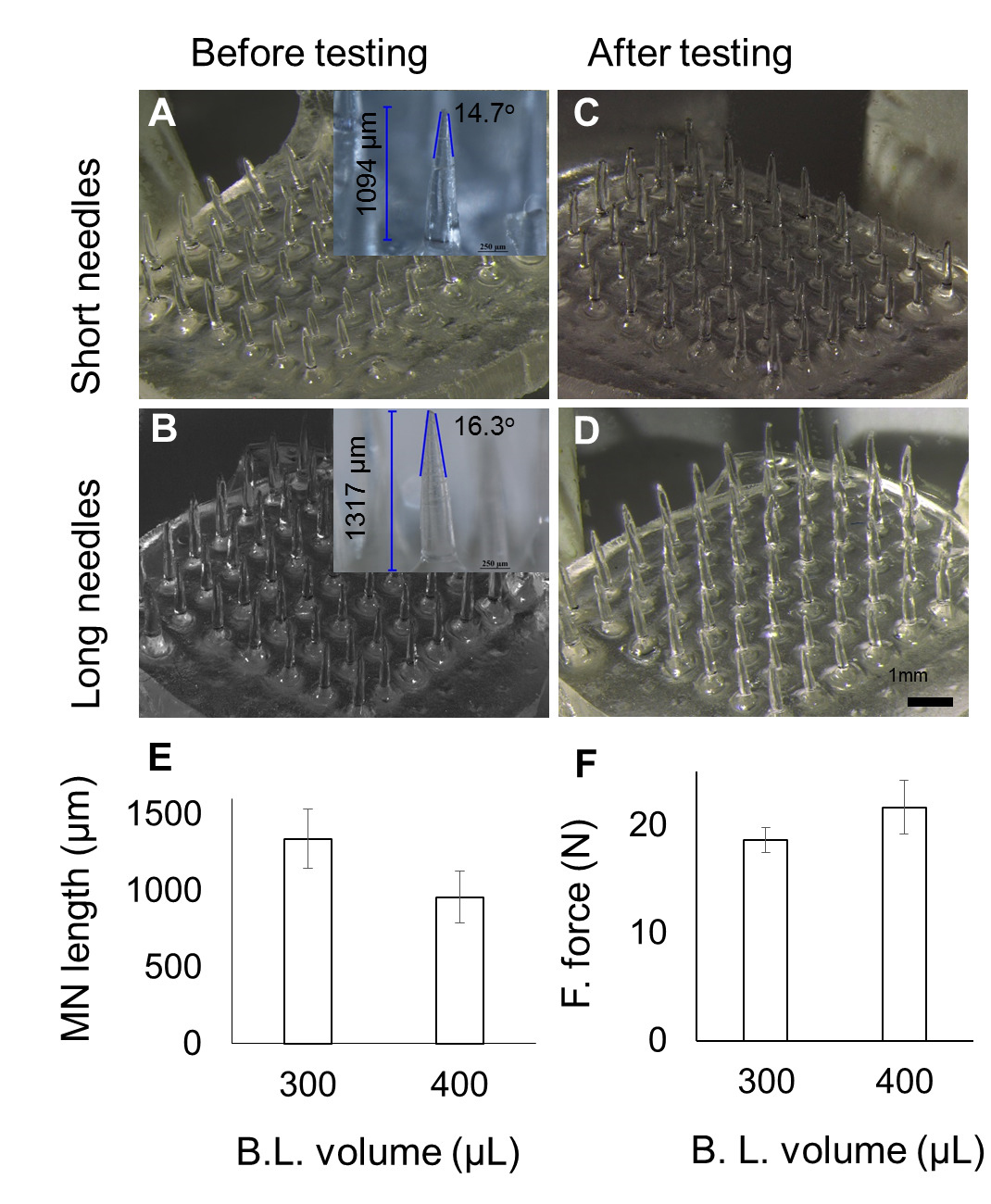
Figur 4. Wirkung von variierenden Vorpolymers Volumen Trägerschicht Herstellung verwendet. (A - B) Bilder bei verschiedenen Volumen, mit durchschnittlichen MN Länge für kurze (957 um) und lang (1,336 um) MNs. (C - D) Bilder entsprechend (AB) Bruchkraft-Tests. (E) Abnahme der MN Länge mit Zunahme des Volumens für die Trägerschicht Herstellung verwendet. (F) MN Bruchkraft über die beiden zur Trägerschicht (BL) zu fertigen Prepolymer Bände. Bitte klicken Sie hier, um eine größere Version dieser Figur zu sehen.
Subscription Required. Please recommend JoVE to your librarian.
Discussion
Die oben für die Herstellung des MNs Array beschriebenen Protokoll wurde vorgestellt, um die MNs Array von ~ 1 cm 2 herzustellen. Die Arrays können durch die Schaffung eines großen Hohlraums und durch die Verwendung eines größeren Photomaske skaliert werden. Die erhöhte Hohlraumgröße kann durch Erhöhung der Breite zwischen den Abstandshaltern auf beiden Seiten erzeugt werden. Wenn jeder Schritt die MN-Arrays im Protokoll herstellen wichtig war, waren die wichtigsten Schritte: die Fotomaske Positionierung, das Füllen der Prepolymer-Lösung und die Bestrahlung des Aufbaus. Positionierung der Photomaske sollte in einer Weise, dass die Cr / Au-beschichteten Oberflächen nach innen zeigen den Hohlraum und an den Seiten der Hohlwände verdeckt die Linsen in der Photomaske eingebettet werden. Beim Füllen der Form mit der Präpolymerlösung, sorgen dafür, dass keine Luftblasen eingeschlossen, die sonst zu einer deformierten und geringe Festigkeit MN Array führen kann. Die Luftblasen können durch eine kontrollierte Saugwirkung durch langsame Zugabe des prepolyme verhindert werdenr-Lösung und die Sicherstellung, dass es keine in der Präpolymer-Lösung Luftblasen. Positionierung des Setup für die Bestrahlung sollte in einer geführten Weise durchgeführt werden, um eine einheitliche UV-Exposition zu gewährleisten. Vor der Belichtung mit UV-Licht wurde die Anordnung ausgerichtet sind und innerhalb der Abgrenzung auf dem Basisständer angeordnet.
Die Verwendung der Photolithographie gebildet MNs wurden stark durch die Anwesenheit von Mikrolinsen geprägt, wenn die Linse zur Polymerisierung in einem konvergenten Weg, der zur Bildung der schärferen MNs führte im Vergleich zu den zylindrischen MNs unter Verwendung der planaren Fotomaske gebildet. Im planaren Photomaske durchläuft die UV-Licht durch sie mit wenig Abweichung (fast gerade), was zur Bildung der zylindrischen MNs mit weniger scharfen Spitzen. Während in dem Mikrolinsen-eingebetteten Fotomaske, die UV-Licht, das durch die Linsen unter Brechung und konvergiert wird, was zur Bildung von scharfen Spitzen versehenen MNs. Gleichung Die Linsen Herstellers der als predicti verwendet wurde,ve Modell, um die Länge des MN durch Korrelation mit der Brennweite der Mikrolinse annähern ergab eine Vorhersage der Länge dreimal weniger als die tatsächliche. Die Diskrepanz kann aufgrund der abgeflachten konvexen Oberfläche der Mikrolinse, die keine Lichtbrechung wie der herkömmliche konvexe Linse zuließ. 13 zu
Ein weiterer Faktor für die MN-Geometrie war die UV-Lichtintensität. Die Intensität von 6,44 W / cm 2 wurde gewählt, weil die bei dieser Intensität erzeugt Nadeln besitzen ausreichende mechanische Festigkeit für Hautanwendungen. Eine weitere Erkenntnis der Intensität bezogen war, dass mit jeder Erhöhung der UV-Intensität, die Länge des MN erhöht. Dies könnte zu der flachen Oberseite der Mikrolinse, die ein Teil der Lichtstrahlen außerhalb des Brennpunkts reisen erlaubt zurückzuführen. 14,15 Weiterhin ist das Ausmaß der Polymerisation hat den Grenzwert in Abhängigkeit von der invers-quadratischen Gesetz des Lichtes, dh Energie verliert das Licht als die Entfernungaus den Quell zunimmt. 16
Die hier beschriebenen Protokolle haben den Vorteil, schimmelfrei Herstellung innerhalb einer kurzen Zeitspanne. Aber wir können nicht vorhersagen, wie weit kann es ferner für Bulk-Fertigung genommen werden. Die MNs Arrays wurden von niedrigen Kosten biokompatiblen Polymer hergestellt. Gegebenenfalls kann es als transdermale Arzneimittelabgabevorrichtung für pharmazeutische und kosmetische Anwendungen verwendet werden. Noch interessanter ist, kann es als eine Kombination aus dem Liefersystem und die Geräte 5,6,17 verwendet werden, die therapeutischen Verbindungen können (durch Mischen oder solubilisierende in Präpolymerlösung) während der Herstellung von MNs verkapselt werden. Die Löslichkeit der zugesetzten Verbindung innerhalb der Prepolymer-Lösung ist zu berücksichtigen, wie die MN Eigenschaften, beispielsweise genommen werden, MN Kraft, Änderungen vorbehalten. 17
Subscription Required. Please recommend JoVE to your librarian.
Materials
Name | Company | Catalog Number | Comments |
Poly(ethylene glycol) diacrylate (PEGDA Mn=258) | SIGMA | 475629-500ML | |
2-hydroxy-2-methyl-propiophenone (HMP) | SIGMA | 405655-50ML | |
Bovine collagen type 1, FITC conjugate | SIGMA | C4361 | |
UV curing station | EXFO Photonic Solutions Inc., Canada | OmniCure S2000-XL | |
Collimating Adaptor | EXFO Photonic Solutions Inc., Canada | EXFO 810-00042 | |
24-well plate | Thermo Fisher Scientific, USA | ||
Nikon SMZ 1500 stereomicroscope | Nikon, Japan | ||
Dillon GL-500 digital force gauge | Dillon, USA | ||
A-1R confocal microscope | Nikon, Japan |
References
- Zhou, C. P., Liu, Y. L., Wang, H. L., Zhang, P. X., Zhang, J. L. Transdermal delivery of insulin using microneedle rollers in vivo. International journal of pharmaceutics. 392, 127-133 (2010).
- Lee, J. W., Choi, S. O., Felner, E. I., Prausnitz, M. R. Dissolving microneedle patch for transdermal delivery of human growth hormone. Small. 7, 531-539 (2011).
- Raphael, A. P., et al. needle-free vaccinations in skin using multi layered, densely-packed dissolving microprojection arrays. Small. 6, 1785-1793 (2010).
- Lee, J. W., Han, M. R., Park, J. H. Polymer microneedles for transdermal drug delivery. Journal of drug targeting. 21, 211-223 (2012).
- Kochhar, J. S., Goh, W. J., Chan, S. Y., Kang, L. A simple method of microneedle array fabrication for transdermal drug delivery. Drug development and industrial pharmacy. 39, 299-309 (2013).
- Kochhar, J. S., Zou, S., Chan, S. Y., Kang, L. Protein encapsulation in polymeric microneedles by photolithography. International journal of nanomedicine. 7, 3143-3154 (2012).
- Tay, F. E. H., Iliescu, C., Jing, J., Miao, J. Defect-free wet etching through pyrex glass using Cr/Au mask. Microsystem Technologies. 12, 935-939 (2006).
- Iliescu, C., Chen, B., Miao, J. On the wet etching of Pyrex glass. Sensors and Actuators, A: Physical. 143, 154-161 (2008).
- Iliescu, C., Taylor, H., Avram, M., Miao, J., Franssila, S. A practical guide for the fabrication of microfluidic devices using glass and silicon. Biomicrofluidics. 6, 16505-16516 (2012).
- Iliescu, C., Jing, J., Tay, F. E. H., Miao, J., Sun, T. Characterization of masking layers for deep wet etching of glass in an improved HF/HCl solution. Surface and Coatings Technology. 198, 314-318 (2005).
- Pan, J., et al. Fabrication of a 3D hair follicle-like hydrogel by soft lithography. Journal of biomedical materials research. Part A. 101, 3159-3169 (2013).
- Jay, T. R., Stern, M. B. Preshaping photoresist for refractive microlens fabrication. P Soc Photo-Opt Ins. 1992, 275-282 (1993).
- Friedman, G. B., Sandhu, H. S. Longitudinal Spherical Aberration of a Thin Lens. Am J Phys. 35, 628 (1967).
- Xu, Q. A., Li, J., Zhang, W. Collimated the laser diode beam by the focus lens. Semiconductor Lasers and Applications IV. 7844, (2010).
- Lin, T. W., Chen, C. F., Yang, J. J., Liao, Y. S. A dual-directional light-control film with a high-sag and high-asymmetrical-shape microlens array fabricated by a UV imprinting process. J Micromech Microeng. 18, (2008).
- Dunne, S. M., Millar, B. J. Effect of distance from curing light tip to restoration surface on depth of cure of composite resin. Prim Dent Care. 15, 147-152 (2008).
- Kochhar, J. S., et al. Microneedle integrated transdermal patch for fast onset and sustained delivery of lidocaine. Molecular pharmaceutics. 10, 4272-4280 (2013).
- Kochhar, J. S., et al. Direct microneedle array fabrication off a photomask to deliver collagen through skin. Pharmaceutical research. 31, 1724-1734 (2014).