Abstract
Este manuscrito descreve a fabricação de microagulhas polimérico (Mn) matrizes por fotolitografia. Trata-se de um processo livre de mofo simples usando um photomask constituído por micro-lentes embutidas. Micro-lentes embutidas foram encontrados para influenciar MN geometria (nitidez). MN matrizes robustos com diâmetros que variam entre 41,5 ponta mm ± 8,4 mm e 71,6 mm ± 13,7 mm, com dois comprimentos diferentes (1336 mm ± 193 mm e 957 mm ± 171 mm) foram confeccionados. Estas matrizes de MN podem proporcionar aplicações potenciais na entrega de agentes terapêuticos de baixo molecular e macromolecular através da pele.
Introduction
Administração transdérmica de fármacos oferece uma abordagem alternativa atractiva para a administração da droga, especialmente para biomoléculas, que são administrados quase exclusivamente por injecções hipodérmicas. No entanto, a pele, especialmente a camada de topo (estrato córneo), é uma barreira formidável prevenção moléculas exógenas de entrar no corpo humano. Recentemente, dispositivos MN surgiram como possibilitando ferramentas para entregar drogas através da pele. Os dispositivos MN criar poros temporários no interior do estrato córneo, para permitir a passagem das moléculas de fármaco para conseguir a desejada actividade fisiológica melhorada com a adesão do paciente e conveniência 1-3.
Foram adotados vários métodos de fabricação para fabricar MNs poliméricos 4. No entanto, eles geralmente envolvem processos complicados e que exigem vários passos longos tempos e / ou temperaturas elevadas para fabricar matrizes milhões. 4 Para simplificar o processo de fabricação, um único processo livre de mofo etapa usandouma fotomáscara foi desenvolvido recentemente 5,6. No entanto, com este método, fabricado MNs teve blunt dicas de agulhas, como nenhum mecanismo estava no local para modificar o caminho ultravioleta (UV) luz envolvido em fotolitografia.
Neste estudo, as microlentes incorporado na fotomáscara têm sido propostos para definir a geometria dos milhões. O protocolo para fabricar máscaras que consistem em microlentes embutidos e, posteriormente, MN fabricação com pontas afiadas usando o photomask são relatados.
Subscription Required. Please recommend JoVE to your librarian.
Protocol
1. fotomáscara Fabrication
- Limpar uma bolacha de 4 "de vidro com solução piranha (H 2 SO 4 / H 2 O 2 na razão 2: 1) durante 20 min a 120 ° C por imersão num tanque de quartzo.
- Depositar uma camada de crómio / ouro (30 nm de Cr / 1 uM de Au) camada sobre a bolacha de vidro utilizando um feixe electrónico de evaporação 7 (Figura 1A).
- Coloque as bolachas em um evaporador e-beam. Uma vez que o vácuo atinge 5 x 10 -6 Torr, ligue a fonte de alta tensão (10 kV). Controlar a espessura pelo painel de controle monitor.
- Pré-limpos cada material durante 30 segundos utilizando a pistola de feixe electrónico, mantendo o obturador "OFF" (a fim de evitar a deposição sobre as bolachas).
- Gerar uma camada de máscara photoresist Cr / Au de profunda corrosão úmida do vidro.
- Aplicar um fotorresistente espessura de 2 um por fiação de 5 ml da solução durante 30 segundos a 3000 rpm utilizando um sistema de revestimento por pulverização de rotação.Prebake o fotorresistente numa placa de aquecimento a 100 ° C durante 1,5 min.
- Expor e asse difícil o photoresist a 120 ° C durante 30 minutos em um prato quente. É crítico para gerar uma superfície hidróf oba e uma forte aderência do foto-resistente para a camada de metal. Padrão da camada de Cr / Au Au usando Cr e condicionadores através do photoresist mascarar 8,9.
- Para a proteção da superfície do vidro modelado-un, unir temporariamente a pastilha de vidro de uma pastilha de silício manequim. 9
- Coloque a bolacha de vidro sobre uma chapa quente a 110 ° C e a cera derreter no lado oposto da pastilha de vidro (de tal forma que toda a superfície da bolacha é coberto com cera).
- Coloque uma pastilha de silício manequim em contato com a pastilha de vidro e pressione para remover o excesso de cera. A fim de evitar o derramamento de cera, coloque um lenço de papel sala limpa sobre a placa.
- Executar ataque químico isotrópico da lente usando ácido fluorídrico optimizada (49% v / v)e solução de ácido clorídrico (37% v / v) (numa proporção volumétrica de 10: 1). com um agitador magnético durante 10 min 8,5 Presença do HCl é crítico na obtenção de uma boa qualidade de superfície das lentes geradas.
- Assegure-se que a velocidade de gravação é de 7 um / min; utilizando um volume total de 200 ml de solução de gravação. Executar ataque químico num recipiente de plástico e tomar precauções de segurança para esta etapa de processamento.
- Limpar a bolacha na (DI) de água desionizada por enxaguamento e secagem adicional à temperatura ambiente.
- Após a conclusão do processo, separar a pastilha de vidro a partir da bolacha de silício do manequim e aquecer a cera usando uma chapa quente a 100 ° C durante 15 seg. Como a cera derrete a esta temperatura, separar a pastilha de vidro a partir da bolacha de silício do manequim.
- Remova a cera restante, o fotorresistente e as salientes Cr / Au camadas nos bordos das lentes que utilizam ultra-sons durante 1 hora, utilizando N-metil-2-pirrolidona como solvente a 80 ° C num tanque de ultra-sons.
- Criar uma réplica molde PDMS das microlentes fabricadas nas máscaras 11.
- Caracterizar as dimensões fotomáscara (comprimento e largura) e o molde microlentes PDMS (profundidade e diâmetro) réplicas usando um microscópio eletrônico de varredura e microscópio estereoscópico, respectivamente. 12-14
2. Eixos MN Fabrication
- Criar uma cavidade de 2,5 cm x 0,9 cm, utilizando as lâminas de vidro montados em ambos os lados de um vidro. O número das lâminas de vidro empilhadas em ambos os lados vai determinar a altura da cavidade conhecido como espaçador de espessura (Figura 1B).
- Fixe cada camada da placa de vidro através da aplicação de uma fina camada da solução de pré-polímero que contém o poli (etileno-glicol) diacrilato (PEGDA, PM = 258 Da) com 0,5% w / w de 2-hidroxi-2-metil-propiofenona (HMP) para a lâmina de vidro, seguido por irradiação da luz configurado com o ultravioleta de alta intensidade (UV) de 2 seg.
- Posicione o photomaSK (previamente fabricado) com as superfícies de Cr / Au revestida voltada para o interior da cavidade. Assegure-se que os lados das paredes da cavidade são não obscurecer as lentes embutidas na fotomáscara.
- Encher a cavidade com a solução de pré-polímero até que a superfície revestida a Cr / Au está em contacto com a solução sem quaisquer bolhas visíveis.
- Irradiar a configuração com elevada intensidade de luz UV de uma intensidade desejada por 1 segundo a uma distância de 3,5 cm da fonte de UV usando a estação de cura por UV com uma gama de filtro de UV de 320-500 nm. Utilize um adaptador collimating com a sonda de luz UV.
- Medir a intensidade de luz UV utilizado usando um radiómetro.
- Após exposição à radiação UV, remover a foto-mascara com a matriz de milhões. Verter a solução de pré-polímero em excesso que não é polimerizado no processo volta para o seu recipiente original para reutilização.
- Quantificar o diâmetro e o comprimento da ponta dos MNS usando um microscópio estereoscópico de acordo com as instruções do fabricante.
- Com uma pinça, colocar os MNS (previamente fabricado) fixos sobre a foto-mascara em um poço de uma placa de 24 poços como mostrado na Figura 1C.
- Adicionar um volume específico (300 - 400 ul) da solução de pré-polímero no poço, até as agulhas estão submersas a uma altura desejada. Este volume determina a espessura da camada de suporte resultante.
- Irradiar a configuração com luz UV de alta intensidade (15,1 W / cm 2), 10,5 cm de distância da fonte de UV com a duração de 1 segundo.
- Separa-se a camada de suporte sobre a matriz de manganês a partir da fotomáscara usando uma lâmina afiada.
- Quantificar o diâmetro comprimento, diâmetro da ponta e da base do MNS com a camada de suporte usando um microscópio estereoscópico de acordo com as instruções do fabricante.
Subscription Required. Please recommend JoVE to your librarian.
Representative Results
A geometria das MNS pode ser significativamente afectada pelas características de fotomáscara de microlentes e embutidos. O grau de refracção afecta o caminho de transmissão dos raios UV, que influenciaram a geometria MN (Figura 2A). Cada microlente foi encontrada para ter um diâmetro de 350 um, a 130 uM achatada superfície convexa, e uma profundidade de 62,3 uM (Figura 2B-D). Utilizando o teorema de Pitágoras, o raio de curvatura da primeira superfície mostrou-se 272,89 uM. A distância focal foi calculada como sendo de 509,28 pM (considerando n = 1,53627 vidro; n ar = 1,000; λ = 365 nm) através da equação fabricante de lentes 12, tal como indicado abaixo:
1 / f = (n 1 / n m -1) * (1 / r 1 -1 / r 2)
Onde n é 1 o índice de refracção do material da lente, n m é o índice de refracção do meio ambiente, o símbolo R1 representa o radius de curvatura da primeira superfície, e R2 é o raio de curvatura da segunda superfície.
O efeito de intensidade da radiação UV no comprimento MN, nitidez e deformação estrutural foi estudado variando a intensidade da luz UV a partir de 3.14 para 15.1 W / cm 2, a uma distância focal constante e à distância de fonte de luz. Verificou-se que o comprimento médio MN aumentou significativamente (p <0,05) com o aumento da intensidade 3,14-9,58 W / cm 2 (Figura 3A). Outros aumentos de intensidade superior a 15,1 W / cm 2 não produziu alteração significativa no comprimento. O diâmetro da ponta (medida da agudeza) e a estrutura de ponta de MN foram encontrados para variar com o aumento da intensidade (Figura 3B). Os de MNS com uma forma regular e sem qualquer deformação estrutural foram observados a 6,4 W / cm2.
A camada de suporte foi fabricado para permitir a remoção de manganês sob a forma de um emplastroe para tornar o reutilizável photomask. Ele também forneceu força para os eixos do manganês. Portanto, o efeito do volume de camada de suporte (o volume das soluções de pré-polímero para formar a camada posterior) foi também estudada. Com diâmetros de ponta não afectadas, foram observados os de MNS com uma gama de comprimento (1.336 ± 193 mm para 300 ul e 957 ± 171 mm para 400 ul), após a exposição à radiação UV (Figura 4).
Figura 1. (A) Representação esquemática do processo de fabrico de lentes embutidas fotomáscara. (1) 4 "bolacha de vidro. (2) Cr / Au camada depositada utilizando um evaporador e-beam. (3) Exposição de Cr camada de máscara / Au / photoresist à luz UV com photomask. (4) Formação de teste padrão na camada usando Cr / Au etchant. (5) ligação temporária de vidro em uma pastilha de silício manequim. (6) - (7) Gravura Wet (isotrópico) processo usando HF condicionadores / HCl seguido de ultra-som. (8) descolagem de wafer de silício manequim e remoção de camada foto-resistente. (B) Representação esquemática do processo de fabrico de agulhas. Crómio fotomáscara revestido (9 x 9 matrizes), é colocado sobre uma cavidade que contém a solução de pré-polímero e exposto a UV. (C) Representação esquemática do processo de fabricação da camada de suporte. Photomask, com microagulhas em anexo, é colocado em um poço cheio com pré-polímero e exposto a UV. Por favor clique aqui para ver uma versão maior desta figura.
Figura 2. Caracterização de fotomáscara. (A) Exposição UV foca a luz num conica l caminho, produzindo MNS cónicos. (B) e uma imagem SEM de uma microlente (C). (D) uma porção de uma matriz de PDMS réplicas molde copiados dos microlentes, mostrando a superfície convexa achatada, sob um estereomicroscópio. (E) A photomask mostrando o padrão. Por favor clique aqui para ver uma versão maior desta figura.
Figura 3. Efeito de parâmetros de UV na geometria microagulhas. Efeito de (A) e intensidade (B) espaçador espessura da duração microagulhas. Por favor clique aqui para ver uma versão maior desta figura.
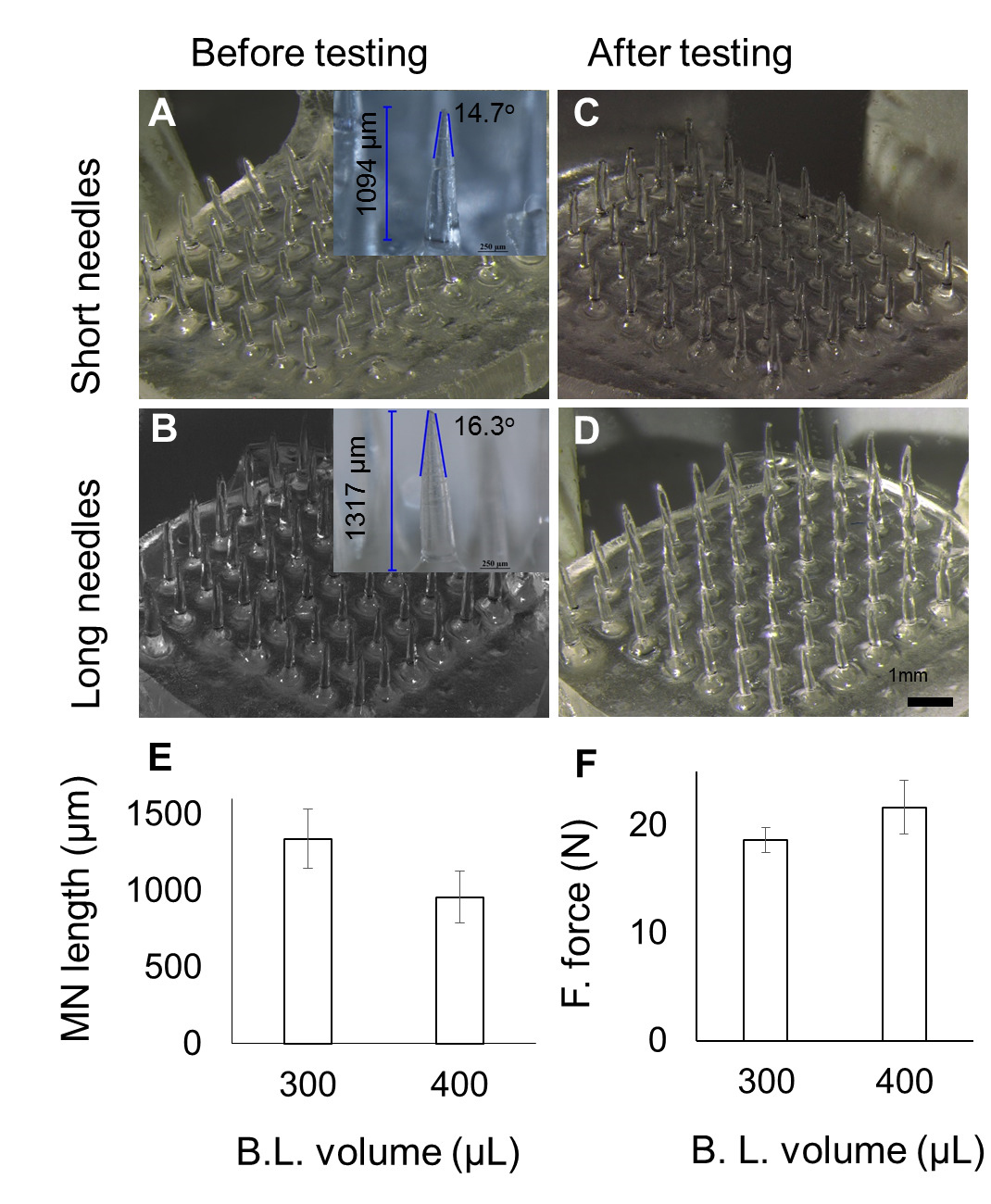
Figura 4. Efeito da variação de volume pré-polímero utilizado para a camada de suporte de fabricação. (A - B) imagens em vários tamanhos, com duração média de MN (1.336 um) MNs curtas (957 mm) e longas. (C - D) As imagens correspondentes a (AB) após o teste de força fratura. (E) Redução de comprimento MN com aumento do volume usado para camada de suporte de fabricação. Força fratura (F) MN entre os dois volumes pré-polímero utilizado para fabricar camada de suporte (BL). Por favor clique aqui para ver uma versão maior desta figura.
Subscription Required. Please recommend JoVE to your librarian.
Discussion
O protocolo acima descrito para o fabrico da matriz de MNS foi apresentada para fabricar a matriz MNS de ~ 1 cm 2. As matrizes podem ser aumentados através da criação de uma cavidade grande tamanho e usando uma fotomáscara maior. O aumento de tamanho da cavidade pode ser criado através do aumento da largura entre os espaçadores de cada lado. Embora cada passo para fabricar as matrizes MN no protocolo foi importante, os passos mais importantes foram: o posicionamento photomask, o preenchimento de solução de pré-polímero, e irradiação da configuração. Posicionamento da fotomáscara deve ser de tal maneira que as superfícies de Cr / Au revestidos enfrentar o interior da cavidade e os lados das paredes da cavidade obscurecer as lentes embutidas na fotomáscara. Ao preencher o molde com a solução de pré-polímero, garantir que o ar bolhas não são aprisionados, que pode de outra forma levar a uma matriz força MN deformado e baixo. As bolhas de ar podem ser evitados através de uma ação wicking controlada adicionando lentamente o prepolymer solução e assegurar que não existem bolhas de ar presentes na solução de pré-polímero. Posicionamento da instalação para a irradiação deve ser feito de uma forma orientada para garantir a exposição UV uniforme. Antes da exposição à luz UV, a configuração foi alinhado e colocado dentro da demarcação no suporte da base.
Os MNS formadas usando fotolitografia foram grandemente influenciadas pela presença dos micro-lentes como a lente resultou na polimerização num percurso convergente, o que levou à formação dos MNS nítidas em relação aos MNS cilíndrica formada usando a foto-mascara planar. No fotomáscara planar, a luz UV passa por ele com pouco desvio (quase recta), resultando na formação dos MNS cilíndricos com pontas afiadas menos. Enquanto na fotomáscara microlente-embedded, a luz UV que passa através das lentes foram submetidos a refracção e convergentes, resultando na formação de MNS com pontas afiadas. A equação do fabricante de lente que tem sido utilizado como um predictive modelo para aproximar o comprimento do MN, correlacionando com a distância focal das microlentes deu uma previsão do comprimento três vezes menos do que o real. A discrepância pode ser devido à superfície convexa achatada das microlentes, o que não permitiu refração da luz como a lente convexa convencional 13.
Outro factor para a geometria MN foi a intensidade da luz UV. A intensidade de 6,44 W / cm2 foi escolhido porque as agulhas produzidas nesta intensidade possuía uma resistência mecânica suficiente para aplicações de pele. Outra constatação foi relacionada com a intensidade com que cada incremento na intensidade da radiação UV, o comprimento de manganês aumenta. Isto poderia ser atribuído ao topo plana de microlente, o que permitiu que alguns dos raios de luz a viajar para além do ponto focal. 14,15 Além disso, a extensão da polimerização tem o seu limite, dependendo da lei do inverso do quadrado da luz, ou seja, a luz perde energia como a distânciaA partir da fonte aumenta. 16
Os protocolos aqui descritos têm a vantagem de fabricação livre de molde dentro de um curto período de tempo. Mas não podemos prever o quão longe ela pode ser levada adiante para a fabricação em massa. Os MNs matrizes foram feitas a partir de um baixo custo polímero biocompatível. Ele pode potencialmente ser usado como dispositivo de distribuição transdérmica de fármacos para aplicações farmacêuticas e cosméticas. Mais interessante, que podem ser utilizados como uma combinação de sistema de entrega e o dispositivo, tal como os compostos terapêuticos pode ser encapsulada (ou por mistura em solução de pré-polímero de solubilização) durante o fabrico de mns. 5,6,17 A solubilidade do composto acrescentado interior deve ser tomada em consideração a solução de pré-polímero como as características de MN, por exemplo, força MN, pode mudar. 17
Subscription Required. Please recommend JoVE to your librarian.
Materials
Name | Company | Catalog Number | Comments |
Poly(ethylene glycol) diacrylate (PEGDA Mn=258) | SIGMA | 475629-500ML | |
2-hydroxy-2-methyl-propiophenone (HMP) | SIGMA | 405655-50ML | |
Bovine collagen type 1, FITC conjugate | SIGMA | C4361 | |
UV curing station | EXFO Photonic Solutions Inc., Canada | OmniCure S2000-XL | |
Collimating Adaptor | EXFO Photonic Solutions Inc., Canada | EXFO 810-00042 | |
24-well plate | Thermo Fisher Scientific, USA | ||
Nikon SMZ 1500 stereomicroscope | Nikon, Japan | ||
Dillon GL-500 digital force gauge | Dillon, USA | ||
A-1R confocal microscope | Nikon, Japan |
References
- Zhou, C. P., Liu, Y. L., Wang, H. L., Zhang, P. X., Zhang, J. L. Transdermal delivery of insulin using microneedle rollers in vivo. International journal of pharmaceutics. 392, 127-133 (2010).
- Lee, J. W., Choi, S. O., Felner, E. I., Prausnitz, M. R. Dissolving microneedle patch for transdermal delivery of human growth hormone. Small. 7, 531-539 (2011).
- Raphael, A. P., et al. needle-free vaccinations in skin using multi layered, densely-packed dissolving microprojection arrays. Small. 6, 1785-1793 (2010).
- Lee, J. W., Han, M. R., Park, J. H. Polymer microneedles for transdermal drug delivery. Journal of drug targeting. 21, 211-223 (2012).
- Kochhar, J. S., Goh, W. J., Chan, S. Y., Kang, L. A simple method of microneedle array fabrication for transdermal drug delivery. Drug development and industrial pharmacy. 39, 299-309 (2013).
- Kochhar, J. S., Zou, S., Chan, S. Y., Kang, L. Protein encapsulation in polymeric microneedles by photolithography. International journal of nanomedicine. 7, 3143-3154 (2012).
- Tay, F. E. H., Iliescu, C., Jing, J., Miao, J. Defect-free wet etching through pyrex glass using Cr/Au mask. Microsystem Technologies. 12, 935-939 (2006).
- Iliescu, C., Chen, B., Miao, J. On the wet etching of Pyrex glass. Sensors and Actuators, A: Physical. 143, 154-161 (2008).
- Iliescu, C., Taylor, H., Avram, M., Miao, J., Franssila, S. A practical guide for the fabrication of microfluidic devices using glass and silicon. Biomicrofluidics. 6, 16505-16516 (2012).
- Iliescu, C., Jing, J., Tay, F. E. H., Miao, J., Sun, T. Characterization of masking layers for deep wet etching of glass in an improved HF/HCl solution. Surface and Coatings Technology. 198, 314-318 (2005).
- Pan, J., et al. Fabrication of a 3D hair follicle-like hydrogel by soft lithography. Journal of biomedical materials research. Part A. 101, 3159-3169 (2013).
- Jay, T. R., Stern, M. B. Preshaping photoresist for refractive microlens fabrication. P Soc Photo-Opt Ins. 1992, 275-282 (1993).
- Friedman, G. B., Sandhu, H. S. Longitudinal Spherical Aberration of a Thin Lens. Am J Phys. 35, 628 (1967).
- Xu, Q. A., Li, J., Zhang, W. Collimated the laser diode beam by the focus lens. Semiconductor Lasers and Applications IV. 7844, (2010).
- Lin, T. W., Chen, C. F., Yang, J. J., Liao, Y. S. A dual-directional light-control film with a high-sag and high-asymmetrical-shape microlens array fabricated by a UV imprinting process. J Micromech Microeng. 18, (2008).
- Dunne, S. M., Millar, B. J. Effect of distance from curing light tip to restoration surface on depth of cure of composite resin. Prim Dent Care. 15, 147-152 (2008).
- Kochhar, J. S., et al. Microneedle integrated transdermal patch for fast onset and sustained delivery of lidocaine. Molecular pharmaceutics. 10, 4272-4280 (2013).
- Kochhar, J. S., et al. Direct microneedle array fabrication off a photomask to deliver collagen through skin. Pharmaceutical research. 31, 1724-1734 (2014).