Summary
Eksperimentelle metoder til hurtig pyrolyse af lignocellulose biomasse til at producere bio-olier og til den katalytiske hydrogenbehandling af bio-olier til at producere brændstof range kulbrinter præsenteres. Hot-damp filtrering under hurtig pyrolyse for at fjerne fine char partikler og uorganiske forureninger fra bioolie blev også bedømt.
Introduction
Vores samfund er meget afhængig af fossile brændstoffer (f.eks olie, naturgas, kul, etc.). Disse ressourcer er ikke bæredygtige energikilder og bliver udnyttet i et hastigt stigende tempo, hvilket fører til bekymringer vedrørende svindende fossile brændstoffer ressourcer, miljømæssige konsekvenser af CO 2 -udledning og økonomiske problemer. 1,2,3,4 Der er stigende efterspørgsel efter alternative og bæredygtige energikilder. Biomasse er den eneste vedvarende og carbon-neutral ressource for produktion af flydende brændstoffer (biobrændstoffer) og carbon-baserede kemikalier til at erstatte fossile brændstoffer i den nuværende produktion og konvertering energisystem. 3,4
Lignocellulose biomasse (f.eks, skove, græs, energiafgrøder, landbrugsaffald, etc.), som i øjeblikket er den mest udbredte og billigste biomasse kilde, har tiltrukket sig mest opmærksomhed som en måde at producere biobrændstoffer via forskellige termokemiske og biologiske ruter.
Den første rute kan kun udnytte cellulose og hemicellulose del af lignocellulose biomasse. Pyrolyse integreret med opgradering anses for at være en nær sigt levedygtig teknologi til direkte produktion af biobrændstoffer.
Pyrolyse er den termiske nedbrydning af lignocellulose biomasse ved temperaturer mellem 400 og 550 ° C i fravær af oxygen. 4,5,6 En række reaktioner, såsom depolymerisering, dehydrering, og C-C-binding spaltning forekommer under pyrolyse og føre til dannelsen af en kompleks blanding of mere end 200 oxygenerede forbindelser. 4,5,6 Bio-olier i høje udbytter (op til 75 vægt-% af tørfoder) kunne produceres med op til 70% af energien lagret i de biomasseråmaterialer tilbageholdt. 4,5 Men direkte anvendelse af den producerede pyrolyse bio-olie som transportbrændstof i standardudstyr er problematisk på grund af den høje ilt og vandindhold, der fører til forskellige fysiske og kemiske egenskaber, såsom høj viskositet, ætsende, dårlig volatilitet, lav brændværdi, og dårlig stabilitet. 6,7,8,9 derfor omfattende fjernelse ilt, som kræves for at opgradere bio-olier til brændstof-range kulbrinter. Katalytisk hydrobehandling anvendelse af faste katalysatorer i hydrogen er den mest almindelige vej til opgradering bioolie ved fjernelse ilt gennem hydrodeoxygenation og hydrogeneringsreaktioner. 6,7,8,9
I øjeblikket er en af de primære udfordringer for pyrolyse efterfulgt af hydrobehandling er at opnå langsigtet stabil drift, især forhydrogenbehandlingsproces hvor den termiske ustabilitet af bioolie og uorganiske og svovl rester i bioolie forårsage betydelig katalysatordeaktivering. 10,11 Den termiske ustabilitet af bioolie er blevet behandlet af lav temperatur hydrogenering for at stabilisere de aktive arter i bioolie. 11,12 Cleanup af bioolie ved at fjerne uorganiske rester, som kunne katalysere repolymerization af bioolie fraktioner og deaktiver hydrobehandlingskatalysatorer ved udfældning, kan være værdifuld. Hot-damp filtrering er en af de teknikker til effektivt reducerer det uorganiske indhold i bioolie ved at fjerne char partikler under pyrolyse. 13,14,15 Hot-damp filtrering anvendes nedstrøms for pyrolysereaktoren at adskille char bøder fra pyrolysen gas / dampstrømmen ved høj temperatur før kondensering af dampene. 13,14,15
Vi rapporterer her den protokol, der bruges på National Renewable Energy Laboratory (NREL) for biomasse hurtigt pyrolysis både med og uden hot-damp filtrering til frembringelse af bioolier bruger hvirvellagsreaktor og på Pacific Northwest National Laboratory (PNNL) for bioolie hydrobehandling at producere biobrændstoffer i en kontinuerlig flow packed bed katalytisk reaktor. Arrangementet af reaktorsystemer, de operationelle procedurer, og forarbejdning og analyser af råmaterialer, bio-olier, og biobrændstoffer er beskrevet i detaljer. Resultater af pyrolyse behandling af en repræsentativ biomasse råmateriale med eller uden hot-damp-filtrering og hydrogenbehandling af den producerede bio-olie er også præsenteret sammen med en vurdering af virkningen af hot-damp filtrering.
Protocol
1. Fast Pyrolyse med Hot Vapor Filtration
- Forberedelse Biomasse råvare
- Mill biomassen til en partikelstørrelse på <2 mm. Opbevares på et køligt, tørt sted.
- Saml pyrolyse-system
- Saml pyrolysereaktoren.
- Mount reaktor inde ovnen. Tilslut fluidiseret kvælstof, snegl nitrogen og luftledninger til reaktoren. Sæt sneglen ind med kappe snegl port. Tilslut køleluft til jakken.
- Mount og connect snegl motor.
- Mount solid feeder 30 til 60 cm direkte over den vertikale åbning af sneglen port.
- Mount lock hopper mellem det faste feeder udløb og den vertikale åbning af sneglen port. Forbindelse til sneglen port med nylon-fletning, forstærket vinyl slange med en indvendig diameter på 25 mm. Fastgør slangen til sneglen port med en slangeklemme. Tilslut til feeder med en letvægts-, klar, løs plast slip-fit.
- Saml cyklon og varmt filter.
- Monter cyklon og tilslut cyklon indløb til reaktoren. Close-par modtager til cyklonen.
- Mount hot filter (fremstillet af rustfrit stål med en porestørrelse på 2 um) i filterhuset. Slut cyklon udløb til hot-filter indløb. Tilslut kvælstof udrensning og trykaflastning til cyklon stikkontakt.
- Brug varme tape og isolerende tæpper at varme spor fra cyklonen indløb til kondensatoren indløb.
- Saml kondensatorsystem.
BEMÆRK: Monter stykker af kondensatoren systemet i et stinkskab ved hjælp laboratorie-stik, ring-stande, og laboratorie klemmer.- For første kondensator, til at koble 15 til 30 cm af rustfrit stålrør 1,2 cm (ydre diameter) borsilikat rør, med en standard konisk joint. Forbind den første kondensator til en 500 ml, tohalset (standard konus), rundbundet kolbe (modtager) anbringes i en beholder that vil tjene som et isbad. Foretag forbindelser mellem fartøjer neden for dette punkt med 9 til 12-mm klart vinyl slange sikret med spændebånd på slebne samlinger, sfæriske led og slange modhager på glas.
- Tilslut udløbet af den første kondensator kolben til den nedre side port (indgang) af den elektrostatiske udskiller (ESP).
- Tilslut oversiden port (udløb) af ESP til den lille øvre tilslutning af tøris-fælde (kolde finger kondensator).
- Tilslut en U-rør til linje mellem ESP og tøris fælde. Fyldes U-røret halvt fyldt med vand.
- Tilslut tøris-fælde til en 500 ml, tohalset, rundbundet kolbe (modtager) anbringes i en beholder, der vil tjene som en tør-isbad.
- Forbind udgangen fra 500 ml kolbe til indløbet (midterste port) af huset af kulfilteret.
- Placer en beholder til tøris omkring bunden af filterhuset.
- Tilslut filter outlet til den tørre-test måler og andre gas analyse instrumenter (f.eks, ikke-dispersive infrarøde analysatorer for CO, CO 2, og CH 4, varmeledningsevne detektor til brint, og mikro-gaskromatografi (mikro-GC) for CO , CO 2, nitrogen-, hydrogen og C1-C4 hydrocarboner) og derefter at udlufte.
BEMÆRK: Skematisk af pyrolysereaktoren er vist i figur 1. Billeder af biomassen feeder, pyrolyseovnen, cyklon, hot-dampfilter, og kondensatorer i pyrolysereaktoren systemet er vist i fig S1 til S5 i den supplerende fil.
- Saml pyrolysereaktoren.
- Load pyrolysereaktoren
- Hæld 200 ml sand (330 g) i reaktoren.
- Hæld 2 kg jord biomasse til påfyldningstragten.
- Lækage kontrollere pyrolyse-system
- Cap off system ved kondensatorens indløb.
- Presse til 0,05 MPa eller forventede maksimale driftstryk, alt efter hvader højere. Sikre, at der kræves for at opretholde trykket er <200 ml / min. Hvis ikke, finde og reparere læk, og gentage dette trin.
- Reducer trykket, Tag hætten systemet, tilslut kondens-system, cap ved afkørsel slutningen af kondens-system.
- Presse til 0,01 MPa. Sikre, at en strøm af <200 ml / min opretholder trykket. Hvis ikke, finde og reparere lækagen, og gentage dette trin.
- Trykket og tilslut kondens-systemet til instrumenter.
- Varm op reaktor
- Slå køleluft, indstille fluidiserende nitrogen flow til 3 standard L / min og sneglen nitrogenstrøm til 1 standard L / min.
- Sæt ovnen måltemperatur til 500 ° C og andre varmeapparater til 400 til 500 ° C.
- Rampe temperatur op til at målrette temperaturer ved en hastighed på 1 til 10 ° C / min.
- Forbered dig på at betjene
- Forøg fluidiserende kvælstof flow til 14 standard L / min, snegl kvælstof flow sats til 1,4 standard L / min, og indføre rensegas ved en strømningshastighed på 0,5 standard L / min. De fleste af udrensningen går ind i brud-disk port på cyklonudløbet.
- Fyld bad under første kondensator med is. Fyld tøris fælde, beholder under sin receiver, og beholder omkring koalisensfilter med tøris.
- Overvåge temperatur inderside koalisensfilter med termoelement placeret på overfladen af filteret og justere tøris niveau, så det er 0 ° C.
- Udfør pyrolyse eksperiment
- Tænd lock-hopper ventiler (brug 4 sekunder cyklus) og snegl.
- Tænd ESP. Sæt spænding til 5 til 10 kV, som er nødvendig for at observere en bue mindst en gang hver 2 sek.
- Brug mikro-GC for at verificere, at ingen ilt er til stede. Kontroller, at tænde for sneglen og lås hopper ikke forårsagede et fald i produktionen gasstrømmen, hvilket ville indikere tilstedeværelsen af en lækage.
- Slå feeder ved 100 g / time. Overhold sengen temperatur ogøge setpunktet efter behov for at kompensere for den øgede varmebelastning.
- Når temperaturen er kommet til inden for 2 ° C på 500 ° C, øge tilspændingen med 100 g / time. Gentag dette indtil en fødehastighed på 420 g / time er nået.
- Hver 15 min, rekord seng temperatur, tilspænding på feeder controller, gaskoncentrationer ved mikro-GC, tør test måler hastighed, og systemtryk ved manometre. Kontroller, at ESP stadig gnistdannelse korrekt. Reagere på ændringer i nogen af disse efter behov. Refill is og tøris. Tøm ESP til et produkt samling krukke efter behov.
- Lukke ned
- Efter fodring 1 kg biomasse, stop fodring.
- Efter gas niveauer er henfaldet til mindre end 10% af steady-state-værdier, skal du slukke alle varmeapparater, skru ned fluidiserende strøm til 3 standard L / min og sneglen flow til en standard L / min. Sluk ESP, slusebeholderen ventiler, og snegl.
- Lad systemet køle (4 til 6 timer), før du åbner de varme sektioner. </ Ol>
- Saml flydende produkter og char.
- Afvej alle dele af kondensatoren for at opnå total flydende udbytte. Hæld væsker fra kondensatoren modtagere til en fælles krukke eller flaske. Alternativt kan du bruge acetone til at rengøre glas.
- Tomme char modtageren i en krukke. Fjern hot filter, tømme huset, og børst filteret ind i char krukke. Afvej filteret. Fjern og vejer sengen materiale. Brug en HEPA vakuum med en knock-out fartøj for denne tjeneste.
- Oxidere systemet.
- Forsegle reaktor, cyklonbeholderen, og renses varmt filter. Kontroller for utætheder som beskrevet ovenfor i afsnit 1.4.
- Installere en metal linje fra kondensatoren indløbet til udløbet af kulfilteret at omgå kondensation system.
- Opvarm reaktoren til 550 ° C med 3 standard L / min nitrogen som den fluidiserende gas og 1 standard L / min snegl nitrogenstrøm.
- Tilføj luft til fluidiserendegas. Start ved 0,2 standard L / min og gradvist øge til 4 l / min. Fortsæt indtil CO + CO 2 koncentrationer er mindre end 0,1%.
- Beregn udbyttet.
- Beregn flydende udbytte som den samlede ændring i massen af kondens-systemet.
- Beregn char udbytte som summen af vægten ændring i sengen, vægtændring af den varme filter, og char indsamlet fra cyklonen modtager og hot-filterhuset.
BEMÆRK: Yderligere char kunne estimeres fra oxidationen af systemet, men dette er normalt uden betydning. - Beregn gasudbytte som den samlede vægt af gasformige produkter fra gaskoncentrationerne målt på GC og strømningshastigheden af det tørre testmåleinstrument.
2. Katalytisk hydrogenbehandling af Bio-olie
Bemærk: De bio-olieprøver produceret på NREL blev sendt til PNNL for katalytisk hydrogenbehandling på et hydrogenbehandler system.
- hydrogenbehandler systemet
- Sørg for, at hydrogenbehandler systemet er i drift tilstand ved at kontrollere hver komponent.
BEMÆRK: hydrogenbehandler reaktorsystem anvendte er udformet som en enkelt-pass, medstrøm, kontinuerlig, down-flow katalytisk reaktor. Systemet består af tre hovedkomponenter: 1) en gas og vådfodring komponent, 2) en opvarmet reaktor, og 3) en gas-væske produktadskillelse komponent (figur 2). Systemet er konstrueret til at fungere ved op til 13,6 MPa (2.000 psig; maksimale driftstryk) med en maksimal katalysatortemperatur 500 ° C (kun reaktoren er vurderet ved denne temperatur). - Sørg for, at hydrogenbehandler overvågning og kontrol system, og systemet sikkerhedsstyring er i driftstilstand.
BEMÆRK: Systemet overvåges og delvist kontrolleret af en in-house bygget computerprogram med forskellige sensorer. Sensorer omfatter termoelementer og tryktransducere til reaktoren samt brint og ventilation sensors i kabinettet, hvor reaktoren er placeret. Data registreres af program til overvågning reaktoren. Gasudløbet strømningshastigheden måles af et flowmeter, og data registreres af det ledsagende software. Programmet styrer også strømforsyningen af større udstyr af reaktoren. Under et eksperiment, hvis reaktoren undergår en uønsket ændring i driftsbetingelserne angår specifikke trykændringer og / eller temperaturændringer, eller en brændbar gas er til stede over grænsen sikkerhed, og / eller hvis ventilationen svigter, kunne programmet automatisk lukke systemet ned for at sikre sikkerheden. Trykaflastning ventiler og en sprængskive også installeres i hydrogenbehandler system til at beskytte mod overtryk.
- Sørg for, at hydrogenbehandler systemet er i drift tilstand ved at kontrollere hver komponent.
- Katalysator lastning og forbehandling
- katalysatorfremstilling
- Knuse begge katalysatorer, Ru / C, som den fase-I-katalysator og CoMo / Al 2 O 3 som den fase-II-katalysator, ogsigte for at bevare 0,25 til 0.60 mm (30 til 60 mesh) kerner.
BEMÆRK: Ru / C katalysator blev fremstillet in-house og Como / Al 2 O 3 Katalysatoren var et kommercielt produkt.
- Knuse begge katalysatorer, Ru / C, som den fase-I-katalysator og CoMo / Al 2 O 3 som den fase-II-katalysator, ogsigte for at bevare 0,25 til 0.60 mm (30 til 60 mesh) kerner.
- Katalysatorbelastning i reaktoren
- Brug stålrør og skærme rustfri som support medier til katalysatoren senge. Hæld langsomt fase-II-katalysator korn, Stage-I-katalysator korn, og de oprindelige fase-I katalysatorpartikler ekstrudater, som blev brugt som distributør, ind i reaktoren sekventielt mens "trykke" på ydersiden af reaktoren til dannelse pakkede katalysatorlag . Load 32 ml af hver katalysator til dannelse af en to-trins katalysatorleje med 24 ml af hver katalysator placeret i den isoterme zone (figur 3).
- Installer reaktoren til hydrogenbehandler systemet
- Placer reaktoren ind i hydrogenbehandler system ved at installere de to varmelegemer og derefter forbinder reaktoren til gassen og væskenfoder komponent og gas-væske-separation komponent.
BEMÆRK: To heat tape-heated aluminium kapper omslutte den rørformede reaktor for at tilvejebringe varme. Hver opvarmet kappe anvendes uafhængigt for at opvarme den del af reaktoren under katalysator forbehandling og under hydrogenbehandling testning. Hver kappe aluminium omviklet med en høj temperatur varme bånd og isolering og opvarmes med en temperaturregulator. Den rørformede fast leje katalytisk reaktor er fremstillet af 316 rustfrit stål og med en indre diameter på 13 mm og en længde på 64 cm. Et termoelement (4,7 mm udvendig diameter) er placeret i midten af reaktoren, og to termoelementer er placeret i brønden for at måle temperaturen af katalysatorlejerne.
- Placer reaktoren ind i hydrogenbehandler system ved at installere de to varmelegemer og derefter forbinder reaktoren til gassen og væskenfoder komponent og gas-væske-separation komponent.
- Kontroller trykket af hydrogenbehandler for utætheder ved hjælp 12,0 MPa nitrogengas ved at holde systemet på tryk og sikre, at trykfaldet er lavere end 1 psig per time.
- Katalysator forbehandling. sulfidkatalysatorerne in situ i brint og sulfidering agent flow.
- Varm begge katalysatorlejerne fra stuetemperatur til 150 ° C med en hastighed på 120 ° C / time i hydrogen ved 242 ml / min.
- Oprethold begge katalysator-bed temperaturer ved 150 ° C i 2 timer i hydrogen ved 242 ml / time og sulfidering middel ved 0,128 ml / min (35 vægt% di-tert-butyldisulfide i decan fødes af en fødepumpe).
- Varm fase-I seng fra 150 til 250 ° C med en hastighed på 83,3 ° C / time, og holdes ved 250 ° C i 5,8 timer. I samme periode, opvarme den fase-II seng fra 150 til 400 ° C med en hastighed på 83,3 ° C / time, og holdes ved 400 ° C i 4 timer. Under proceduren, holde trykket af reaktoren ved 10,3 MPa, den sulfidering agent strømningshastighed på 0,128 ml / min, og den hydrogen strømningshastighed på 242 ml / min.
- Stop sulfidering agent flow og vedligeholde hydrogenstrøm. Derefter indstille temperaturen af hver katalysator bed til den ønskede reaktionstemperatur.
BEMÆRK: sulfidering middel strømningshastighed bestemmes af mængden af anvendt katalysator og sulfidering agent flydende rumhastighed (LHSV) på 0,12 ml / ml-kat / time i overordnede katalysatorer. Hydrogenstrømningshastigheden bestemmes af sulfidering middel strømningshastighed og midlet strømningsforhold hydrogen-til-sulfidering ved 1.890 ml hydrogen / ml sulfidering middel væske. Komponenterne gas og flydende fodring af hydrogenbehandler systemet består af to højtryks-sprøjtepumper. En af de to pumper anvendes til at fodre sulfidering middel. Gassen og sulfidering middel indføres i den præ-reaktoren zone af reaktoren, hvor væsken blandes, før de passerer nedad gennem katalysatorlejet i reaktoren.
- katalysatorfremstilling
- Bioolie hydrobehandling
- Juster hydrogenstrøm til 152 ml / min og vedligeholde systemet tryk ved 10,3 MPa. Indstil temperaturerne af den fase-I katalysatorlejet og scenen-II katalysatorlejet til 220 og 400 ° C, hhv.
BEMÆRK: The hydrogen strømningshastighed er bestemt af mængden af anvendt katalysator, bioolie-LHSV på 0,20 ml / ml-cat / time for hvert trin, og forholdet hydrogen-til-bioolie af 1.900 ml hydrogen / ml bioolie . - Optag lejetemperaturen og hydrogenstrøm basislinjer, når temperaturen, trykket, og hydrogenstrøm bliver stabil.
- Tilføj di-tert-butyl disulfid til bio-olie foder på et beløb svarende til 150 ppm svovl i bio-olie. Fyld bioolie foder i en af fødepumper og rense tilførselsledningen indtil en flydende strøm, som er fri for luftbobler opnås.
- Pres på den pumpe til 10,3 MPa, og derefter oprette forbindelse til reaktoren ved at åbne de forbindende ventiler. Begynde at fodre bioolien ved en strømningshastighed på 4,8 ml / time. Denne handling starter bioolie-hydrobehandling test.
BEMÆRK: Bioolie flowhastighed bestemmes af mængden af anvendt katalysator og bioolie-LHSV på 0,20 ml / ml-cat / time for hver fase. Hydrogengassen og bioolie introduceres til præ-reaktoren zone af reaktoren, hvorgassen og væsken blandes, før de passerer nedad i en antaget sive flow gennem katalysatorlejet i reaktoren. - Kontroller status af reaktoren og registrere de parametre, såsom temperatur, tryk, strømningshastighed og volumen, periodisk. Sørg for katalysator-bed temperaturen ligger inden for ± 2 ° C af den ønskede temperatur, den gas og flydende strømningshastigheder er nøjagtigt de samme som de ønskede indstillinger, og reaktortrykket er inden for ± 0,15 MPa af det ønskede tryk. Sikre trykfaldet over katalysatorlejet er <0,35 MPa.
BEMÆRK: Systemet overvåges og delvist kontrolleret af en in-house bygget computerprogram med forskellige sensorer. Sensorer omfatter termoelementer og tryktransducere til reaktoren samt brint og ventilation sensorer i kabinettet, hvor reaktoren er placeret. - Analyser outlet gasprøver hver 2 timer ved at dirigere off-gas gennem en on-line micro-GC.
BEMÆRK: mikro-GC er en en fire-kanaliel mikro-GC og kalibreres med en kalibreringsgas før hver hydrobehandling test. - Indsamle væskeprøver hver 6 timer under anvendelse af følgende procedure: skifte prøveudtagning fælde til bypass fælde, reducere presset af prøveudtagningen fælde, dræne den flydende prøve til indsamling hætteglas, rense prøveudtagning fælden med nitrogen under tryk prøveudtagning fælde med nitrogen, og omdirigere vareflow til prøveudtagning fælde. Betjen en række to- og tre-vejs ventiler, der aflede gasser og produkter i de ønskede retninger.
BEMÆRK: Når reaktanterne passerer gennem katalysatorlejerne, er de flydende produkter og uomsatte væsker adskilt fra de gasformige produkter og uomsatte gasser i gas-væske separation system. De varme gasser passerer gennem en af to under tryk, kølet, flydende / gas kuldefælder (prøve fat i eller bypass fælde) anbragt parallelt nedstrøms reaktorsystemet. Afgangsgassen passerer derefter gennem modtryksregulator hvor trykket reduceres til atmospHeric pres. Afgangsgassen føres derefter gennem en gasmåler til måling af strømningshastighed. - Gennemføre testen for 60 timer på strøm (tid på strøm [TOS]). Afslutning af testen ved at stoppe bioolie feed. Indstil reaktortemperaturen til 100 ° C og hydrogen strømningshastighed til 100 ml / min.
BEMÆRK: Testen kan arrangeres med Toss spænder fra halvtreds til flere hundrede timer.
- Juster hydrogenstrøm til 152 ml / min og vedligeholde systemet tryk ved 10,3 MPa. Indstil temperaturerne af den fase-I katalysatorlejet og scenen-II katalysatorlejet til 220 og 400 ° C, hhv.
- Procedure Post-test
- Brug acetone til rengøring fødepumpen til tilførsel bioolie. Læg den rensede fodring pumpe med acetone.
- Udrense katalysatorlejet med ~400 ml acetone ved en acetone strømningshastighed på 10 til 40 ml / min og en hydrogen flowhastighed på 100 ml / min, når katalysatoren-sengs temperaturer er ved 100 ° C.
- Slukke varmelegemerne i reaktoren, trykket af systemet til omgivende tryk, og rense reaktoren med nitrogen i mindst 24 timer.
- Fjern reaktoren fra systemet, og fjern de brugte katalysatorer fra Reactor.
- Produkt behandling og resultat analyse
- For flydende produkt behandling, adskille de to faser og vejer individuelt. De flydende produkter er normalt i to faser, en let olie fase (olie produkt) og en tung vandig fase (vandig produkt).
- Gennemføre følgende analyser af olieprodukt: måling tæthed; Karl Fischer-titrering for vandindhold; grundstofanalyse (D5291 / D5373, D5373mod, og D1552 / D4239) for carbon, hydrogen, nitrogen, oxygen og svovl; semi-mikro farve indikator titrering (D3339) for total syretal; induktivt koblet plasma-optisk emission spektroskopi til uorganisk indhold; og simuleret destillation (ASTM D2887) for at vurdere de relative mængder af olieprodukter i benzin, diesel, flybrændstof, og resterende intervaller. Gennemføre følgende analyser af de vandige produkter: Karl Fischer-titrering for vandindhold og grundstofanalyse (D5291 / D5373) for carbon, hydrogen og nitrogen contelt 15.
- Beregn udbytter af producerede olie produkt, vandigt produkt, og gasformig produkt; brint forbrug; og massebalancen baseret på fjorden reaktant flow og tæthed, indløb brint gennemstrømning, olieudtag varens vægt, indhold af stikkontakten olieprodukt vand, afløb vandigt produkt vægt, outlet gasstrømmen, og udløb gassammensætning.
- Analyser brugte katalysatorer ved induktivt koblet plasma-optisk emission spektroskopi 15.
Representative Results
Hurtig pyrolyse af en repræsentativ urteagtige biomasse, præriegræs, med eller uden hot-damp filtrering og den katalytiske hydrobehandling af produktet bioolie anvendes som et eksempel for processen rapporteret her. Flere detaljer om disse forsøg kan findes i detaljer i vores nylige publikation. 15
Hot-damp-filtreret hurtig pyrolyse
Tabel 1 viser bioolie, char, og gasudbytter fremstillet med og uden hot-dampfilter for en typisk urteagtig råmateriale. For kontroleksperimentet uden varmt-damp filtrering, dampene ledes gennem filterhuset, men filteret blev ikke installeret. Dette holdt opholdstiden i de to eksperimenter samme så enhver forskel skyldes kun filteret. Bioolien udbyttet var 52% til 56%, hvilket indikerer vellykket omdannelse af størstedelen af biomassen til flydende intermediate olier. Et billede af en repræsentativ bioolie-prøve er vist i figur 4. Massebalancen lukninger var 86% til 90%. Lette dampe, der ikke er korrekt indsamlet i kondens toget var en kilde til massetab. Pyrolyseolier indeholder flere lavt kogepunkt forbindelser, såsom hydroxyacetaldehyd (kogepunkt 20,2 ° C), som er vanskelige at kondensere. Tilføjelse af en anden tøris fælde vil forbedre inddrivelsen af de lyse kondenserbare forbindelser. Udførelse eksperimenter med højere biomasse tilspændinger end rapporteret her vil forbedre inddrivelsen af de lette dampe ved at øge koncentrationen af dampe før kondens. Flugten af lette kondenserbare forbindelser kan verificeres ved gaschromatografi-massespektroskopi analyse af exit gas. De massebalancer var relativt lav for urteagtige råvare, sandsynligvis på grund af at undslippe lys char, som blev produceret fra præriegræs i relativt store mængder. Krakningsreaktioner forekomme på filteret, så ikonklusion af den varme-damp filter reducerede olieudbytte og øget gas udbytter.
Tabel 2 og figur 5 og 6 viser analyseresultaterne af urteagtige råmateriale og bio-producerede olie. Hot-damp filtrering reducerede aske rest i bio-olie fra 1,45% til under detektionsgrænsen. Forskellige uorganiske, såsom aluminium, calcium, jern, kalium, magnesium, natrium, phosphor og silicium, blev observeret i bio-olier, og de stammer hovedsageligt fra biomassen råmateriale. Hot-damp filtrering faldt betydeligt de uorganiske indhold i bio-olie, hvilket indikerer, at hot-damp-filtrering var en stærk protokol for effektivt at reducere indholdet af sporstoffer i bio-olier ved at fjerne char og aske partikler. Hot-damp-filtrering også faldt kulstofindholdet og øget iltindholdet i bio-olier. Woody råmaterialer har askeindhold lavt i forhold tilurteagtige råmaterialer, og lavere reduktioner i bio-olie-aske og uorganiske indhold overholdes. 15
Katalytisk hydrogenbehandling af bio-olie
Analyseresultaterne for den producerede bioolie stemte overens med det faktum, at bioolier fremstillet af sådan proces ikke er af tilstrækkelig kvalitet til direkte anvendelse i forbrændingsmotorer. Derfor er opgradering af bioolie påkrævet. De to bio-olieprøver blev opgraderet ved katalytisk hydrobehandling i hydrogenbehandler systemet under betingelserne beskrevet ovenfor.
Bio-olier er kendt for at sætte de hydrobehandlende reaktorer som chars eller polymerisationsprodukter af aktive arter i bio-olier ophobes i katalysatoren sengen. Derfor trykfaldet over katalysatorlejerne under hydrobehandling test er en vigtig indikator for akkumulere chars eller polymerisationsprodukter. Den varme-damp filtreret bio-olie udføres næsten fejlfrit i 60 timer TOS i hydrogenbehandlingsprocessen testen. Men den ufiltreret bioolie havde -5 vægt-% uopløste faste stoffer, som er adskilt i pumpen og blev ikke behandlet. Selv med disse ubehandlede faste stoffer, var der stadig et trykfald opbygning efter 50 timer TOS, sandsynligvis på grund af de tilbageværende faste stoffer i ufiltreret bioolie plukker det pakkede katalysatorleje.
Tabel 3 og 4 og 5 og 7 liste udbyttet af produkterne til bio-olie hydrogenbehandling på forskellige kast. Faseadskilt flydende produkter, herunder en opgraderet oliefase og en vandig fase, og gasformige produkter, herunder CH4, C 2H 6, C 3 H 8, C4 H 10, CO og CO2, blev produceret. Figur 4 viser et foto af en genoprejsende opgraderet olie prøve. tabel 5viser analyseresultaterne af opgraderede olie og Figur 5 sammenligner elementaranalyseresultater af bioolie og den opgraderede olie. Hydrobehandling var meget effektiv til at reducere oxygen, svovl og nitrogen og tilsætning af hydrogen signifikant fra bioolie feed. Oxygenindholdet i den opgraderede olie var ~2.0 vægt-%, hvilket er væsentligt lavere end 35 var til 40 vægt-% oxygen i bioolie-feed. Hydrogenet-til-carbon-forhold af den opgraderede olie var ~1.7, sammenlignet med ~1.3 for bioolie-feed. Tendensen til densiteten af den opgraderede olie, der steg fra 0,81 til 0,83 g / ml over testperioden, antyder en mild katalysatordeaktivering over 60 timers TOS.
Som vist i figur 7, sammenligninger af hydrobehandlede produkter mellem hot-damp filtreret og ufiltreret bioolie viste, at hot-damp filtreret bioolie førte til en lidt højere vand-til-olie-forhold opgraderet, hvilket er arrangemenstenten med højere iltindhold i hot-damp-filtrerede bioolie feed. Egenskaberne for opgraderede olie for de to bio-olier var meget ens. Den største forskel mellem hydrobehandling af hot-damp-filtreret og ufiltreret bioolie var, at de anvendte katalysatorbeds af hot-damp-filtrerede bioolie viste meget mindre aflejring af uorganiske forhold til katalysatoren brugte senge med ufiltreret bio-olier.
Figur 1. Skematisk for 5-cm fluidiseret leje pyrolyse reaktorsystem. Der er en hot-damp filter, en kondensering-system, og en gas-målesystem. Klik her for at se en større version af dette tal.
r /> Figur 2. Skematisk af mini-reaktoren hydrogenbehandler system. (MFC: massestrøm controller, RD: sprængskive; PT: tryktransducer, PI: tryk indikator (overtryk), BPR: back-trykregulator, PR: trykregulator) Klik her for at se en større version af dette tal.
Figur 3. Skematisk af katalysatorlejet i mini-hydrogenbehandler reaktor. Temperaturprofilen af katalysatorlejet er vist i den venstre og positionen af katalysatorer ifølge hvert trin er vist i den højre. Klik her for at se en større version af dette tal.
s / ftp_upload / 54.088 / 54088fig4.jpg "/>
Figur 4. Billeder af en repræsentativ bio-olie prøver (til venstre) og en repræsentant opgraderede olie prøve (til højre). Klik her for at se en større version af dette tal.
Figur 5. Sammenligning af elementaranalyseresultater af urteagtige råmateriale (rishirse), bio-olie fremstillet med hot-damp filtrering, og den opgraderede olie. Carbon, hydrogen og oxygen indhold ændrede sig ikke meget efter hurtig pyrolyse af biomasse imidlertid, iltindhold faldet betydeligt og hydrogenindhold steg efter bioolie hydrobehandling. Klik her for at se en større version af dette tal.
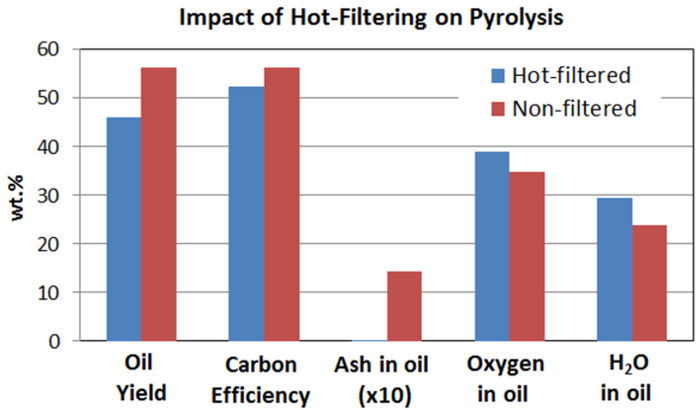
Figur 6. Sammenligning af olieudbytte, kulstofeffektivitet, og nogle egenskaber af bioolie fra hot-damp filtreret og ufiltreret pyrolyse. Dette viser virkningen af varm gas filtrering af pyrolysedampene før kondensation. Varm gas filtrering fjerner uorganiske rester, men det påvirker også pyrolyse olie udbytte [3-LM] og olie egenskaber såsom olie iltindhold. Klik her for at se en større version af dette tal.
Figur 7. Sammenligning af hydrobehandling resultater af bio-olier fra hot-damp filtreret og ikke-filtreret pyrolyse. Hot-damp filtreret bioolie fører til en lidt højere vand-til- brændstof forhold og egenskaber opgraderet brændstof til de to bio-olier er meget ens. Den største forskel mellem hydrobehandling af de to pyrolyseolier er, at katalysatorlejet af hot-damp-filtrerede bioolie viste meget mindre aflejring af mineraler. Klik her for at se en større version af dette tal.
Tabel 1. Udbytter af større pyrolyseprodukter (bio-olie, char og gas) og masse balance lukninger til pyrolyse af en urteagtige råmateriale (præriegræs) med og uden hot-damp filtrering.
Tabel 2. Analyse af den repræsentative urteagtige råmateriale (præriegræs) og bio-olie produceret med og uden hot-damp filtrering.
088table3.jpg "/>
Tabel 3. Udbytte af større hydrobehandling produkter på forskellige lodtrækningen for hot-damp filtreret og ufiltreret repræsentativ bioolie.
Tabel 4. Produceret gassammensætning under hydrobehandling af repræsentative bio-olier.
Tabel 5. Analyse af de opgraderede olieprodukter fra hydrobehandling af repræsentative bio-olier.
Discussion
I dette papir, beskrev vi en detaljeret procedure til konvertering lignocellulose biomasse til brændstof-range kulbrinter via hurtig pyrolyse og katalytisk hydrogenbehandling. NREL pyrolyse reaktorsystem med en 5-cm indre diameter hvirvellagsreaktor og PNNL hydrogenbehandler system med en 1,3-cm indre diameter fast leje katalytisk reaktor og deres operation procedurer er beskrevet i detaljer. Disse reaktorsystemer kunne bruges til at udføre pyrolyse og hydrobehandlende tests på en effektiv og sikker måde. Vi anvendte repræsentative urteagtige råmateriale ved fremstilling af flydende bioolier i pyrolysereaktoren systemet, og derefter blev de bioolier behandles i hydrobehandling system med en to-trins katalysatorleje herunder sulfideret Ru / C og CoMo / Al 2 O 3 som katalysatorer til fremstilling af brændstof-range flydende kulbrinter. Fremgangsmåden også er anvendelig til pyrolyse af en lang række biomasseråmaterialer herunder træ, græs og majsstængler og derefter opgradere den fremstilledebioolie til at producere biobrændstoffer. 16 hydrogenbehandler og hydrogenbehandlingsproces også vil kunne anvendes til opgradering af andre biomasse-genererede mellemprodukter såsom fortætning olie (bio-råt) fra biomasse såsom træ og alger.
Maksimering bioolie udbytte under pyrolyse kræver opvarmning af biomassen hurtigt til tilstrækkelig temperatur til at opnå maksimal fordampning af biomassen. For de fleste biomasse, betyder dette temperaturer på 500 til 600 ° C. En fluid bed giver hurtig varmeoverførsel fra sandet til biomassen, hvilket giver en høj opvarmningshastighed. Anvendelsen af små partikler tilvejebringer også en højere opvarmningshastighed. Typisk nogle få procent højere udbytte bioolie opnås med biomasse formalet til <0,5 mm, end med biomasse formalet til <2 mm. Maksimering udbytte betyder også minimere termisk krakning af dampene ved at holde opholdstiden ved temperaturen lav (1 til 2 sekunder). Pyrolysedampene indeholder forbindelser med en bred vifte af kogepunkter. Således hot rørføring tendens til at blive forurenet med væske, repolymerized dampe og char. For at undgå denne tilstand, holde sneglen temperatur under 100 ° C, og alle overflader mellem reaktoren og kondensation tog over 400 ° C for at undgå tilsmudsning, men under 500 ° C for at minimere termisk cracking. Grundig dækning med varme tape er nødvendig for at forhindre kuldebroer og sikrer en ensartet temperatur. Syet isolering puder med lukninger på dem generelt giver mere ensartet dækning, hvilket resulterer i mere ensartet temperatur. Det er vigtigt, at temperaturen falder hurtigt i den første kondensator for at minimere muligheden for repolymerization af høj kogepunkt materialer, der kunne føre til blokering af kondensatoren indløbet. Det er også nødvendigt at anvende tøris i den anden kondensator for at maksimere flydende genopretning og forebygge skader på gas-måle- og analyseinstrumenter.
Nogle forbedrede funktioner blev ikke nævnt i den grundlæggende hurtig pyrolyse procedure. jegt er nyttigt at have en trykmåler eller senderen i nærheden reaktorindløbet. Desuden er det nyttigt at måle trykforskellen over reaktoren og cyklon og måle endelige tryk og temperatur ved den tørre prøve meter (for at muliggøre nøjagtige volumenberegningerne). Det er også nyttigt at have yderligere termoelementer i pyrolyse sengen for at kontrollere, at sengen er fluidisering ensartet nok til at give ensartede temperaturer. Typisk <5 ° C spredning ses vertikalt gennem lejet. Det er også nyttigt at have indlejrede loop temperaturkontrol på reaktoren. Når en større mængde olie er behov, er det nyttigt at installere en ventil i bunden af trækullet modtager og montere en sekundær char modtager under det, hvilket igen har en ventil i bunden med en krukke løst monteret på den. Dette gør det muligt at tømme char modtageren ind i det sekundære modtager og endelig ned i glasset, således at kontinuerlig drift kan opretholdes i mange timer. Vibration er hjælpful til operationen. kan anvendes manuel omkuld af rørene, men en automatisk vibrator giver mere pålidelig omrøring. Disse kan drives kontinuerligt på låsen tragt og snegl port til at opretholde en jævn fødestrøm gennem forsyningskablet. Også ved hjælp af en automatisk vibrator på det sekundære char modtageren under char dræning gør denne operation meget mere pålidelig. Hot-damp filtrering forbedrer revnedannelse og reducerer bioolie udbytte som vist ovenfor. Idet temperaturen af filteret lav, men stadig over kondenseringstemperatur (> 400 ° C) minimerer revnedannelse. Et inert overflade på filteret kan også reducere revnedannelse. Filteret område skal være store for at reducere trykfald.
Den største begrænsning af hurtig pyrolyse fremgangsmåde er, at der produceres bioolie har nogle store problematiske egenskaber såsom høj viskositet, korrosivitet, dårlig flygtighed, lav brændværdi, og kemisk ustabilitet, hvilket begrænser deres direkte udnyttelse og forårsager nogle problemer during forbedringsarbejdet. 6,7,8,9 En variant af hurtig pyrolyse, katalytisk hurtig pyrolyse, hvor hurtig pyrolyse er integreret med en katalyse proces at opgradere pyrolyse damp, og hydropyrolysis, hvor hurtig pyrolyse udføres i nærværelse af reaktive gasser såsom H2, kan føre til en højere kvalitet bio-olie, men lider højere operationelle kompleksitet og lavt udbytte produkt. 4,8
To-trins katalytiske hydrogenbehandling viste gode forarbejdning resultater til konvertering bioolie til brændstof-range kulbrinter. Bio-olier er kendt for at være kemisk ustabile på grund af tilstedeværelsen af aktive arter såsom carbonyl- og phenolforbindelser, som kan undergå repolymerization og kondensering ved en lav temperatur, hvilket fører til en høj tilbøjelighed til at danne carbonholdige materialer og deraf katalysatordeaktivering og endog tilstopning af katalysatorleje. Derfor er det første trin hydrogeneringstrin var kritisk for processen, og blev anvendt til at stabilisere bio-olie ved hydrogenering af carbonyler og phenoler ved en relativ lav temperatur ved anvendelse af en ordentlig hydrogeneringskatalysator. Udførelsen af hydrogeneringskatalysatoren var nøglen til den langsigtede stabilitet og funktionsdygtighed af processen. Oxygen fjernelse ved hydrodeoxygenation indtraf i anden fase af et sulfid-baserede hydrobehandlingskatalysator. Udbyttet og egenskaber produceret endelige olieprodukt afhang af katalysatorer og betingelser, der anvendes i det andet trin. Maksimering af udbyttet af flydende endelige brændstoffer kan opnås ved anvendelse af katalysatorer, der kan skabe CC-bindinger, såsom alkylering funktion, og optimerede reaktionsparametre herunder reaktionstemperatur, tryk og rumhastighed. Den største begrænsning af hydrogenbehandlingsprocessen er, at på grund af nogle problematiske egenskaber i bioolie såsom kemisk ustabilitet og tilstedeværelsen af forureninger 17, levetid hydrobehandlingskatalysatorer, især de første trin hydrogeneringskatalysatorer, der stadig begrænseed, hvilket gør den samlede proces kostbar. Maksimere levetiden af katalysatorerne anvendte kunne opnås ved anvendelse af mere robuste katalysatorer; optimerede reaktionsparametre herunder reaktionstemperatur, tryk og rumhastighed; eller forbehandling for at sænke indholdet af den aktive art eller kontaminanter i bio-oil feeds.
Den hydrogenbehandler blev drevet ved høje tryk og reaktor temperaturer med brændbare gasser og væsker, der er involveret. Derfor bør sikkerhedsregler og procedure følges nøje.
Disclosures
Forfatterne erklærer, at de ikke har nogen konkurrerende finansielle interesser.
Acknowledgments
Dette arbejde blev støttet af det amerikanske Department of Energy (DOE) under kontrakt DE-AC36-08-GO28308 på NREL og Contract DE-AC05-76RL01830 på PNNL. Forfatterne takker støtte fra DOE s bioenergiteknologier Office.
Materials
Name | Company | Catalog Number | Comments |
Pyrolysis system | |||
Feedstock | Mill to pass 2 mm screen | ||
Sand for bed material | Black Rock | Screen to 300-500 microns | |
Furnace | Thermcraft | TSP-3.75-0-24-3C-J13667/1A | Split tube furnace 3.75 ID X 24 L |
Pyrolysis reactor | Custom-built at NREL | 2" diameter, height 17", dual staggered plate distributor, 316SS, Auger port is 2.5 cm above distributor and is cooled with air or water, there is a coiled 1/4" 304 SS tube below the distributor to pre-heat the gas | |
Cyclone | Custom-built at NREL | 1" diameter | |
Cyclone receiver | Custom-built at NREL | 1 L capacity | |
Cyclone secondary receiver | Custom-built at NREL | 1 L capacity | |
Hot vapor filter | Serv-A-Pure | SC2-0P10B34-X | 316SS, 10 inches long, 2.0 micron |
2-neck round-bottomed flasks | 500 ml | ||
Electrostatic precipitator | Allen Scientific Glassware, NREL-built electrodes | Custom built | 2" diameter 10" long ground electrode, glass enclosed, stop-cock on bottom |
High-voltage power supply | Spellman High Voltage | Bertan 803C-300P | 30 kV max, 0.5 mA |
Cold-finger condenser | Aldrich | Z164038 | |
Coalescing filter | Finite | 10C15-060 | |
Dry test meter | American Meter | DTM-200A | with IMAC counter |
Gas chromatograph | Varian | CP-4900 | MS5A, PBQ, CP-Sil columns |
Hydrogen detector | Gerhard Wagner | TCM-4 | thermal conductivity detector |
Non-Dispersive Infrared Spectrometer | California Analytical | Model 300 | Carbon monoxide 0-5%, 0-25%, carbon dioxide 0-5%, 0-20%, methane 0-5,000 ppmv, 0-3% |
Mass flow controller | Celerity (now Tylan) | Unit 7301 | 0-20 SLM reactor bottom, 0-10 SLM auger, 0-2 slm purges, 0-5 slm air |
Auger | Auger Manufacturing Specialists | 110520 | 3/8" Dia SS RH Auger 18" |
Motor for Auger | Leeson | Gearmotor-Parallel Shaft, 94 rpm, 1/15 HP, TEFC, 115 VAC | |
Feeding system: Motor for hopper | Lenze | VDE0530 | 7KB4-7-100H Motor Ac Helical Gearbox 3PH 0.25 kW 1.4/0.82 A |
Feeding system: Hopper and Loss in weight feeder | K-TRON Soder | KCL24T20 | with K10S controller |
Feeding system: Valves | Swagelok | SS-65TS16 | 151 bar at 37 °C and 6.8 bar at 232 °C |
Control system | Opto22 | SNAP-PAC parts | |
Heat cables | McMaster-Carr | 4550T152 and similar | Extreme-Temperature (1,400 °F), heavy insulation for use on metal |
Ball Vibrator | Vibtec | K 8 | |
U-tube | Custom-built at NREL | 1/4" PFA and stainless steel tubing, 1.4 m tall | |
Hydrotreating system | |||
Ru on carbon catalyst | Fabricated at PNNL | 7.6 wt% Ru on carbon | |
3% Co and 9% Mo on Al2O3 catalyst | Alfa-Aesar | 45579 | Cobalt oxide, typically 3.4-4.5%, Molybdenum oxide typically 11.5-14.5% on alumina |
Feeding pumps | ISCO | 500D | Syringe pump, 500 ml cylinder capacity |
Mass flow controller | Brooks | SLA5850S1BAF4B1A1 | |
Temperatrue controller | Cole-Parmer | WU-89000-10 | Digi-Sense Advanced Temperature Controller, 115 V |
Thermocouples | Omega | K-type thermocouples | |
Pressure transducer | Omega | PX309-3KG5V | |
Heat tapes | Cole-Parmer | EW-03106-27 | Dual element heating tape, 1/2 in x 12 ft, 936 watts, 120 VAC w/ 2-prong plug |
Digital pressure gauge | Omega | DPG4000-3K | High Accuracy Digital Pressure Gauge, with Data Logging Capability |
Back pressure regulator | Mity-Mite | ||
Gas flow meter | Mesa Labs | 200-220L | Dry Cal, Definer 220 Low Flow |
Hydrotreating reactor, cross, tee, fittings | Parker, Autoclave | ||
Combustible gas sensor | SMC | 5100-02-IT-S1-01-00-0-0 | Combustible gas detection sensor, 24 VDC power, analog 4-20 MADC output with modbus, no relays |
H2S sensor | SMC | 5100-05-IT-S1-01-00-0-0 | H2S toxic gas sensor module, 24 VDC power, analog 4-20 MADC output with modbus, no relays |
Ventilation sensor | TSI | FHM10 | Fume Hood Monitor FHM10 |
Micro-Gas chromatograph | Inficon | Inficon 3000 | Four-channel micro-GC with molecular sieve, Plot U, Alumina, and Stabilwax columns |
Lab-view based monitering and controlling system | Custom-built at PNNL | Using National Instruments parts and Labview software |
References
- BP. Statistical Review of World Energy. , http://www.bp.com/content/dam/bp/pdf/Energy-economics/statistical-review-2014/BP-statistical-review-of-world-energy-2014-full-report.pdf. (2014).
- U.S. Energy Information Administration. International Energy Outlook 2014. , http://www.eia.gov/forecasts/ieo/pdf/0484%282014%29.pdf (2014).
- Bioenergy Technologies Office. Replacing the Whole Barrel. , http://www1.eere.energy.gov/bioenergy/pdfs/replacing_barrel_overview.pdf. (2013).
- Huber, G. W., Iborra, S., Corma, A. Synthesis of transportation fuels from biomass: Chemistry, catalysts, and engineering. Chem. Rev. 106 (9), 4044-4098 (2006).
- Mohan, D., Pittman, C. U. J., Steele, P. H. Pyrolysis of wood/biomass for bio-oil: A critical review. Energy Fuels. 20 (3), 848-889 (2006).
- Bridgewater, A. V. Review of fast pyrolysis of biomass and product upgrading. Biomass Bioenergy. 29, 68-94 (2012).
- Elliott, D. C. Historical developments in hydroprocessing bio-oils. Energy Fuels. 21 (3), 1792-1815 (2007).
- Wang, H., Male, J., Wang, Y. Recent advances in hydrotreating of pyrolysis bio-oil and its oxygen-containing model compounds. ACS Catal. 3 (5), 1047-1070 (2013).
- Zacher, A. H., Olarte, M. V., Santosa, D. M., Elliott, D. C., Jones, S. B. A review and perspective of recent bio-oil hydrotreating research. Green Chem. 16, 491-515 (2014).
- Elliott, D. C., et al. Catalytic Hydroprocessing of Fast pyrolysis bio-oil from pine sawdust. Energy Fuels. 26 (6), 3891-3896 (2012).
- Venderbosch, R. H., Ardiyanti, A. R., Wildschut, J., Oasmaa, A., Heeresb, H. J. J. Stabilization of biomass-derived pyrolysis oils. Chem. Technol. Biotechnol. 85 (5), 674-686 (2010).
- Olarte, M. V., et al. Towards long-term fast pyrolysis oil catalytic upgrading. Prepr. Pap. Am. Chem. Soc., Div. Fuel Chem. 58 (2), 230-231 (2013).
- Scahill, J., Diebold, J. P., Feik, C. Removal of residual char fines from pyrolysis vapors by hot gas filtration. Developments in Thermochemical Biomass. Bridgwater, A. V., Boocock, D. G. B. , Blackie Academic and Professional. London, U.K. (1996).
- Hoekstra, E., Hogendoorn, K. J. A., Wang, X., Westerhof, R. J. M., Kersten, S. R. A., van Swaaij, W. P. M. Fast pyrolysis of biomass in a fluidized bed reactor: In situ filtering of the vapors. Ind. Eng. Chem. Res. 48 (10), 4744-4756 (2009).
- Elliott, D. C., Wang, H., French, R., Deutch, S., Iisa, K. Hydrocarbon liquid production from biomass via hot-vapor-filtered fast pyrolysis and catalytic hydroprocessing of the bio-oil. Energy Fuels. 28 (9), 5909-5917 (2014).
- Howe, D., et al. Field-to-Fuel Performance Testing of Lignocellulosic Feedstocks: An Integrated Study of the Fast Pyrolysis/Hydrotreating Pathway. Energy Fuels. 29 (5), 3188-3197 (2015).
- Wang, H., Wang, Y. Characterization of Deactivated Bio-oil Hydrotreating Catalysts. Topics in Catalysis. 59, 65-72 (2015).