Summary
对木质纤维素生物质生产生物油的快速热解和生物油生产燃料范围的烃的催化加氢实验方法介绍。快速热解过程中热蒸汽过滤从生物油去除细小炭颗粒和无机污染物也被评估。
Introduction
我们的社会严重依赖于化石燃料( 例如 ,石油,天然气,煤, 等等 )。这些资源是不可持续的能源和在迅速增加速率正在枯竭,导致关于减少的化石燃料资源, 二氧化碳排出环境后果,和经济问题的担忧。 1,2,3,4有替代和可持续能源的需求不断增加。生物质是生产液体燃料(生物燃料)和碳基化学品的,以取代在当前能源生产和转换系统的化石燃料的唯一的可再生和碳中的资源。 3,4
木质纤维素生物质( 如木材,草,能源作物,农业废弃物等 ),这是目前国际上最丰富和最便宜的生物质能源,吸引了最多的关注,以此来产生通过不同的热化学和生物路线生物燃料。 3,4
第一路径仅可利用木质纤维素生物质中的纤维素和半纤维素部分上。与升级集成热解被认为是用于直接生产生物燃料的一个短期可行的技术。
热解是木质纤维素生物质在无氧的400和550℃之间的温度下的热分解。 4,5,6,发生一些反应,如解聚,脱水,和C-C键裂解的热解过程中,并导致一种复杂的混合物邻的形成˚F200多含氧化合物。 4,5,6生物油中高收率(高达干饲料的75%(重量))可以与存储在保留生物质原料的能量的70%来制备。 4,5然而,直接使用所产生的热解生物油作为标准设备运输燃料是因为高的氧和水分含量,这会导致不同的物理和化学性质,如高粘度,腐蚀性,挥发性较差,低的问题热值,和稳定性差。 6,7,8,9因此,大量的除氧需要升级生物油燃料范围的碳氢化合物。使用固体催化剂在氢气催化加氢处理是由除氧通过加氢脱氧和加氢反应升级生物油中最常见的路线。 6,7,8,9
目前,为热解随后的加氢处理的主要挑战之一是实现长期稳定运行,特别是对加氢处理方法,其中,生物油和生物油无机和硫的残基的热不稳定性造成显著催化剂失活。 10,11-生物油的热稳定性已通过低温加氢处理以稳定生物油的活性种。通过除去无机残余物,它可以催化生物油馏分的再聚合并通过淀积停用的加氢处理催化剂11,12清理生物油,可能是有价值的。热蒸汽过滤是的技术通过热解过程中除去焦炭颗粒以有效地减少在生物油的无机内容之一。 13,14,15热蒸汽过滤使用热解反应器的下游以在高温下的蒸气冷凝之前,从热解气体/蒸气流炭细粒分离。 13,14,15
我们在这里报告生物质快速PYROL在国家可再生能源实验室(NREL)中使用的协议ysis既没有热蒸汽过滤以产生使用流化床反应器,并在太平洋西北国家实验室(PNNL)为生物油加氢处理以产生一个连续流动填充床催化反应器中的生物燃料的生物油。在反应器系统中,操作程序,以及处理和原料,生物油和生物燃料的分析的结构进行详细说明。具有或不具有热汽滤波和产生生物油的加氢处理的代表性生物量原料的热解处理的结果也与热蒸汽过滤的影响的评估呈现沿。
Protocol
1.快速热解与热蒸汽过滤
- 生物质原料的准备
- 磨的生物质的<2mm的粒度。存放在阴凉,干燥的地方。
- 组装热解系统
- 装配热解反应器。
- 炉内安装电抗器。流化氮,氮螺旋和空气线连接到反应器中。将螺旋进夹套螺旋口。连接冷却空气夹克。
- 安装和连接螺旋电机。
- 安装固体供给器30〜60厘米的正上方螺旋口的垂直开口。
- 固料机出口和螺旋口的垂直开口之间安装锁斗。连接到与尼龙编织螺旋口,钢筋25的内径乙烯管。固定油管的螺旋口用软管夹。连接具有重量轻,清,宽松的塑料滑动配合馈线。
- 旋风装配和热过滤器。
- 安装飓风和龙卷风入口连接到反应器出口。特写夫妇接收器旋风。
- 安装热过滤在过滤器壳体(具有2微米的孔尺寸由不锈钢制成)。连接气旋出口到热过滤器入口。氮气吹扫和卸压连接至气旋出口。
- 使用热胶带和绝缘毯子从旋风分离器入口到冷凝器入口加热的迹线。
- 组装聚光系统。
注:使用实验室千斤顶,环看台,和实验室夹挂载聚光系统的碎片在通风橱。- 为第一冷凝器,一对15至30厘米的1.2厘米(外径)的不锈钢管的硼硅酸盐管与标准锥形接头。连接放置在容器中塔第一冷凝器的500毫升两颈(标准锥)的圆底烧瓶中(接收器)ŧ将作为冰浴。使容器之间的连接这一点上与上磨口玻璃接头软管夹,球形接头,并且在玻璃器皿软管倒钩固定9至12毫米清晰乙烯管的下游。
- 第一冷凝器烧瓶中的出口连接到所述静电除尘器(ESP)的下侧端口(入口)。
- 在ESP的上侧端口(出口)连接到干冰阱(冷手指冷凝器)的小上部连接。
- 连接U型管的ESP和干冰阱之间的排队。填充U形管半满水。
- 干冰阱连接到一个500毫升两颈圆底置于容器中,将作为一个干冰浴烧瓶(接收器)。
- 连接凝聚过滤器的壳体的500毫升烧瓶中的入口(中央端口)的出口。
- 放置一个容器用于保持围绕过滤器壳体的底部干冰。
- 连接过滤器outle吨至干测试计和其他气体分析仪( 例如,非分散红外分析仪的CO,CO 2和CH 4,氢的热导率检测器和微型气相色谱仪(微GC)对CO CO 2,氮,氢,和C 1 -C 4烃类),然后放空。
注:示意图热解反应器系统的示于图1。生物质给料机,热解器,旋流器,热蒸汽过滤器的图片,并在热解反应器系统的冷凝器示于图S1至S5在补充文件。
- 装配热解反应器。
- 载热解反应器
- 倾200毫升砂(330克)的反应器中。
- 倒入2千克地上生物量的进料漏斗。
- 泄漏检查裂解系统
- 在冷凝器入口盖关闭系统。
- 加压至0.05MPa的或预期的最大工作压力,取其较高。确保以保持压力所需的流动是<200毫升/分钟。如果没有,找到并修复泄漏,并重复此步骤。
- 舒缓压力,摘帽系统,连接冷凝系统,在帽冷凝系统的出口端。
- 加压至0.01兆帕。确保的<200毫升流量/分钟保持的压力。如果没有,找到并修复泄漏,并重复此步骤。
- 减压和冷凝系统重新连接到仪器。
- 烧热反应堆
- 打开空气,设置流化氮气流冷却到3标准升/分钟和螺旋推运器的氮气流,以1标准升/分钟。
- 集炉目标温度至500℃和其他加热器400〜500℃。
- 斜升温以1至10℃/分钟的速率到目标温度。
- 准备工作
- 提高流化氮气流速至14标准升/分钟,螺旋推运器氮FLO瓦特率1.4标准升/分钟,并以0.5标准升/分钟的流速引入吹扫气体。大多数清洗的进入对气旋出口破裂盘端口。
- 在冰冷第一冷凝器填写洗澡。填写干冰陷阱,其接收器在容器中,容器周围用干冰凝聚过滤器。
- 监测温度聚结热电偶滤波器放置在过滤器的表面上的内和调节干冰水平所以它是0℃。
- 执行热解实验
- 打开锁斗阀(用4第二个周期)和螺旋。
- 打开ESP。根据需要设置的电压5〜10千伏至至少每2秒观察的弧。
- 借助micro-GC确认不存在氧。验证接通螺旋钻和封闭料斗没有引起在输出气体流量的减少,这将指示泄漏的存在。
- 以100克/小时打开进纸器。观察床温度和根据需要,以补偿增加的热负荷增加的设定点。
- 当温度在2℃下的500℃恢复到,100克/小时提高进料速率。重复该步骤直至420克进气量/到达小时。
- 每隔15分钟,记录床温度,进料供给器控制器,气体浓度对速率通过微气相色谱,干燥测试计速率,和系统压力通过压力表。验证ESP仍在正常电弧。根据需要应对在任何的这些变化。再填充冰和干冰。根据需要,沥干ESP到产品收集罐。
- 关闭
- 喂养1公斤生物质后,停止摄食。
- 气体浓度后已经衰减到稳态值低于10%,关闭所有加热器,调低流化流3个标准升/分钟和螺旋气流,以1标准升/分钟。关闭ESP,闭锁料斗阀门和螺旋。
- 允许打开热段之前的系统冷却(4-6小时)。 </ OL>
- 收集的液体产品和焦炭。
- 称冷凝器系统的各个部分,以获得总液收。倾从冷凝器接收液体到一个共同的罐子或瓶子。或者,用丙酮清洗玻璃器皿。
- 空字符接收到一个罐子。删除热过滤,空外壳,并且过滤器刷掉流入焦炭罐。称量过滤器。删除和权衡床料。使用高效真空与此服务的淘汰赛容器。
- 氧化系统。
- 密封该反应器,旋风接收机,并清洗热过滤。检查是否漏气,如第1.4如上所述。
- 安装从冷凝器入口的金属线的凝聚过滤器的出口处,以绕过冷凝系统。
- 加热该反应器至550℃,3标准L / min的氮气作为流化气体和1标准升/分钟螺旋推运器的氮气流。
- 加入空气流化加油站。开始以0.2标准升/分钟,逐渐增加至4升/分。继续直到CO + CO 2的浓度是小于0.1%。
- 计算收益率。
- 计算液体收率作为冷凝系统的质量的整体变化。
- 计算焦炭产率,为在床中,热过滤器的重量变化的重量变化的总和,和从旋风分离器接收机和热过滤器外壳收集炭。
注:其他炭可以从系统的氧化来估计,但是这通常是不重要的。 - 计算气体产率从GC和干测试计的流率测量的气体的浓度的气态产物的总重量计。
2.生物油催化加氢
注:在NREL产生的生物油样品运到西北太平洋国家实验室的加氢处理系统上的催化加氢处理。
- 加氢处理系统
- 确保加氢处理系统处于运行状态通过检查每个组件。
注:所用的加氢处理反应器系统被配置为单通,顺流,连续的,向下流动催化反应器中。该系统由三个主要部分组成:1)一个气体和液体进料组分,2)加热的反应器,和3)的气-液产品分离成分( 图2)。该系统被设计以高达13.6兆帕操作(2000 psig的;最大操作压力),最高催化剂温度500℃(只在反应器的额定功率为此温度)。 - 确保加氢处理监测和控制系统和安全控制系统在运行条件。
注:该系统监控,并通过与各种传感器的内部内置计算机程序部分控制。传感器包括用于反应器的热电偶和压力传感器以及氢和通风蟾酥RS在该反应器所在的机箱。数据由程序来监视反应器记录。出口气体流速由流量计测量,并且数据由所附软件记录。该方案还控制反应堆主要设备的电源。在实验过程中,如果反应器经受的具体的压力变化和/或温度的变化,或可燃气体术语中的操作条件的不希望的变化是本以上的安全性的限制,和/或如果通风系统出现故障时,程序自动可以关闭系统,以确保安全。泄压阀和一个破裂盘也被安装在加氢处理系统,以防止过压。
- 确保加氢处理系统处于运行状态通过检查每个组件。
- 催化剂加载和预处理
- 催化剂制备
- 粉碎两种催化剂,钌/碳,作为阶段I催化剂和的CoMo / 的 Al 2 O 3作为阶段-Ⅱ催化剂,和筛留住0.25至0.60毫米(30至60目)颗粒。
注:钌/碳催化剂在内部制备的CoMo / 的 Al 2 O 3催化剂是商业产品。
- 粉碎两种催化剂,钌/碳,作为阶段I催化剂和的CoMo / 的 Al 2 O 3作为阶段-Ⅱ催化剂,和筛留住0.25至0.60毫米(30至60目)颗粒。
- 催化剂装载到反应器
- 使用不锈钢管和屏幕作为用于催化剂床的支持介质。慢慢倒入阶段-II的催化剂颗粒,在阶段I催化剂颗粒,和原来的阶段I催化剂挤出物,其中用作分配器,进入反应器顺序地,同时在反应器的外面“窃听”,以形成填充催化剂床。负载32 ml的每种催化剂的形成用24毫升每种催化剂的位于等温区( 图3)的两级催化床。
- 安装在反应器的加氢处理系统
- 放置在反应器入加氢处理系统通过安装两个加热器,然后将反应器连接到气体和液体进料组分和气体 - 液体分离组件。
注:两个热带加热铝护套包围的管式反应器提供热量。每一个被加热护套独立使用期间催化剂预处理和加氢处理试验期间加热反应器的部分。每个铝护套包裹着的高温热胶带和绝缘,并用温度控制器加热。管状固定床催化反应器是由316不锈钢,用13毫米内径和64厘米的长度。热电偶孔(4.7毫米外直径×)位于反应器的中心,和两个热电偶放置在井以测量催化剂床的温度。
- 放置在反应器入加氢处理系统通过安装两个加热器,然后将反应器连接到气体和液体进料组分和气体 - 液体分离组件。
- 检查加氢处理器系统的使用12.0兆帕的氮气通过保持该系统中的压力,并确保的压力下降是每小时低于1 psig的泄漏的压力。
- 催化剂的预处理。硫化物原位催化剂在氢气和硫化剂的流动。
- 在242毫升/分钟氢气120℃/小时的速率加热,从室温至150℃两催化剂床。
- 同时维持催化剂床的温度在150℃下在242毫升/小时的氢气2小时,以0.128毫升/分钟(35%(重量)二叔butyldisulfide在癸烷中由进给泵供给)硫化剂。
- 加热阶段我床从150至250℃,在83.3℃/ hr的速度,并在250℃下保持5.8小时。在同一期间,加热阶段-II床从150至400℃,在83.3℃/ hr的速度,并在400℃下保持4小时。在手术过程中,保持反应器的压力为10.3兆帕,所述硫化剂的流速在0.128毫升/分钟,并在242毫升/分钟的氢气流速。
- 停止硫化剂流量,保持氢气流量。然后将床到所需的反应温度的各催化剂的温度。
注:硫化剂流量由使用催化剂的量和0.12毫升/毫升的猫/ hr的整体催化剂的硫化剂液体时空速(LHSV)来确定。氢气流速是由硫化剂的流速和在1890毫升氢/ ml的硫化剂液体中的氢与硫化剂流量比来确定。加氢处理系统的气体和液体供给组件包括两个高压注射器泵。一两个泵被用来喂硫化剂。气体和硫化剂被引入到它们向下穿过反应器中的催化剂床通之前的液体被混合的反应器的预反应器区。
- 催化剂制备
- 生物油加氢
- 调整氢气流至152毫升/分钟并保持在10.3兆帕系统压力。设置了阶段-I催化剂床和阶段II催化剂床的温度为220和400℃,分别。
注:钍È氢气流量由催化剂的使用量来确定,0.20毫升/毫升的猫/小时对于每个阶段,氢对生物油比1900毫升氢/ ml的生物油的生物油的LHSV 。 - 记录时的温度,压力,以及氢气流成为稳定的床温与氢气流量基准。
- 在的量等于150ppm的硫在生物油添加二硫化物二叔丁基对生物油进料。填充生物油进料在进料泵中的一个并吹扫馈送线,直到液体流是不含气泡的实现。
- 加压泵至10.3兆帕,然后通过打开连接阀连接到反应器中。开始在4.8毫升/小时的流速进料生物油。此操作将启动生物油加氢试验。
注:生物油流量由所使用的催化剂的量和0.20毫升/毫升的猫/ hr的每个阶段的生物油的LHSV确定。氢气和生物油被引入到反应器中,其中的预反应器区气体和液体它们在反应器中通过催化剂床的假定滴流向下传递之前进行混合。 - 检查该反应器的状态并记录参数,如温度,压力,流速和体积,周期性。确保在催化剂床温度在±2℃的所需温度的,气体和液体流速是完全一样的所需设置,反应器压力在±期望的压力为0.15兆帕。确保在整个催化剂床的压降是<0.35兆帕。
注:该系统监控,并通过与各种传感器的内部内置计算机程序部分控制。传感器包括在所述反应器所在的机箱的反应器中的热电偶和压力传感器以及氢和通风传感器。 - 通过一个在线微GC引导废气分析出口气体样品每2小时。
注:微GC是一个四陈荫罴埃尔微型气相色谱仪和每个测试加氢处理之前,使用校准气体校准。 - 收集液体样品用下列步骤,每6小时:采样阱切换到旁路陷阱,降低采样阱的压力,沥干液体样品收集小瓶中,用氮气吹扫采样陷阱中,用氮气加压采样陷阱,和重定向产品流向抽样陷阱。操作的一系列转移在所需方向中的气体和产品的二维和三通阀。
注意:一旦反应物通过催化剂床,所述液体产物和未反应液体从气体产物和未反应的气体在气 - 液分离系统分离。热气体通过设置在反应器系统中的并行下游2加压,冷却,液/气冷阱(样品陷阱或旁路阱)中的一个。废气然后经过背压调节器,其中的压力减小到情调heric压力。废气然后通过燃气表通过测量流速。 - 进行测试60小时的流(时间流[TOS])。通过停止生物油进料终止测试。设定反应器的温度至100℃,氢气流速为100毫升/分。
注:测试可以为折腾操作,从五十到几百个小时。
- 调整氢气流至152毫升/分钟并保持在10.3兆帕系统压力。设置了阶段-I催化剂床和阶段II催化剂床的温度为220和400℃,分别。
- 后测试程序
- 用丙酮来清洁用于馈送生物油输送泵。装载用丙酮清洗过输送泵。
- 吹扫与~400毫升丙酮的催化剂床,以10至40毫升/分的丙酮流速为100毫升/分钟的氢气流速,当催化剂床温度在100℃。
- 关闭反应器的加热器,减压系统环境压力,并用氮气吹扫该反应器在至少24小时。
- 从系统中移除反应堆,并从reacto取出废催化剂河
- 产品加工及结果分析
- 用于液体产品的处理,分离两相并单独称重。液体产物通常是在两个阶段中,光油相(油产物)和重的水相(含水产品)。
- 进行油产物的下列分析:密度测量;卡尔费休滴定水含量;元素分析(D5291 / D5373,D5373mod,和D1552 / D4239)为碳,氢,氮,氧和硫;半微量颜色指示剂滴定(D3339)的总酸值;电感耦合无机内容等离子体 - 光发射光谱;和模拟蒸馏(ASTM D2887),以评估在汽油,柴油,喷气燃料,和残余范围燃料产品的相对量。进行水性产品的下列分析:卡尔·费歇尔滴定法测定碳,氢和氮CON含水量和元素分析(D5291 / D5373)10吨15。
- 计算产生的油产品,含水的产品,和气态产物的产率;氢气消耗;并且基于该入口的反应物的流速和密度,入口氢流量,出口油产品重量,在出口油产品的水含量的质量平衡,出口含水产品重量,出口气体流速和出口气体组成。
- 通过电感耦合等离子体发射光谱仪分析15花费的催化剂。
Representative Results
有代表性的草本生物质的快速热解,柳枝稷,有或没有热蒸汽过滤,产物生物油的催化加氢被用作这里所报告的过程的例子。这些实验的更多细节可以在细节在我们最近的出版物中找到。 15
热蒸汽过滤快速热解
表1示出了生物油,焦炭,和有和没有用于典型草本原料中的热蒸汽过滤器产生的气体产量。对于没有热蒸汽过滤对照实验中,蒸气通过虽然过滤器壳体,但没有安装过滤器。此保持的停留时间在两个实验相同的,所以任何差异是由于只过滤器。生物油收率分别为52%至56%,这表明在液体中间生物质的主要部分的转换成功德油。有代表性的生物油样品的照片示于图4。质量平衡封锁分别为86%至90%。那些没有正确地在冷凝火车收集的光蒸汽是质量损失的一个来源。热解油含有几种低沸点化合物,如羟基乙醛(沸点20.2℃),这是难以冷凝。加入第二干冰阱将提高光冷凝化合物的回收。进行实验比此报告将冷凝之前蒸气浓度的增加提高光蒸汽回收的生物量较高的进给率。的光可冷凝化合物的逃逸可通过出口气体的气相色谱 - 质谱分析进行验证。质量余额为逃避因焦炭光,这是由相对大量柳枝制作的比较低的草本原料,有可能。裂化反应发生在过滤器,以便在热蒸汽滤波器的包涵体降低油的产率和增加了气体的产率。
表2和图5和6显示草本原料的分析结果和所产生的生物油。热蒸汽滤波减少在生物油的灰残余物从1.45%到检测限以下。各种无机物,如铝,钙,铁,钾,镁,钠,磷和硅,在生物油中观察到,它们主要是从生物质原料来源。在生物油热蒸汽过滤显著降低无机内容,表明热蒸汽过滤是通过除去炭和灰的颗粒有效地减少了生物油微量元素内容的强大的协议。热蒸汽滤波也降低了碳含量和增加的生物油中的氧含量。相比伍迪原料具有低灰分含量草本原料,并在生物油灰低级减量和无机内容被观察到。 15
生物油催化加氢
所产生的生物油的分析结果与事实由这种方法生产的生物油是足够的质量为在内燃机直接使用并不一致。因此,需要生物油的升级。两个生物油样品通过在上面讨论的条件下加氢处理系统的催化加氢处理进行升级。
生物油是公知的,以堵塞加氢处理反应器中作为字符或在生物油活性种的聚合产物积聚在催化剂床。因此,在加氢处理试验在整个催化剂床的压降积累字符或聚合产品的一个重要指标。热蒸汽过滤bIO-油加氢处理测试中表现完美了近60小时的TOS值。然而,未过滤的生物油具有约5%(重量)不溶解的固体,这在泵分离出来,并没有进行处理。即使有这些未处理的固体,仍有堵塞填充催化剂床50小时TOS,因为在非滤波生物油的残余固形物的大概后的压降积累。
表3和4以及图5和7列表产品在不同TOSS生物油加氢处理的产率。析相液体产品,包括升级油相和水相,和气态产物,包括CH 4,C 2 H 6,C 3 H 8,C 4 H 10,CO,和CO 2,制作了。 图4示出了修复升级油样品的照片。 表5示出升级油的分析结果和图5中的生物油和升级油的元素分析结果进行比较。加氢处理是在减少氧,硫和氮,并从生物油进料显著添加氢非常有效。在升级后的油中的氧含量为~2.0重量%,这是显著低于35向生物油原料中氧的40%(重量)。升级油中的氢 - 碳比为~1.7,相比~1.3为生物油进料。已升级的油,从而增加从0.81至0.83的密度的趋势微克/毫升在测试期间,表明在60小时TOS温和的催化剂失活。
正如图7所示,过滤热蒸汽和非滤波生物油之间加氢产物的比较表明热蒸汽过滤生物油导致稍高水与升级油比,这是consi与热蒸汽过滤生物油原料中的氧含量较高的支架来说。升级油的两个生物油的性质非常相似。热蒸汽的过滤和未过滤的生物油的加氢处理的主要区别是,热蒸汽过滤生物油的使用过的催化剂床呈无机物的少得多沉积相比于用非滤波中使用的催化剂床生物油。
图1原理图对5厘米的流化床热解反应器系统。还有一个热汽滤波器,一个冷凝系统,和一个气体测量系统。 请点击此处查看该图的放大版本。
转/> 图2中的微型反应器加氢系统的原理图。 (MFC:质量流量控制器; RD:爆破片; PT:压力传感器; PI:压力指示器(表压); BPR:背压调节器; PR:压力调节器) 点击此处查看该图的放大版本。
图3原理图在迷你加氢反应器的催化剂床的。催化剂床的温度分布示于左侧和各阶段的催化剂的位置在右示出。 请点击此处查看该图的放大版本。
S / ftp_upload / 54088 / 54088fig4.jpg“/>
图4.具有代表性的生物油样品(左)和具有代表性的升级油样(右)的照片。 请点击此处查看该图的放大版本。
图5的草本质原料(柳枝稷),生物油与热蒸汽过滤产生的,并已升级的石油的元素分析结果的比较。碳,氢,和氧含量的生物质的快速热解后没有太大变化,但是,氧气含量显著降低和生物油加氢处理后的氢含量增加。 请点击此处查看该图的放大版本。
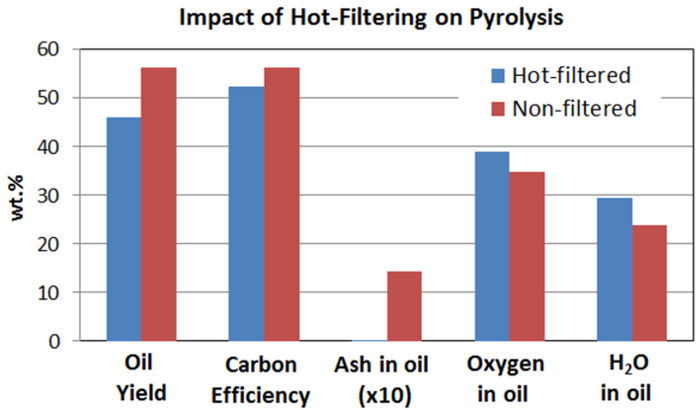
图6.比较出油率,碳效率,以及滤波的热蒸汽和非过滤热解生物油的某些属性。这表明前缩合裂解的蒸气的热气体过滤的影响。热气体过滤消除无机残基,但它也影响热解油收率[3- LM]和油性能,例如油的氧含量。 请点击此处查看该图的放大版本。
图7.从滤波的热蒸汽和非滤波热解生物油的加氢处理的结果的比较。热蒸汽过滤生物油导致稍高的水用于─燃料比及升级燃料的两个生物油的性质非常相似。两个热解油的加氢处理之间的主要区别是,床的热汽过滤生物油的催化剂显示出的矿物质少得多的沉积。 请点击此处查看该图的放大版本。
表1的主要裂解产物(生物油,焦炭,和气体)和草本植物质原料(柳枝稷)的热解质量平衡封闭带和不带热蒸汽过滤产量的影响。
表2.分析代表草本原料(柳枝稷)和生物油带和不带热蒸汽过滤产生的。
088table3.jpg“/>
表在不同折腾了滤波的热蒸汽和非过滤代表生物油的加氢主要产品。产量。
表4.代表性的生物油加氢处理过程中产生的气体成分。
表5.分析升级石油产品代表生物油的加氢处理的。
Discussion
在本文中,我们描述了通过快速热解和催化加氢处理木质纤维素生物质转化成燃料的烃类范围的详细过程。用5厘米的内径流化床反应器,并用1.3厘米内径固定床催化反应器和它们的操作的程序PNNL加氢处理系统中的可再生能源实验室热解反应器系统进行详细说明。这些反应器系统可以用于以有效和安全的方式进行热解和加氢处理试验。我们使用代表草本原料来生产在热解反应器系统的液体生物油,然后,将生物油在加氢处理系统进行了处理用的两级催化床包括硫化的钌/碳和的CoMo /的Al 2 O 3作为催化剂,以产生燃料范围的液态烃。该方法也适用于大范围的生物质原料的,包括木材,草,玉米秸秆的热解,然后提升生产生物油生产生物燃料。 16加氢处理和加氢处理方法也可用于升级其他生物质生成的中间体,如液化油状物(生物粗品)从生物质,例如木材和藻类。
热解过程中最大限度地提高生物油产量,需要快速加热的生物质至足够的温度以实现生物质的最大挥发。对于大多数的生物量,这意味着在500〜600℃的温度。流化床提供从砂快速热传递到生物质,提供高加热速率。使用小颗粒也提供了更高的加热速率。通常情况下高出几个百分点的生物油产量与地上生物量要达到<0.5毫米比地面生物量<2毫米。最大化产量也意味着通过保持的停留时间在温度低(1至2秒)最小化蒸汽的热裂解。热解蒸汽包含具有宽沸点范围的化合物。因而,对hOT管道趋于液体,蒸汽repolymerized和char犯规。为了避免这种情况,保持螺旋钻温度低于100℃,在反应器和冷凝列车400℃以上,以避免污染之间的所有表面,但低于500℃,以减少热裂化。全面覆盖热胶带有必要防止冷点,并提供均匀的温度。其上具有封闭件缝合绝缘垫片通常提供更均匀的覆盖,从而导致更均匀的温度。重要的是温度在第一冷凝器迅速下降,以尽量减少高沸点材料,这可能导致在冷凝器入口的堵塞的再聚合的机会。它也有必要使用干冰在第二冷凝以最大化液体回收,并防止气体的测量和分析仪器的损害。
一些增强功能并没有基本的快速热解过程中提到。一世t是非常有用的压力计或发射机靠近反应器入口。此外,它是有用的测量穿过反应器和旋风分离器压差,并测量在干燥测试计的最终压力和温度(以实现精确体积计算)。它也有利于在该热解床附加的热电偶,以验证该床流化均匀地足以提供均匀的温度。典型地,<5℃传播垂直通过床看到。它也是有在反应器嵌套循环的温度控制是有用的。当需要的油用量较大,它是有帮助的上焦炭接收器的底部安装一个阀门并装入低于次级炭接收机,这反过来又具有与罐底部的阀松散地安装到它。这使得有可能以清空焦炭接收到辅助接收机,最后向下进入罐子以便连续操作可保持很多小时。振动是帮助FUL的操作。管道的手动冲击都可以使用,但自动振动器提供了更可靠的搅拌。这些可以连续封闭料斗和螺旋推运器的端口上被操作以维持流经送料器的平滑进料流。此外,使用对char排水期间二次炭接收机的自动振动器使得该操作更可靠。热蒸汽过滤可增强龟裂和减少生物油收率如上所示。保持过滤器的温度低,但仍高于冷凝温度(> 400℃),最大限度地减少开裂。在过滤器上的惰性表面也可减少开裂。该过滤器区需要是很大的,以减少压力降。
的快速热解过程的主要限制是,所产生的生物油有一些重大问题的性质,如高粘度,腐蚀性,挥发性较差,低热值,和化学不稳定性,这限制了它们直接利用,并导致一些问题杜尔ING的升级。 6,7,8,9快速热解,催化快速热解,其中快速热解是用催化过程集成到升级热解蒸汽和水热解的方法,其中快速热解在反应性气体如H 2的存在下进行的一种变体,能导致更高质量的生物油,但遭受更高的操作的复杂性和低的产品产率。 4,8
两段催化加氢显示出良好的处理结果,用于将生物油燃料范围的烃。生物油是已知的,因为活性物质,如,可以在低温下进行再聚合和缩合羰基和酚化合物的存在下的化学性质不稳定,从而导致高的倾向以形成含碳材料和由此产生的催化剂失活,甚至堵塞的催化剂床。因此,第一级加氢步骤是该过程的关键,并被用来稳定双向邻 - 油通过在相对低的温度羰和酚醛塑料的氢化,通过使用一个适当的氢化催化剂。氢化催化剂的性能的过程的长期稳定性和可操作性的键。除氧通过加氢脱氧发生在通过基于硫化物的加氢处理催化剂的第二阶段。产率和产生的最终油产品的性能取决于在第二阶段中所用的催化剂和条件。最大化液体最终燃料的产率可以通过使用能够产生CC键,如烷基化的功能的催化剂,并优化反应参数,包括反应温度,压力和空间速度来实现。的加氢处理方法的主要限制是,由于在生物油一些问题性质如化学不稳定性和污染物17的存在下,加氢处理催化剂的寿命,尤其是在第一步骤的氢化催化剂,都仍然限制版,这使得整个工艺昂贵。最大化使用可以通过使用更健壮的催化剂来实现,催化剂的寿命;优化反应参数,包括反应温度,压力和空间速度;或预处理,以降低活性种或污染物的生物油进料的内容。
加氢处理是在高压和反应器温度与所涉及可燃气体和液体进行操作。因此,安全规则和程序应严格遵守。
Disclosures
作者宣称,他们没有竞争的经济利益。
Acknowledgments
这项工作是由美国能源署(DOE)根据合同DE-AC36-08-GO28308在NREL和合同DE-AC05-76RL01830在西北太平洋国家实验室的支持。作者非常感谢美国能源部生物能源科技厅的支持。
Materials
Name | Company | Catalog Number | Comments |
Pyrolysis system | |||
Feedstock | Mill to pass 2 mm screen | ||
Sand for bed material | Black Rock | Screen to 300-500 microns | |
Furnace | Thermcraft | TSP-3.75-0-24-3C-J13667/1A | Split tube furnace 3.75 ID X 24 L |
Pyrolysis reactor | Custom-built at NREL | 2" diameter, height 17", dual staggered plate distributor, 316SS, Auger port is 2.5 cm above distributor and is cooled with air or water, there is a coiled 1/4" 304 SS tube below the distributor to pre-heat the gas | |
Cyclone | Custom-built at NREL | 1" diameter | |
Cyclone receiver | Custom-built at NREL | 1 L capacity | |
Cyclone secondary receiver | Custom-built at NREL | 1 L capacity | |
Hot vapor filter | Serv-A-Pure | SC2-0P10B34-X | 316SS, 10 inches long, 2.0 micron |
2-neck round-bottomed flasks | 500 ml | ||
Electrostatic precipitator | Allen Scientific Glassware, NREL-built electrodes | Custom built | 2" diameter 10" long ground electrode, glass enclosed, stop-cock on bottom |
High-voltage power supply | Spellman High Voltage | Bertan 803C-300P | 30 kV max, 0.5 mA |
Cold-finger condenser | Aldrich | Z164038 | |
Coalescing filter | Finite | 10C15-060 | |
Dry test meter | American Meter | DTM-200A | with IMAC counter |
Gas chromatograph | Varian | CP-4900 | MS5A, PBQ, CP-Sil columns |
Hydrogen detector | Gerhard Wagner | TCM-4 | thermal conductivity detector |
Non-Dispersive Infrared Spectrometer | California Analytical | Model 300 | Carbon monoxide 0-5%, 0-25%, carbon dioxide 0-5%, 0-20%, methane 0-5,000 ppmv, 0-3% |
Mass flow controller | Celerity (now Tylan) | Unit 7301 | 0-20 SLM reactor bottom, 0-10 SLM auger, 0-2 slm purges, 0-5 slm air |
Auger | Auger Manufacturing Specialists | 110520 | 3/8" Dia SS RH Auger 18" |
Motor for Auger | Leeson | Gearmotor-Parallel Shaft, 94 rpm, 1/15 HP, TEFC, 115 VAC | |
Feeding system: Motor for hopper | Lenze | VDE0530 | 7KB4-7-100H Motor Ac Helical Gearbox 3PH 0.25 kW 1.4/0.82 A |
Feeding system: Hopper and Loss in weight feeder | K-TRON Soder | KCL24T20 | with K10S controller |
Feeding system: Valves | Swagelok | SS-65TS16 | 151 bar at 37 °C and 6.8 bar at 232 °C |
Control system | Opto22 | SNAP-PAC parts | |
Heat cables | McMaster-Carr | 4550T152 and similar | Extreme-Temperature (1,400 °F), heavy insulation for use on metal |
Ball Vibrator | Vibtec | K 8 | |
U-tube | Custom-built at NREL | 1/4" PFA and stainless steel tubing, 1.4 m tall | |
Hydrotreating system | |||
Ru on carbon catalyst | Fabricated at PNNL | 7.6 wt% Ru on carbon | |
3% Co and 9% Mo on Al2O3 catalyst | Alfa-Aesar | 45579 | Cobalt oxide, typically 3.4-4.5%, Molybdenum oxide typically 11.5-14.5% on alumina |
Feeding pumps | ISCO | 500D | Syringe pump, 500 ml cylinder capacity |
Mass flow controller | Brooks | SLA5850S1BAF4B1A1 | |
Temperatrue controller | Cole-Parmer | WU-89000-10 | Digi-Sense Advanced Temperature Controller, 115 V |
Thermocouples | Omega | K-type thermocouples | |
Pressure transducer | Omega | PX309-3KG5V | |
Heat tapes | Cole-Parmer | EW-03106-27 | Dual element heating tape, 1/2 in x 12 ft, 936 watts, 120 VAC w/ 2-prong plug |
Digital pressure gauge | Omega | DPG4000-3K | High Accuracy Digital Pressure Gauge, with Data Logging Capability |
Back pressure regulator | Mity-Mite | ||
Gas flow meter | Mesa Labs | 200-220L | Dry Cal, Definer 220 Low Flow |
Hydrotreating reactor, cross, tee, fittings | Parker, Autoclave | ||
Combustible gas sensor | SMC | 5100-02-IT-S1-01-00-0-0 | Combustible gas detection sensor, 24 VDC power, analog 4-20 MADC output with modbus, no relays |
H2S sensor | SMC | 5100-05-IT-S1-01-00-0-0 | H2S toxic gas sensor module, 24 VDC power, analog 4-20 MADC output with modbus, no relays |
Ventilation sensor | TSI | FHM10 | Fume Hood Monitor FHM10 |
Micro-Gas chromatograph | Inficon | Inficon 3000 | Four-channel micro-GC with molecular sieve, Plot U, Alumina, and Stabilwax columns |
Lab-view based monitering and controlling system | Custom-built at PNNL | Using National Instruments parts and Labview software |
References
- BP. Statistical Review of World Energy. , http://www.bp.com/content/dam/bp/pdf/Energy-economics/statistical-review-2014/BP-statistical-review-of-world-energy-2014-full-report.pdf. (2014).
- U.S. Energy Information Administration. International Energy Outlook 2014. , http://www.eia.gov/forecasts/ieo/pdf/0484%282014%29.pdf (2014).
- Bioenergy Technologies Office. Replacing the Whole Barrel. , http://www1.eere.energy.gov/bioenergy/pdfs/replacing_barrel_overview.pdf. (2013).
- Huber, G. W., Iborra, S., Corma, A. Synthesis of transportation fuels from biomass: Chemistry, catalysts, and engineering. Chem. Rev. 106 (9), 4044-4098 (2006).
- Mohan, D., Pittman, C. U. J., Steele, P. H. Pyrolysis of wood/biomass for bio-oil: A critical review. Energy Fuels. 20 (3), 848-889 (2006).
- Bridgewater, A. V. Review of fast pyrolysis of biomass and product upgrading. Biomass Bioenergy. 29, 68-94 (2012).
- Elliott, D. C. Historical developments in hydroprocessing bio-oils. Energy Fuels. 21 (3), 1792-1815 (2007).
- Wang, H., Male, J., Wang, Y. Recent advances in hydrotreating of pyrolysis bio-oil and its oxygen-containing model compounds. ACS Catal. 3 (5), 1047-1070 (2013).
- Zacher, A. H., Olarte, M. V., Santosa, D. M., Elliott, D. C., Jones, S. B. A review and perspective of recent bio-oil hydrotreating research. Green Chem. 16, 491-515 (2014).
- Elliott, D. C., et al. Catalytic Hydroprocessing of Fast pyrolysis bio-oil from pine sawdust. Energy Fuels. 26 (6), 3891-3896 (2012).
- Venderbosch, R. H., Ardiyanti, A. R., Wildschut, J., Oasmaa, A., Heeresb, H. J. J. Stabilization of biomass-derived pyrolysis oils. Chem. Technol. Biotechnol. 85 (5), 674-686 (2010).
- Olarte, M. V., et al. Towards long-term fast pyrolysis oil catalytic upgrading. Prepr. Pap. Am. Chem. Soc., Div. Fuel Chem. 58 (2), 230-231 (2013).
- Scahill, J., Diebold, J. P., Feik, C. Removal of residual char fines from pyrolysis vapors by hot gas filtration. Developments in Thermochemical Biomass. Bridgwater, A. V., Boocock, D. G. B. , Blackie Academic and Professional. London, U.K. (1996).
- Hoekstra, E., Hogendoorn, K. J. A., Wang, X., Westerhof, R. J. M., Kersten, S. R. A., van Swaaij, W. P. M. Fast pyrolysis of biomass in a fluidized bed reactor: In situ filtering of the vapors. Ind. Eng. Chem. Res. 48 (10), 4744-4756 (2009).
- Elliott, D. C., Wang, H., French, R., Deutch, S., Iisa, K. Hydrocarbon liquid production from biomass via hot-vapor-filtered fast pyrolysis and catalytic hydroprocessing of the bio-oil. Energy Fuels. 28 (9), 5909-5917 (2014).
- Howe, D., et al. Field-to-Fuel Performance Testing of Lignocellulosic Feedstocks: An Integrated Study of the Fast Pyrolysis/Hydrotreating Pathway. Energy Fuels. 29 (5), 3188-3197 (2015).
- Wang, H., Wang, Y. Characterization of Deactivated Bio-oil Hydrotreating Catalysts. Topics in Catalysis. 59, 65-72 (2015).