Abstract
Une microémulsion inverse est utilisée pour encapsuler des nanoparticules d'oxyde de métal de transition précoce monométalliques ou bimétalliques dans les coquilles de silice microporeux. Les nanoparticules d'oxyde métallique enrobé de silice sont ensuite cémentés dans une atmosphère de méthane / hydrogène à des températures au-dessus de 800 ° C pour former transition précoce nanoparticules de carbure de métal de silice-encapsulée. Au cours du processus de carburation, les coquilles de silice empêcher le frittage des nanoparticules de carbure adjacentes tout en empêchant le dépôt de carbone de surface en excès. En variante, les nanoparticules d'oxydes métalliques de silice encapsulées peuvent être nitridized dans une atmosphère d'ammoniac à des températures au-dessus de 800 ° C pour former des nanoparticules transition précoce de nitrure de métal de silice-encapsulée. En ajustant les paramètres de microémulsion inverse, l'épaisseur des coquilles de silice, et les conditions de carburation / nitruration, carbure ou nitrure des nanoparticules de métaux de transition peuvent être réglés à différentes tailles, des compositions, unphases cristallines ND. Après carburation ou nitruration, les coquilles de silice sont ensuite retirés en utilisant soit une solution de bifluorure d'ammonium aqueuse à température ambiante ou de 0,1 à 0,5 M de solution de NaOH à 40-60 ° C. Bien que les coquilles de silice se dissolvent, un support de surface spécifique élevée, tel que le noir de carbone, peut être ajouté à ces solutions pour obtenir transition précoce carbure ou nitrure métallique des nanoparticules supportées. Si aucun support de grande surface est ajouté, puis les nanoparticules peuvent être stockés comme une nanodispersion ou centrifugés pour obtenir un nanopoudres.
Introduction
Carbures début de métaux de transition (TMC) sont à faible coût, matériaux de terres abondantes qui présentent une stabilité thermique et électrochimique de haute ainsi que des activités catalytiques uniques 1-3 en particulier., Carbure de tungstène (WC) et le carbure de molybdène (Mo 2 C) ont été largement étudiés pour leurs similitudes catalytique pour les métaux du groupe platine (MGP). 4,5 En raison de ces propriétés favorables, les agences de voyages ont été identifiés comme candidats pour remplacer les catalyseurs de PGM coûteux dans les technologies d'énergies renouvelables, telles que la conversion de la biomasse, piles à combustible émergents, électrolyseurs et 6,7.
Pour maximiser l'activité catalytique, les catalyseurs commerciaux sont presque toujours formulés sous forme de nanoparticules ultrapetites (diamètres <10 nm) dispersés sur un support de grande surface, comme le noir de carbone. 8 Cependant, la synthèse du TMC nécessite des températures supérieures à ~ 700 ° C. Cela conduit à une vaste frittage du nanoparticles (IP), dépôt excès de carbone de surface (de coke), et la dégradation de support thermique. Les deux frittage des particules et de la dégradation de soutien conduisent à une diminution des zones de surface du matériau. L'excès d'impuretés de la surface des blocs de dépôt des sites métalliques actifs, ce qui a permis de réduire considérablement ou dans certains cas, d'éliminer complètement l'activité catalytique du PTM. 9,10 Par conséquent, l'étude fondamentale de TMC réactivité est principalement réalisée sur des microparticules en vrac ou des films minces avec surfaces finement contrôlée plutôt que sur grande surface nanomatériaux TMC.
De nombreuses méthodes ont été développées pour synthétiser TMC IP, mais ces méthodes ne sont pas adaptés pour synthétiser IP TMC activité catalytique. Techniques d'imprégnation humides traditionnelles utilisent des solutions de sels métalliques imprégnées sur un support de grande surface. En cas d'échauffement, des procédés d'imprégnation par voie humide peuvent exposer le support de catalyseur à des conditions de carburation destructeurs conduisant à la dégradation de l'appui. En outre, le frittage cun seul être atténués à faibles charges% en poids du métal sur le support, et il est également impossible de synthétiser nanopoudres TMC non pris en charge en utilisant l'imprégnation humide. Plusieurs méthodes actuellement disponibles consistent à mélanger un précurseur de métal avec un précurseur de carbone et l'application de techniques de chauffage classiques et non classiques. 11-18 carbone en excès est utilisé pour empêcher le frittage, mais cet excès résultats de carbone dans une vaste carbone de surface, ce qui rend ces matériaux ne conviennent pas pour les applications catalytiques.
En raison de ces défis synthétiques, les agences de voyages ont toujours été étudiés en tant que co-catalyseurs 11 pour les PGM, supports de catalyseur pour les PGM, 19-22 ou supports pour des monocouches de PGM actifs. 23-25 La méthode présentée ici offre la possibilité de synthétiser à la fois non-fritté et de nitrure de métal de transition (TMN) Les IP avec des tailles accordables, des phases cristallines, et la composition métallique. 26 fin métal TMC IP ainsi que la méthode présentée offre également l'abilité d'obtenir TMC ou RGT nanodispersions ou déposer les TMC et TMN IP sur un support de catalyseur de grande surface à la température ambiante, ce qui atténue la dégradation de support thermique. Cette méthode est donc adapté pour les applications catalytiques autonomes de TMC et TMN IP, le développement de pointe multimétallique TMC et TMN IP, ou d'autres applications nécessitant des tailles et des surfaces de particules finement contrôlées. 26
La méthode présentée ici utilise un protocole en trois étapes pour synthétiser TMC et TMN IP. Dans la première étape, d'une microémulsion inverse (RME) est utilisé pour enrober oxyde de métal de transition précoce (TMO) IP dans les nanosphères de silice. L'émulsion est préparée en dispersant des gouttelettes d'eau dans un milieu non polaire en utilisant un tensioactif non ionique commercial. Les TMO silice IP encapsulés sont ensuite soumis à une ou l'autre cémentation ou traitements thermiques de nitruration. Ici, la silice empêche le frittage des particules à hautes températures tout en permettant aux gaz réactifs de diffuser à til TMO IP et de les convertir à TMC ou RGT NPS. Dans l'étape finale, les coquilles sont enlevées de silice en utilisant soit un traitement acide ou alcalin pour obtenir TMC ou RGT nanodispersions qui peut être dispersé sur un support de surface spécifique élevée, tels que le noir de carbone.
Subscription Required. Please recommend JoVE to your librarian.
Protocol
1. Synthèse de silice monométallique-encapsulé ou bimétallique Metal Oxide nanoparticules
- Préparation de la microémulsion inverse
- Ajouter 240 ml de n-heptane anhydre à un propre, séché au four 1 L ballon à fond rond (RBF) contenant une barre d'agitation magnétique séché au four en utilisant un cylindre propre, séché au four graduée.
- Ajouter 54 ml de polyoxyéthylène (4) lauryl éther au n-heptane sous agitation constante.
Remarque: En raison de la viscosité élevée et une faible tension de surface de ce tensioactif, un endroit propre, sec seringue de 60 ml doit être utilisé pour obtenir des volumes précis au lieu d'un cylindre gradué. - Ajouter 7,8 ml de ultrapure, déminéralisée (DI) de l'eau sous agitation constante à l'aide d'une pipette. Sceller le RBF avec un bouchon de caoutchouc et de la cire Parafilm. Laissez le RME mélanger pendant au moins 10 min.
- Ajouter 0,1 à 0,5 ml de réactif de qualité NH4OH à l'émulsion si l'on veut réduire le temps d'hydrolyse.
Remarque: Certains précurseurs alcoxydes de métal hydroélectriqueslyser lentement à pH neutre. Laissez le RME mélanger pendant au moins encore 10 min après l'ajout de NH 4 OH. A titre d'exemple représentatif, en ajoutant 0,5 ml de NH 4 OH est recommandé pour les synthèses impliquant titane (IV) isopropylate.
- Préparation d'un précurseur d'alcoxyde de métal, de l'alcool, et le n-heptane solution
- Connectez un propre, 250 ml RBF séché au four à une ligne de Schlenk et rincer avec de l'azote. Sinon, placez le nettoyage, 250 ml RBF séché au four dans une boîte à gants d'azote sec.
- Ajouter 12 ml de 5% p / v de tungstène isopropoxyde (OMPI) dans l'isopropanol en utilisant une seringue propre et sec. A ce stade, d'autres alcoolates de métaux peuvent également être ajoutés, tels que le tantale (V) isopropoxyde (Taipo), le molybdène (V) isopropoxyde (MoIPO), de niobium (V) isopropoxyde (NbIPO), le titane (IV) isopropylate (tiipo), nickel (II) méthoxyéthoxyde (NiMEO), le cobalt (II) isopropoxyde (Coipo), etc.
Remarque: les alcoolates métalliques peuvent être achetés dans le commerce ou synthétisés par l'addition d'un anhydronous alcool en le sel de chlorure de métal correspondant en utilisant un tube de Schlenk, comme décrit ailleurs. (Attention: la synthèse de l'alcoolate de métal à partir du chlorure de métal rejets gazeux et du HCl doivent être effectuées dans une hotte bien ventilée) 27 - Utilisation d'un propre, séché à l'étuve canule, transférer 120 ml de n-heptane anhydre à 250 ml le RBF contenant la solution d'alcoolate de métal
- Utilisation d'un propre, séché au four canule, transférer la solution alcoxyde de métal-alcool n-heptane dans le RME sous agitation constante sur la durée de 10 min.
Remarque: Pour alcoxydes métalliques qui réagissent vigoureusement avec de l'eau, comme le tellure (IV) isopropylate, un taux de goutte à goutte beaucoup plus lent de plus est nécessaire. La solution finale doit être optiquement clair quel que soit le précurseur d'alcoxyde de métal utilisé, mais peut être de différentes couleurs selon les alcoolates de métaux utilisés et leurs états d'oxydation. Nous notons que si l'émulsion est transparente ou translucide est dépendante de la taille des particulestandis que la couleur dépend de l'état d'oxydation du métal. - Après 4 h, utiliser une seringue propre et sec pour injecter 1,4 ml de qualité réactif NH 4 OH dans la solution goutte à goutte. Puis, en utilisant une autre seringue propre, sec, injecter 1,2 ml de tétraéthyle qualité réactif (TEOS) goutte à goutte.
Note: l'hydroxyde de sodium (NaOH) ne doit pas être utilisé car il peut conduire à la densification des coquilles de silice au cours de la carburation / nitruration et entraîner des impuretés de sodium dans le réseau des nanoparticules finales. Résiduel NH4OH d'autre part se décompose facilement au cours des traitements thermiques. - Après 16,5 heures, retirer le bouchon de caoutchouc et utiliser un cylindre propre, sec diplômé d'ajouter 300 ml de méthanol à la solution sous agitation constante.
- Après 10 min d'agitation, supprimer la barre d'agitation et laisser la solution pour régler.
Remarque: Il y aura deux phases liquides présentes: une phase supérieure heptane riche et une phase inférieure riche en méthanol. La silice encapsulée métallique oXide nanoparticules, désignés en tant que SiO 2 / MO x vont sédimenter au fond du ballon à partir de la phase inférieure. - Après 1 h, décanter les phases liquides dans un conteneur de déchets organiques et de recueillir la phase solide SiO 2 / MO x dans 50 ml tubes à centrifuger propres.
Remarque: si des tubes en polypropylène ou du polystyrène centrifugeuses sont utilisées, le précipitant ne peut pas être stocké à long terme dans cet état que l'heptane résiduel se dissoudre lentement le tube de centrifugeuse, l'amenant à allongée. En outre, NH 4 OH résiduelle et TEOS peuvent causer le SiO 2 de continuer à croître au-delà de ce qui a été souhaitée. - Centrifugeuse SiO 2 / MO x phase à 2056 g pendant 5 min, puis décanter le surnageant dans un récipient de déchets organiques.
- Ajouter 10-30 ml d'acétone à chaque tube centrifuge de 50 ml et disperser la poudre dans de l'acétone par agitation ou sonication. Cela permet de supprimer l'excès de tensioactif avant la calcination.
- Centrifuge x et l'acétone mélange SiO 2 / MO à 4626 g pendant 10 min, puis décanter le surnageant dans un récipient de déchets organiques. Laisser le 2 / MO x gel de SiO sécher pendant la nuit.
2. Traitement thermique de la poudre synthétisée
Attention Déclaration: hydrogène, de méthane et d'ammoniac gazeux sont extrêmement inflammables. Le gaz ammoniac est toxique. Une fuite vérification approfondie doit être effectuée avant que tous les traitements thermiques, les traitements et doit être effectué dans un four tubulaire de quartz maintenu dans une hotte bien ventilée avec un barboteur à huile à la sortie de gaz. Toutes les bouteilles de gaz devraient être équipés de pare-flammes et entreposés loin de la fournaise. Si requis par les règlements de droit ou institutionnels, de l'ammoniac gazeux en excès doit être mis à barboter dans un grand volume d'eau et soit jeté comme un déchet de base ou neutralisée à une solution de chlorure d'ammonium pH 7 avec HCl.
- Calcination du SiO 2 / MO x powder dans l'air
- Crush the SiO 2 / MO x gel séché en une poudre fine en utilisant une barre d'agitation de verre ou de mortier et d'un pilon. Mettez la poudre dans des bateaux de creuset d'alumine et de la charge dans un four de quartz-tube.
- Avec un taux de chauffage de 2 ° C / min, calciner le SiO 2 / MO x poudre sous 100 sccm d'air à 450 ° C pendant 1 heure. Ceci supprime tout tensioactif résiduel et augmente également la microporosité des coquilles de silice. Après le four a refroidi, retirez les calcinés SiO 2 / MO x poudres et magasin dans des conditions ambiantes.
- Carburation du SiO 2 / MO x poudre dans un / atmosphère d'hydrogène en méthane
- Chargez le calciné SiO 2 / MO x poudre dans un creuset d'alumine bateau non vernissée et le placer dans un four de quartz-tube. Rincez le four quartz tube avec de l'azote pendant au moins 30 min pour éliminer l'oxygène. Effectuez une vérification de fuite en pulvérisant tous les joints avec de l'eau savonneuse.
- Utilisation d'un2 ° le taux de chauffage C / min, carburer le SiO 2 / MO x poudre sous 120 sccm d'hydrogène et 33 SCCM de méthane à 850 ° C pendant 4 heures pour former SiO 2 / MC x.
- Après 4 h, arrêter le flux de méthane et de maintenir la poudre à 850 ° C pendant 1 h en seulement 120 sccm d'hydrogène à piéger tout carbone de surface en excès.
- Laisser le four refroidir lentement à température ambiante sous 120 sccm d'hydrogène. Ensuite, rincez le four avec de l'azote pendant au moins 30 minutes pour éliminer l'hydrogène.
- Débit de 95 sccm d'azote et de 5 sccm de l'air sur la poudre pendant 3 heures pour passiver lentement les carbures avant l'exposition à l'air.
- Retirez le SiO 2 / MC x poudre du four et conserver dans un dessicateur sous vide ou dans une boîte à gants sèche d'azote pour empêcher l'oxydation de vrac à long terme des nanoparticules de carbure de métal dans l'air.
- Nitruration du SiO 2 / MO x poudre dans une atmosphère d'ammoniac
- Load SiO 2 / MO x poudre calcinée dans un bateau creuset d'alumine et le placer dans un four de quartz-tube.
- Rincez le four quartz tube avec de l'azote pendant au moins 30 min pour éliminer l'oxygène.
- En utilisant une vitesse de chauffage de 2 ° C / min, la nitridize SiO 2 / MO x 100 sccm sous une poudre de l'ammoniac à 800 ° C pendant 4 heures pour former SiO 2 / MN x.
- Laisser le four refroidir lentement jusqu'à la température ambiante. Ensuite, rincez le four avec de l'azote pendant au moins 30 min pour éliminer l'ammoniac.
- Débit de 95 sccm d'azote et de 5 sccm de l'air sur la poudre pendant 3 heures pour passiver lentement les nitrures avant l'exposition à l'air.
- Retirez le SiO 2 / MN x poudre du four et conserver dans un dessicateur sous vide ou dans une boîte à gants sèche d'azote pour empêcher l'oxydation de vrac à long terme des nanoparticules de nitrure de métal dans l'air.
3. Retrait des coquillages de silice et soutenir la Nanoparticules
Attention Déclaration: bifluorure d'ammonium (ABF) est hautement toxique. Il ne doit être manipulé dans une hotte bien ventilée en utilisant un équipement de protection individuelle approprié, y compris des gants caoutchouc butyle, un écran facial et une blouse de HF résistant à manches HF-résistant. Verre et de l'équipement de laboratoire en métal ne doivent jamais être utilisés lors de la manipulation ABF.
- Dissolution de la silice dans Bifluorure d'ammonium pour stable en milieu acide carbures et nitrures métalliques (tels que les WC et W 2 N)
- Peser 200 mg de SiO 2 / MC x ou SiO 2 / MN x et mettre dans un contenant pouvant être scellé en polypropylène de 30 ml avec une barre d'agitation magnétique revêtue de téflon.
- Si l'on souhaite soutenir des nanoparticules sur un support de catalyseur de surface spécifique élevée, tels que le noir de carbone ou des nanotubes de carbone, peser la matière et l'ajouter dans le récipient de polypropylène scellable.
Remarque: La masse pèse dépendra de la charge souhaitée des nanoparticules sur esupport e. Pour les supports de catalyseur qui ne sont pas stables dans ABF, tels que l'alumine, le support peut être ajouté après que la silice a été éliminée et la ABF est neutralisé. En l'absence de support est ajouté, une nanodispersion sera obtenu. - Ajouter 20 ml d'eau désionisée ultrapure et commencer à mélanger pour former une suspension. Alternativement, ajouter 20 ml de solution pré-faites 20% ABF.
- Peser 5 g de ABF, puis ajouter au mélange sous agitation. Une fois ajouté, sceller le récipient de polypropylène.
Note: Dissolution des ABF dans l'eau est endothermique, de sorte que la température de la solution va baisser. - Afin d'assurer une dissolution complète de la silice et une bonne dispersion des nanoparticules sur le support de catalyseur, arrêter la réaction après 16 heures en ajoutant de qualité réactif NH4OH goutte à goutte à la solution ABF neutraliser à un pH de 6-7. Attention: cette réaction est exothermique.
- Vider le mélange neutralisé dans un tube de centrifugation et centrifuger à 2056 g pendant 10 min.
- Vider le Supernatant dans un conteneur à déchets alcaline (pour assurer la neutralisation totale) et redisperser la poudre de catalyseur dans 20 ml d'eau ultra-pure de DI.
- Centrifuger à 4626 g pendant 10 min, jeter le surnageant, et faire une dernière 20 ml d'eau de rinçage DI. Jusqu'à 12 850 xg peut être nécessaire pour les nanoparticules non pris en charge.
- Séchez la poudre sous vide et ensuite le stocker dans un dessicateur sous vide ou une boîte à gants sèche d'azote pour empêcher l'oxydation de vrac à long terme du carbure ou nitrure métallique nanoparticules.
- Dissolution de la silice en hydroxyde de sodium pour carbures alcalins stables et des nitrures (tels que les TAC et Ta 3 N 5)
- Peser 200 mg de SiO 2 / MC x ou SiO 2 / MN x et mettre dans un 50 ml RBF en verre avec une barre d'agitation magnétique. Peser et ajouter un support de catalyseur, si désiré.
- Ajouter 30 ml d'au moins 0,1 M solution aqueuse de NaOH. Fixez un condenseur à la RBF ou sceller avec un bouchon de caoutchouc et de la cire Parafilm.
- On chauffe à 60 ° C sous agitation constante pendant 16 heures. Après refroidissement, centrifuger la solution à 2 056 g pendant 10 min.
- Vider le surnageant dans un conteneur à déchets alcaline et redisperser la poudre de catalyseur dans 20 ml d'eau ultra-pure de DI.
- Centrifuger à 4626 g pendant 10 min, jeter le surnageant, et faire une dernière 20 ml d'eau de rinçage DI. Jusqu'à 12 850 xg peut être nécessaire pour les nanoparticules non pris en charge.
- Séchez la poudre sous vide et ensuite le stocker dans un dessicateur sous vide ou une boîte à gants sèche d'azote pour empêcher l'oxydation de vrac à long terme du carbure ou nitrure métallique nanoparticules.
Subscription Required. Please recommend JoVE to your librarian.
Representative Results
Dans la première étape du protocole, l'objectif est d'encapsuler le monométallique ou bimétallique oxyde de métal de transition (TMO) IP au sein de sphères de silice microporeux. La figure 1 montre des images prises de synthèses représentatives avant et après la précipitation avec du méthanol. Deux résultats morphologiques reproductibles ont été observées au cours de cette étape qui semblent être dépendantes des métaux utilisés dans la synthèse: PN TMO peuvent être individuellement revêtues d'une sphère de silice (figure 2b) ou plusieurs IP TMO peut être revêtue à l'intérieur d'une sphère de silice unique (figure 2a). IP TMO Singly revêtus ont été observés pour des synthèses utilisant Ti, Ta et Nb, tout recouvert de plusieurs couches IP TMO ont été observés pour Mo et W. Il est possible de synthétiser ces métaux également dans les formulations seuls revêtus en effectuant l'alcoxyde de métal hydrolyse à pH élevé. Le tableau 1 présente les résultats pour contrôler la taille des particules et la composition en utilisant le RME.Nous émettons l'hypothèse que, à pH élevé, le taux de croissance NP est plus élevé, et les grandes NPS peut plus facilement nucléer SiO 2 croissance de la sphère (Figure 6c, d). A faible pH, certains alcoolates de métaux hydrolysent très lentement, ce qui entraîne dans les noyaux TMO ultrapetites que finalement devenir SiO 2 incorporés dans les sphères (figure 6a, b).
La composition métallique de la TMO IP est contrôlé par les alcoolates ajoutés à la RME et si elles sont mélangées ensemble (comme indiqué dans le protocole donné) ou ajoutés successivement métalliques. Par exemple, Taipo peut être mélangé avec de l'heptane et de l'OMPI avant l'injection dans la RME, ou un Taipo / mélange heptane peut être injecté dans la RME 4 heures après un mélange OMPI / heptane a été injecté et on a laissé l'hydrolyse.
De nombreuses variables doivent être considérées pour contrôler la taille de PN TMO. Le premier ensemble de variables est la sélection de l'agent tensioactif et la phase huileuse. Ici, l'eau / n-heptanee système / Brij-L4® a été choisi en raison de sa large fenêtre de stabilité et la capacité de synthétiser des nanoparticules de très petites. Alternativement, l'eau / n-heptane / Igepal CO-520® peut être utilisé si grandes TMO IP sont désirée comme montré dans la figure 3. Alternativement, on peut modifier les taux de nucléation vs croissance en ajoutant NH 4 OH à la RME avant métallique addition alcoolate, ce qui entraîne de plus grands IP comme représenté sur la figure 6c, et d, et décrit dans le tableau 1. Une fois que le système de RME est choisie, la première série de variables qui contrôlent la taille TMO peuvent être regroupés en tant que paramètres de contrôle RME. Ceux-ci comprennent le rapport eau: agent tensio-actif, l'huile: rapport de l'eau, de l'huile: surfactant rapport, la température de la RME, et l'étendue de mélange convectif. Ces paramètres déterminent la taille des gouttelettes d'eau en suspension, de leur proximité les uns aux autres au sein de l'émulsion, leur polydispersité moyenne, und les taux de coalescence des gouttelettes et de la séparation.
La dernière série de variables qui influent sur la taille TMO NP peut être classé comme alcoolate de métal paramètres de contrôle d'hydrolyse. Ceux-ci comprennent l'alcoxyde de métal: rapport molaire de l'eau, la durée de l'alcoxyde de métal est autorisé à hydrolyser avant d'initier le revêtement de silice, le pH des gouttelettes d'eau, la température et la vitesse d'addition de l'alcoolate de métal dans le système RME.
En fin de compte, l'objectif de cette méthode est de produire des nanoparticules non-frittés et terminé métal TMC et TMN (appelés TMCN IP pour plus de commodité). L'obtention de ce résultat repose sur la synthèse de revêtements de silice microporeux à haute stabilité thermique qui inhibent également le frittage de TMC et TMN nanoparticules. Pour atteindre ce résultat, il existe deux ensembles de variables qui doivent être considérés: variables de contrôle qui affectent la stabilité thermique de la silice, et les variables de commande qui affectent la taille des particules di TMCNstribution (PSD).
Lors du chauffage, de la silice microporeuse peut passer à des phases denses et, finalement, au quartz, ce qui rend difficile d'obtenir TMCN IP __gVirt_NP_NN_NNPS<__ élimination pure et peut faire l'enlèvement de silice plus difficile. Afin de maximiser la stabilité thermique des revêtements de silice, il a été observé que le pH élevé est requis au cours de TEOS hydrolyse et que les PN SiO 2 / TMO doit être précipité à partir de la RME en utilisant du methanol par rapport aux autres agents de précipitation commun telles que l'acétone ou isopropanol. La figure 4 montre les diffractogrammes de poudre par rayons X (PXRD) de carburé SiO 2 / WO x matériaux ayant des revêtements de silice effectués à différentes valeurs de pH tandis que la figure 5 montre PXRD diffractogrammes de SiO 2 / WO x matériaux carburés avec les revêtements de silice réalisées à mais le même pH précipité avec trois solvants différents. TEOS hydrolyse à pH élevé a été démontré que conduire à un nombre élevé de undercoordinQ2 et Q3 emplacements est situé, résultant en un volume de micropores supérieur. 28 L'influence de l'agent de précipitation sur la stabilité thermique de la silice est mal connue, mais les images TEM suggèrent que la floculation avec du methanol conduit à moins agrégées flocons de SiO 2 / TMO par rapport à l'acétone et l'isopropanol (résultats non montrés). Nous trouvons des éléments étayant cette hypothèse à partir d'images TEM de SiO 2 / flocs TMO précipités avec moins que la quantité recommandée de méthanol dans la procédure. Pour les synthèses floculées avec moins de methanol, les flocs apparaissent plus agrégée et la silice est moins stable, la transition vers des domaines de quartz semblable à des températures plus basses que lorsque l'excès de methanol est utilisé pendant l'étape de floculation (résultats non montrés).
Le TMCN PSD est contrôlé par la taille des premières TMO IP ainsi que la nanostructure de silice. En théorie, si TMCN frittage peut être complètement atténuée par les coquilles de silice dans des conditions de carburation / nitruration de, la TMCNPSD sera entièrement contrôlé par le PSD TMO initiale, ajustée par la différence de densité entre le hydraté, treillis initiale amorphe TMO et la TMC cristalline finale ou TMN treillis. Un tel résultat a été obtenu en utilisant étroitement coquilles de silice d'épaisseur avec des exemples représentatifs présentés dans la figure 6c, et d.
Si le frittage est pas entièrement atténué, le PSD finale TMCN sera contrôlée à la fois par le PSD initiale TMO et le revêtement de silice. Ceci est particulièrement vrai pour des revêtements minces de silice ou de ultrapetites 1-2 nm IP TMO qui peuvent plus facilement se diffuser à l'intérieur des revêtements de silice. Un exemple représentatif est présenté à la figure 6a et 6b. Ici, la même initiale 2.1 nm TMO PSD est utilisé, mais le revêtement de silice est modifié de 50 nm à 35 nm. Dans le revêtement de silice dense, le frittage est atténué et un PSD 1-2 nm TMC est obtenu alors que dans le revêtement de silice fine, le frittage est seulement partiellement atténué et un2-3 nm résultats TMC PSD. Notez que certains frittage est présente à la surface de la silice sphères post-carburation, que nous attribuons aux petites IP TMC lié à la surface qui peut diffuser latéralement à travers la surface des sphères de silice et d'aggloméré.
Après carburation, il a été observé que pour les IP TMCN multiplication-enrobés, les revêtements de silice sphérique restent avec un minimum de frittage de la silice (Figure 6a et 6b). En revanche, pour les IP TMCN seuls revêtus, les revêtements de silice fritter ensemble (Figure 6c et 6d). Nous émettons l'hypothèse que les IP TMCN multiplication-revêtues fournissent une intégrité structurelle pour les sphères de silice à des températures élevées, ce qui empêche le frittage des sphères de silice. Bien que ce soit pas le cas pour les infirmières praticiennes TMCN seuls revêtus, le frittage des sphères de silice n'a pas été observée pour inhiber la capacité des revêtements de silice à la fois empêcher le frittage des IP TMCN tout en permettant également carbuRizing nitruration ou molécules de gaz de diffuser à travers eux (figure 6c et 6d). PXRD diffractogrammes ont été inclus dans la Figure 8 pour diverses précoce carbure de métal de transition et de nitrure nanoparticules monométalliques et hétérométalliques de différentes tailles.
Dissolution des IP TMCN sur du noir de carbone (CB) conduit comme Vulcan XC-72R à bien dispersée, soutenu IP. Un résultat représentatif est montré sur la figure 7c. En variante, si aucun support est ajouté, une nanodispersion suspension noire est obtenue comme représenté sur la figure 7a. Parce que pas de surface agents stabilisants sont ajoutés pendant ou après la dissolution, le NPS TMCN former de petits agrégats en solution, un exemple représentatif de ce qui est représenté sur la figure 7b.
Résultat expérimental | Précurseurs | > Volume (ml) | Initial NH 4 OH (ml) | Finale NH 4 OH (ml) | TEOS (ml) |
1-2 nm WC | W (VI) IPO (5% p / v) | 12 | 0 | 2.7 | 1.2 |
2-3 nm WC | W (VI) IPO (5% p / v) | 12 | 0 | 1.4 | 0,6 |
6-8 nm WC | W (VI) IPO maison (5% p / v) | 12 | 0,4 | 1.4 | 1.6 |
7-10 nm WC | W (IV) IPO maison (6,5% p / v) | 8.8 | 1.4 | 1.4 | 1.6 |
9-13 nm WC | W (IV) IPO maison (6,5% p / v) | 10.2 | 1.4 | 1.4 | 1.6 |
6.4 nm Ti 0,1 O 0,9 C | W (VI) IPO (5% p / v) | 10,8 | 0,7 | 1.4 | 0,6 |
Ti (IV) IPO (5% p / v) | 0,7 | ||||
7-10 nm (0,3 Ni 0,7 O) 2 C | W (VI) IPO (5% p / v) | 8.4 | 0,4 | 1.4 | 0,6 |
Ni (II) MEO (5% p / v) | 1.4 |
Tableau 1:. Contrôle de la taille des particules TMC en contrôlant les paramètres de RME * Initial NH 4 OH est si NH4OH a été ajoutée à l'émulsion avant alcoolate de métal hydrolyse pendant finale NH 4 OH est le nombre total de NH 4 OH présent dans l'émulsion avant TEOS est injecté.
Figure 1: Repres repré- images de synthèses RME contenant SiO 2 / TMO IP immédiatement avant (A - C) et après (D, F) l'addition de 300 ml de methanol. (A) montre une synthèse de SiO 2 / WO x, (b) montre un rapport SiO 2 / Mo 0,06 W 0,94 O x synthèse, et (C) montre un SiO 2 / Mo 0,54 W 0,46 O x synthèse tout (D) et (E) correspond à différents angles de vue de la SiO 2 / WO x synthèse après l'addition de methanol. En (D) et (E), la phase supérieure est la phase liquide riche en l'heptane, la phase liquide inférieure est riche en méthanol, et au fond de la fiole comprennent le rapport SiO 2 / WO x flocs. Re-imprimer avec la permission de référence 26.
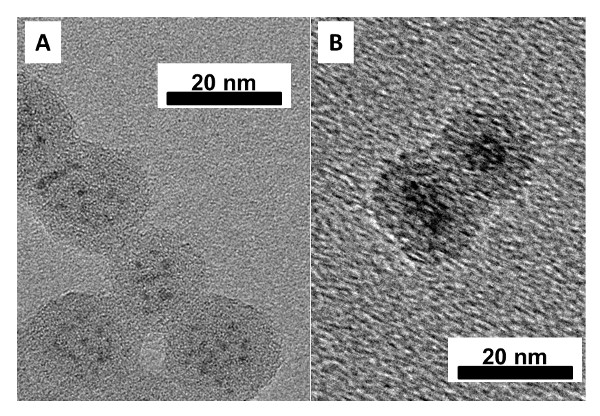
Figure 2: des images représentant de TEM (A) recouvert de plusieurs couches WO x IP au sein de SiO 2 sphères et (B) seuls revêtu Ta 0,3 W 0,7 x O IP au sein de SiO 2 sphères. Les barres d'échelle sont en nanomètres. Modifié de référence 26.
Figure 3: images TEM représentant de SiO 2 / WO x synthétisé dans des conditions identiques décrites dans la procédure, sauf avec 60 ml de Igepal® CO-520 au lieu de 54 ml de l'agent tensioactif Brij-L4 La barre d'échelle est en nanomètres.. Modifié de référence 26.
Figure 4: diffractogrammes de PXRD représentatif de SiO 2 / WO x appliquée à différentes valeurs de pH Carburizations ont été effectuées à 835 ° C pendant 4 heures sous 21% de CH 4 / H 2 et sont indiqués pour les matériaux enrobés à l'aide d'un pH de (A) 10. , (B) 10,5 (C) 10,9, et (D) 11,1. Les synthèses de pH bas (A et B) ont la silice de quartz-like (indiquée par le pic pointu à 22 °) et de multiples phases de carbure tandis que les synthèses de pH élevé (C et D) ont un large pic centré à 22 °, ce qui indique amorphe silice et monophasé visage cubique centrée IP WC. Re-imprimer avec la permission de référence 26.
Figure 5: solvants études sur les effets de précipitation par PRecipitating SiO 2 / WO x ou SiO 2 / Mo x W 1-x O y avec (A) méthanol, (B) l'acétone, et (C) Isopropanol. Toutes les matières ont été rincées avec de l'acétone après la précipitation. Les diffractogrammes de PXRD sont pour le matériel résultant de post-carburation à 835 ° C pendant 4 heures sous 21% de CH 4 / H 2. Re-imprimer avec la permission de référence 26.
Figure 6: Représentant TEM et STEM HAADF images de (A) 1-2 nm de SiO 2 / WC IP post-carburation, (B) 2-3 nm de SiO 2 / WC IP post-carburation, (C) 7-10 nm SiO 2 / WC IP post-carburation, (D) 9-13 nm de SiO 2 / WC IP post-carburation. Les barres d'échelle sont en nanomètres. Modified de référence 26.
Figure 7: (A) des photographies d'un WC nanodispersion hexagonale dispersé dans l'eau à 7,5 mg / ml avant et après trois semaines de la séance dans les conditions ambiantes stagnantes, (B) de l'image représentant STEM HAADF d'une non prise en charge nanopoudres β-WC, (C ) image représentative STEM HAADF de β-WC IP pris en charge sur le noir de carbone à 25% en poids. Les barres d'échelle sont en nanomètres. Modifié de référence 26.
Figure 8: diffractogrammes PXRD de monométallique de silice-encapsulé et hétérométalliques transition début carbures et nitrures métalliques de différentes tailles. Tous ont été TMNs nitridized moins de 100 SCCM NH 3à 800 ° C pendant 4 heures. 3.2 nm de SiO 2 / W 2 C a été synthétisé à 775 ° C sous 18% de CH 4 / H 2 pendant 4 heures tandis que la totalité du <3 nm TMC IP ont été synthétisés à 835 ° C sous 21% de CH 4 / H 2 . Les grandes TMC IP ont été synthétisés à 900 ° C sous 21% de CH 4 / H 2. Modifié de référence 26.
Subscription Required. Please recommend JoVE to your librarian.
Discussion
Un mode opératoire pour la synthèse non-fritté, en métal terminé carbure de métal de transition et de nitrure de nanoparticules dont la taille et la structure accordables est présenté ici 26 Les étapes critiques du procédé comprennent:. En utilisant un RBF exempt d'humidité à contenir le précurseur d'alcoxyde de métal dilué, en évitant métal alcalin des impuretés au cours de toutes les étapes de précipitation, la RME avec un excès de methanol au lieu de l'acétone ou de l'isopropanol, l'exécution d'un contrôle de fuite approprié avant cémentation ou nitruration des composants, et en utilisant EPP approprié lorsque l'on travaille avec le bifluorure d'ammonium.
La méthode peut être modifiée dans plusieurs domaines. Le PSD TMO peut être ajustée en utilisant différents systèmes de RME, l'eau différente: ratios de tensioactifs, différente alcoxyde de métal: ratios d'eau, différentes valeurs de pH, et différents temps d'hydrolyse. Le TMCN PSD peut être manipulé en manipulant le PSD TMO départ ainsi que par l'ajout de différentes quantités de NH 4 OH et de TEOS, en utilisant différent TEOS temps d'hydrolyse, et en utilisant différentes températures carburation / nitruration. La phase pureté cristalline des IP TMCN peut être manipulée en utilisant différentes températures et différentes vitesses de ligne centrale de gaz de cémentation / de nitruration. La composition des IP TMCN peut être ajustée en utilisant tout début alcoxyde de métal de transition hydrolysable, menant à un large éventail de potentiels multimétalliques TMC et TMN IP qui pourrait être synthétisé avec cette méthode.
Cette technique est plus approprié pour des applications de TMC et TMN IP qui exigent des particules non frittées de taille finement contrôlées qui présentent également des surfaces à terminaison métal. Cette technique est également approprié pour la facilité avec laquelle une variété de multimétalliques TMC et TMN IP peut être formulée. La technique est limitée par la stabilité thermique des revêtements de silice. TMC et TMN IP qui nécessitent des températures de carburation ou nitruration au-delà de 1000 ° C probablement pas peuvent être synthétisés par cette rencontréhod raison de l'effondrement thermique de la microporosité de silice à ces températures extrêmes. La technique est également limitée à TMC et TMN IP qui sont stables dans les deux bifluorure d'ammonium ou des solutions alcalines, soit comme un acide ou un traitement alcalin est nécessaire pour enlever les revêtements de silice après la carburation / nitruration.
En ce qui concerne les méthodes existantes pour synthétiser TMCN IP, cette méthode est unique dans sa capacité à atténuer simultanément frittage des particules et le dépôt d'impuretés de surface en excès. Il est également unique dans sa polyvalence pour synthétiser un large éventail de monométalliques et multimétalliques IP TMCN, exigeant seulement un précurseur hydrolysable d'alcoxyde de métal de transition précoce peut être acheté ou synthétisé. Bien que cette méthode est plus complexe que les synthèses humide imprégnation standard, il permet non fritté et TMCN IP pour être chargés sur un support de grande surface à la température ambiante et à toute% en poids de charge désirée fin-métal. Dans i humidempregnation synthèses, les supports de catalyseur doivent être exposés à des conditions de cémentation, conduisant à leur dégradation thermique et de faibles charges wt% doivent être utilisés pour atténuer le frittage des particules excessive.
Les orientations futures après l'apprentissage de cette technique comprennent l'exploration d'autres compositions multimétalliques, autre RME ou systèmes sol-gel, en utilisant des revêtements céramiques autres que la silice tels que l'alumine, la co-alimentation de gaz de carburation et de nitruration, et à l'aide d'autres précurseurs de gaz réactif pour faire par exemple des borures ou phosphures.
Subscription Required. Please recommend JoVE to your librarian.
Materials
Name | Company | Catalog Number | Comments |
n-heptane | Sigma-Aldrich | 246654 | |
polyoxyethylene (4) lauryl ether | Sigma-Aldrich | 235989 | Brij® L4 |
tungsten (VI) isopropoxide | Alfa Aesar | 40247 | W(VI)IPO |
tungsten (VI) chloride | Sigma-Aldrich | 241911 | To prepare W(VI)IPO, homemade |
tungsten (IV) chloride | Strem Chemicals | 74-2348 | To prepare W(IV)IPO, homemade |
tantalum (V) isopropoxide | Alfa Aesar | 40038 | Ta(V)IPO |
niobium (V) isopropoxide | Alfa Aesar | 36572 | Nb(V)IPO |
nickel (II) methoxyethoxide | Alfa Aesar | 42377 | Ni(II)MEO |
titanium (IV) isopropoxide | Sigma-Aldrich | 87560 | Ti(IV)IPO |
molybdenum (V) isopropoxide | Alfa Aesar | 39159 | Mo(V)IPO |
molybdenum (V) chloride | Sigma-Aldrich | 208353 | To prepare Mo(V)IPO, homemade |
tetraethyl orthosilicate | Sigma-Aldrich | 333859 | TEOS |
ammonium hydroxide | Sigma-Aldrich | 320145 | |
methanol | Sigma-Aldrich | 34860 | |
anhydrous isopropanol | Sigma-Aldrich | 278475 | To prepare homemade alkoxides |
ammonium bifluoride | Sigma-Aldrich | 224820 | |
carbon black | Cabot Corp. | Vulcan® XC72R | |
Methane | AirGas | ME R300 | |
Hydrogen | AirGas | HY UHP300 | |
Ammonia | AirGas | AM AH80N705 | |
Quartz Tube Furnace | MTI Corp. | OTF-1200X-S-UL |
References
- Oyama, S. T. The Chemistry of Transition Metal Carbides and Nitrides. , Blackie. (1996).
- Michalsky, R., Zhang, Y. -J., Medford, A. J., Peterson, A. A. Departures from the Adsorption Energy Scaling Relations for Metal Carbide Catalysts. J. Phys. Chem. C. 118 (24), 13026-13034 (2014).
- Kimmel, Y. C., Xu, X., Yu, W., Yang, X., Chen, J. G. Trends in Electrochemical Stability of Transition Metal Carbides and Their Potential Use As Supports for Low-Cost Electrocatalysts. ACS Catal. 4 (5), 1558-1562 (2014).
- Levy, R. B., Boudart, M. Platinum-like behavior of tungsten carbide in surface catalysis. Science. 181, 547-549 (1973).
- Chen, Z., Higgins, D., Yu, A., Zhang, L., Zhang, J. A review on non-precious metal electrocatalysts for PEM fuel cells. Energy Environ. Sci. 4 (9), 3167-3192 (2011).
- Esposito, D. V., Chen, J. G. Monolayer platinum supported on tungsten carbides as low-cost electrocatalysts: opportunities and limitations. Energy Environ. Sci. 4, 3900 (2011).
- Stottlemyer, A. L., Kelly, T. G., Meng, Q., Chen, J. G. Reactions of oxygen-containing molecules on transition metal carbides: Surface science insight into potential applications in catalysis and electrocatalysis. Surf. Sci. Rep. 67, 201-232 (2012).
- Bell, A. T. The impact of nanoscience on heterogeneous catalysis. Science. 299, 1688-1691 (2003).
- Kimmel, Y. C., Esposito, D. V., Birkmire, R. W., Chen, J. G. Effect of surface carbon on the hydrogen evolution reactivity of tungsten carbide (WC) and Pt-modified WC electrocatalysts. Int. J. Hydrogen Energy. 37, 3019-3024 (2012).
- Yang, X., Kimmel, Y. C., Fu, J., Koel, B. E., Chen, J. G. Activation of Tungsten Carbide Catalysts by Use of an Oxygen Plasma Pretreatment. ACS Catal. 2, 765-769 (2012).
- Garcia-Esparza, A. T., et al. Tungsten carbide nanoparticles as efficient cocatalysts for photocatalytic overall water splitting. ChemSusChem. 6, 168-181 (2013).
- Yan, Z., Cai, M., Shen, P. K. Nanosized tungsten carbide synthesized by a novel route at low temperature for high performance electrocatalysis. Sci. Rep. 3, 1646 (2013).
- Giordano, C., Erpen, C., Yao, W., Antonietti, M. Synthesis of Mo and W carbide and nitride nanoparticles via a simple 'urea glass' route. Nano Lett. 8, 4659-4663 (2008).
- Abdullaeva, Z., et al. High temperature stable WC1−x@C and TiC@C core–shell nanoparticles by pulsed plasma in liquid. R. Soc. Chem. Adv. 3, 513 (2013).
- Vallance, S. R., et al. Probing the microwave interaction mechanisms and reaction pathways in the energy-efficient, ultra-rapid synthesis of tungsten carbide. Green Chem. 14, 2184 (2012).
- Shen, P. K., Yin, S., Li, Z., Chen, C. Preparation and performance of nanosized tungsten carbides for electrocatalysis. Electrochim. Acta. 55, 7969-7974 (2010).
- Nikiforov, A. V., et al. WC as a non-platinum hydrogen evolution electrocatalyst for high temperature PEM water electrolysers. Int. J. Hydrogen Energy. 37, 18591-18597 (2012).
- Fang, Z. Z., Wang, X., Ryu, T., Hwang, K. S., Sohn, H. Y. Synthesis, sintering, and mechanical properties of nanocrystalline cemented tungsten carbide – A review. Int. J. Refract. Met. Hard Mater. 27, 288-299 (2009).
- Liu, Y., Kelly, T. G., Chen, J. G., Mustain, W. E. Metal Carbides as Alternative Electrocatalyst Supports. ACS Catal. 3, 1184-1194 (2013).
- Nie, M., Shen, P. K., Wei, Z. Nanocrystaline tungsten carbide supported Au–Pd electrocatalyst for oxygen reduction. J. Power Sources. 167 (1), 69-73 (2007).
- Ham, D. J., et al. Palladium-nickel alloys loaded on tungsten carbide as platinum-free anode electrocatalysts for polymer electrolyte membrane fuel cells. Chem Commun (Camb). 47 (20), 5792-5794 (2011).
- Yan, Y., et al. Template-free pseudomorphic synthesis of tungsten carbide nanorods. Small. 8, 3350-3356 (2012).
- Esposito, D. V., et al. Low-cost hydrogen-evolution catalysts based on monolayer platinum on tungsten monocarbide substrates. Angew. Chem. Int. Ed. 49, 9859-9862 (2010).
- Esposito, D. V., Hunt, S. T., Kimmel, Y. C., Chen, J. G. A new class of electrocatalysts for hydrogen production from water electrolysis: metal monolayers supported on low-cost transition metal carbides. J. Am. Chem. Soc. 134, 3025-3033 (2012).
- Kelly, T. G., Hunt, S. T., Esposito, D. V., Chen, J. G. Monolayer palladium supported on molybdenum and tungsten carbide substrates as low-cost hydrogen evolution reaction (HER) electrocatalysts. Int. J. Hydrogen Energy. 38, 5638-5644 (2013).
- Hunt, S. T., Nimmanwudipong, T., Roman-Leshkov, Y. Engineering non-sintered, metal-terminated tungsten carbide nanoparticles for catalysis. Angew. Chem. Int. Ed. Engl. 53 (20), 5131-5136 (2014).
- Mehrota, R. C. Alkoxides and Alkylalkoxides of Metals and Metalloids. Inorg. Chim. Acta. 1, 99-112 (1967).
- Munoz-Aguado, M., Gregorkiewitz, M. Sol-Gel Synthesis of Microporous Amorphous Silica from Purely Inorganic Precursors. J. Colloid Interface Sci. 185, 459-465 (1997).